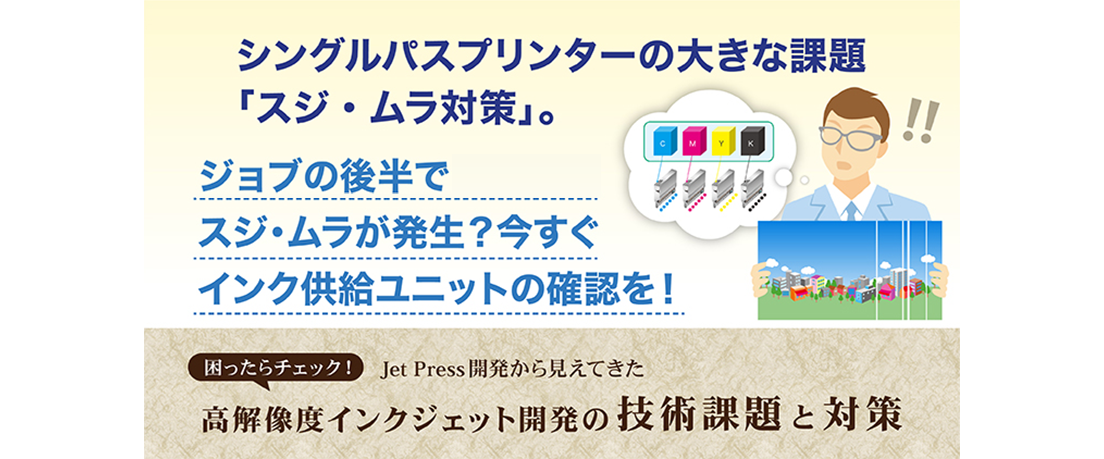
1200×1200dpiの解像度を持つシングルパス・インクジェットプリンター「Jet Press」の開発でさまざまなトラブルを経験した富士フイルムの技術者が、試行錯誤の中でわかった技術課題と対策についてご紹介します。
本記事の「3つのポイント」
- 見過ごされがちだが、インク供給ユニットがスジ・ムラの原因になりうる!
- インク供給を適切に行う際のポイントは、「異物」「気泡」「インク温度」「メニスカスの状態」
- インク供給ユニットを用いてプリントヘッドを安定的に使いこなすことが重要
本シリーズでは、これまで、「スジ・ムラの体系的な分析方法」をはじめ、スジ・ムラの原因として「プリントヘッドのクリーニング」、「搬送・振動」、「画像検査装置」を挙げ、それぞれの対策方法をご紹介してきました。
今回は、プリントヘッドにインクを供給する「インク供給ユニット」により起こるスジ・ムラとその対策方法をご紹介します。
「適切なインク供給」、できていますか?
1回の印刷(1ジョブ)で数百枚~数千枚印刷している最中に発生し始めるスジ・ムラや、装置を設置して数か月~数年経過してから発生し始めるスジ・ムラで悩まれた経験はありませんか?その場合、プリントヘッドが劣化してしまったからだと諦めていませんか?
そのスジ・ムラの原因は、プリントヘッドではなく、インク供給ユニットにあるかもしれません。実際に、Jet Pressの開発において、インク供給ユニットの改良でスジ・ムラを改善した経験があります。
インク供給ユニットに要求される主要な機能は、プリントヘッド内に安定してインクを供給し、プリントヘッド内のインクを適切な状態に保つことです。
特に、高解像度・高画質の画像を目指すほど、下記に挙げた4つのポイントが重要になります。
インク供給ユニットに要求される4つの機能
- 異物の除去と異物発生の抑制
- 気泡対策
- インク温度の制御
- ノズルにおけるメニスカスの制御
Jet Pressにおいても、上記4点に注意した設計を行ってきました。
では、次のページから、Jet Pressで発生したトラブルや、インク供給ユニットで注意すべき具体例について見てみましょう。
インク供給ユニット
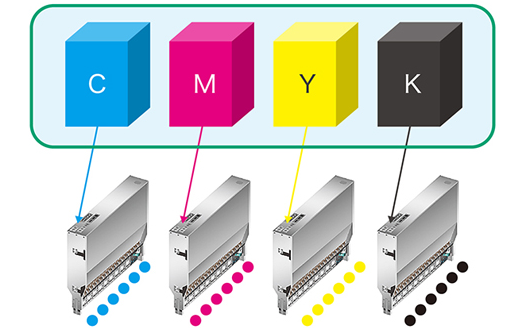
図1 プリントバー(プリントヘッド)にインクを供給する「インク供給ユニット」
では、適切なインク供給ユニットはどのようにすれば実現できるのか、具体例を紹介します。
インク供給ユニットの4機能でスジ・ムラを防ぐ
1.異物の除去と異物発生の抑制
1200dpiの高解像度プリントヘッドを用いた高画質な印刷においては、数μm程度の異物がインク中に混入しただけでも、画質に大きな影響を与えます。
