富士フイルムグループは、2040年度までに自社が使用するエネルギー起因のCO2排出を実質的にゼロとするとともに、原材料調達から製造、輸送、使用、廃棄に至るまでの自社製品のライフサイクル全体において、2030年度までにCO2排出量50%削減(2019年度比)を目指しています。本目標の達成に向け、富士フイルムグループ環境戦略「Green Value Climate Strategy」のもと環境負荷の少ない生産活動や優れた環境性能を持つ製品・サービスの創出・普及を推進していきます。
各拠点における取り組み
使用電力を風力発電由来に転換
(FUJIFILM Manufacturing Europe B.V./オランダ)
写真用カラーペーパーや、バイオ医薬品の研究開発・製造における細胞培養に不可欠な培地などの製造、および複合機のトナーカートリッジの回収・再生を行う、オランダ・チルバーグ市にあるFUJIFILM Manufacturing Europeでは、再生可能エネルギーの1つである風力発電由来の電力で使用電力のすべてをまかなっています。具体的には、2011年に敷地内に設置した5基の風力発電機を通じて35%の電力を確保(2024年度実績)。残りの65%についても、風力発電事業者から供給を受けています。
一方、建物の一部や高温の蒸気を必要とする一部の製造工程においては、蒸気生成の燃料として天然ガスを利用しています。この天然ガスの削減に向けて、同拠点では風力発電由来の電力で水を加熱し蒸気を発生させる電気ボイラーを導入しました。この電気ボイラーおよびより効率的な蒸気生成を可能にするヒートポンプの活用により、FUJIFILM Manufacturing Europeではグループ全体の目標年度から10年前倒しの2030年度にカーボンニュートラル*1を実現することを目指しています。
- *1 自社使用エネルギー起因のCO2排出ゼロ(Scope1,Scope2)
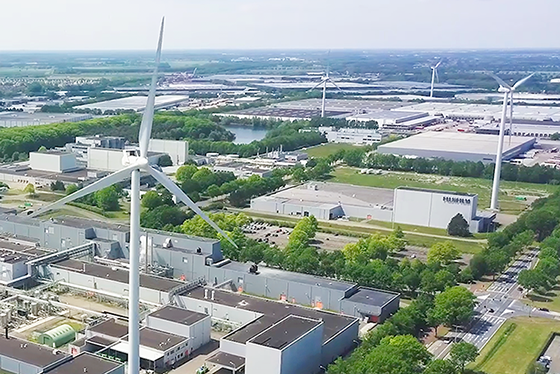
敷地内に複数の風力発電機を設置
内視鏡システムの生産における環境への配慮
(富士フイルムヘルスケアマニュファクチャリング 佐野事業所)
胃や大腸などの疾患の早期発見・治療への貢献が期待できる内視鏡システム。その製造を行う富士フイルムヘルスケアマニュファクチャリング 佐野事業所(栃木県佐野市)では、建屋の屋上や地上に太陽光発電パネルを設置することで、製造工程での使用電力を再生可能エネルギーに段階的に切り替え、CO2の排出削減を進めています。
内視鏡システムの組み立てを行う建屋では、太陽光発電の導入に加えて、その他の省エネ活動により、2023年度に全使用電力の実質的な再生可能エネルギー化*2を実現しました。
また、同事業所は、AIやIoT技術を活用し、生産効率を高めるスマートファクトリー化を推進中。従来は人による作業が必要だった工程を自動化することで作業時間を短縮し、使用電力の削減にもつなげています。同事業所では、将来的に事業所全体でのカーボンニュートラル*3実現も視野に、これからも取り組みを進めていきます。
- *2 再生可能エネルギー証書(再生可能エネルギーによって発電された電気の「環境価値」を証書化したもの)の適用を含む。
- *3 自社使用エネルギー起因のCO2排出ゼロ(Scope1,Scope2)
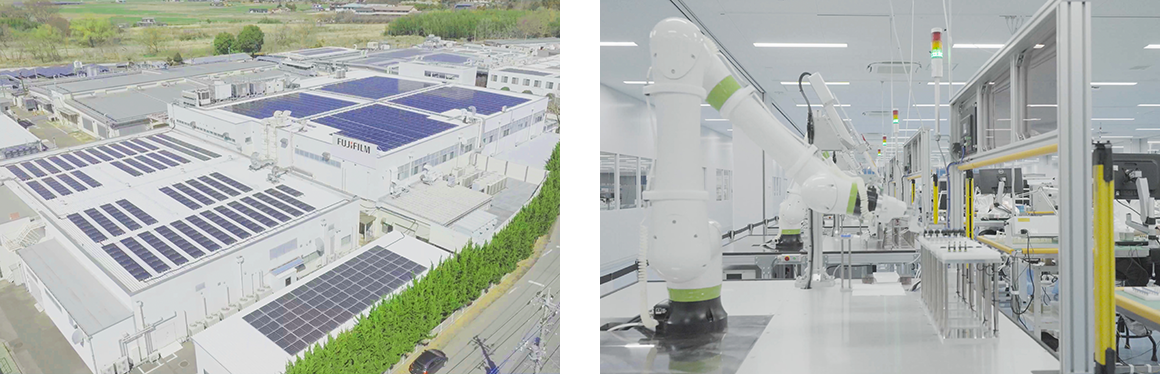
製品・技術における取り組み
環境負荷を低減する化成品の生産手法「フロー合成プロセス」
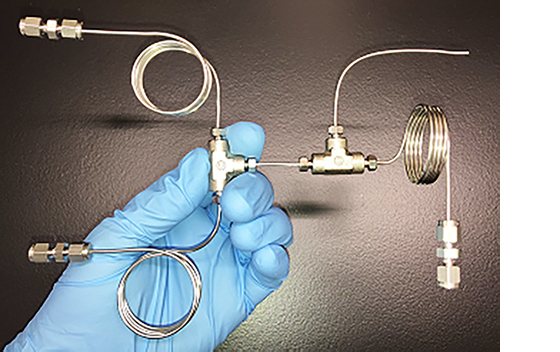
フロー合成法で用いられる極細な管
フロー合成法とは、直径数百ミクロン~数ミリメートル程度の極細な管に、原料である化学物質を連続的に供給して混合・反応させる化学合成法です。大きな反応釜で大量の原料を一度に混合・反応させる従来のバッチ合成法と比べて、フロー合成法はさまざまな生産規模に対応でき、多品種少量生産ニーズへの対応も可能です。
また一般的なバッチ合成法では、反応釜の一部での急激な反応を防ぐために、反応釜全体を極低温に冷却する大掛かりな設備が必要となる場合があります。一方フロー合成法では、バッチ合成法と比べて小さい反応部の冷却だけで済むことから、一般的な冷却設備が利用でき、大幅なエネルギー削減につながります。
当社はこのフロー合成法について、独自技術*4を活用し、生産性・エネルギー効率をさらに高めた新たな合成手法を開発しました。この新たな合成手法を使って、「アリールボロン酸誘導体」*5を生産した際に排出されるCO2について試算したところ、従来のバッチ合成法と比較すると、原材料の投入量と廃棄物量を抑制できること、また冷却に必要なエネルギーを低減できることから、同じ量を生産した際のCO2の排出量を約53%削減できることがわかりました。これらの環境性能を評価した結果、当社グループはこの合成手法を「Green Value Products」認定制度において、最上位ランク「ダイヤモンド」に認定しました。
- *4 化学工学的知見に基づいて設計された独自構造のミキサーや熱交換機の適用
- *5 医薬品の原料など幅広い化成品の生産において重要原料、中間体として使われる物質