しかも、異物は外部から混入したものだけでなく、インク中の固形分の沈降やインクの変質など、インク内部でも発生することがあり、これらがノズルや流路内に詰まることによりスジ・ムラの原因となります。
このような課題に対する一つの解答は、適切な粗さのフィルタの設置です。
インク供給ユニットでは、大きな異物を適切に除去しつつ、インク内で必要な固形分は通過させる必要があるので、インクやシステムに適したフィルタの選択が重要です。
フィルタの選択を間違えると、フィルタ自体がインク変質あるいはインク凝集物などの異物発生を引き起こしたり、フィルタの交換頻度を増加させる恐れもあります。
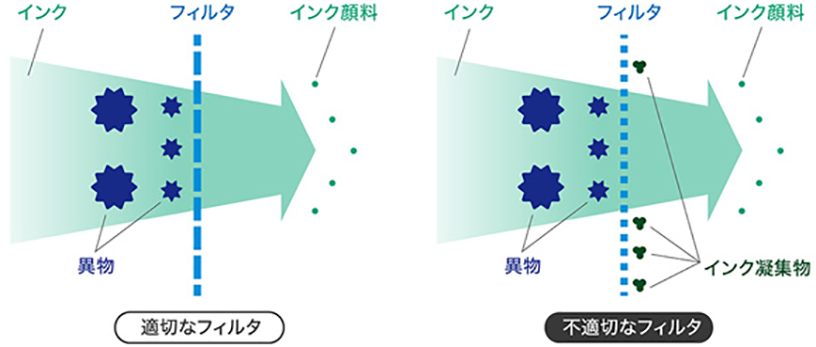
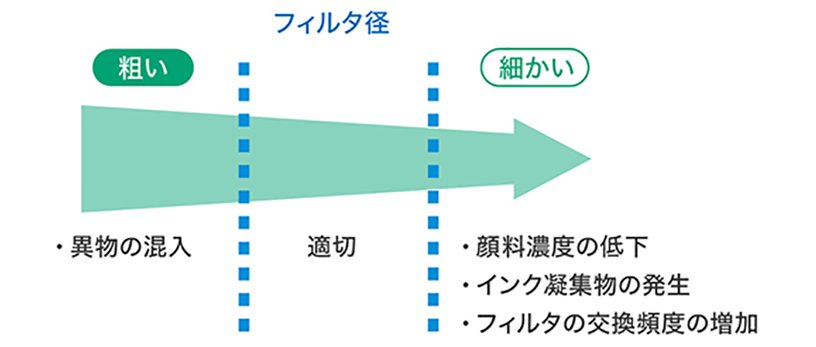
図2 フィルタによる異物除去と不適切なフィルタ使用時の問題
適切なフィルタ径を選択するには、用いているインクの顔料粒径、プリントヘッドの流路・ノズル径を考慮するだけではなく、そのフィルタを用いたときのインク供給ユニットの送液能力への考慮や、実際に長時間フィルタにインクを通し続けてもインクが変性しないかの評価が必要になります。
2.気泡対策
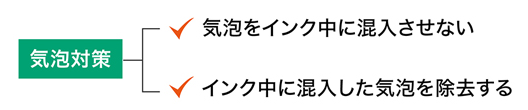
図3 気泡対策
インクジェットプリンターにおいて、気泡への対処は大変重要です。プリントヘッドの流路は数十μm程度と狭いため気泡が残存しやすく、気泡が流路につまると、スジ・ムラが多発してしまいます。インク供給ユニットには、インク中に気泡を極力混入させない設計、かつ、インク中に混入した気泡を除去する設計が求められます。
気泡をインク中に混入させない
インク中に気泡が混入する主な場所として、プリントヘッドのノズル面が挙げられます。
プリントヘッドのノズル面から気泡が混入するタイミングには、大きく、プリントヘッドのクリーニング時と印刷時の2つが考えられます。
プリントヘッドのクリーニング時の気泡対策については、「プリントヘッドのクリーニング直後のスジトラブルの原因に迫る!」で紹介しました。
印刷時の気泡混入対策の方法については、後述の「4」でご紹介します。
インク中に混入した気泡の除去
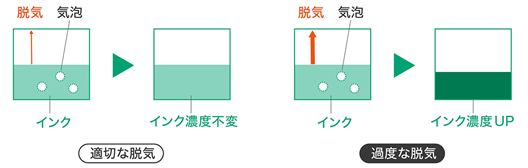
図4 適切な脱気が重要
インク中に気泡を極力混入させないようにしていても、エラーなどで気泡が混入してしまうことがあります。そのような場合、気泡除去のために、インクパージなどのシーケンスをインク供給ユニットに実装することが必要です。
また、目に見える気泡だけではなく、インク中に溶け込んでいる気体が、圧力や温度の変化などにより、インク中に気泡として発生してしまうこともあります。このようにインク中に溶け込んだ気体を取り除く方法として、インクの脱気があります。脱気フィルタを介して減圧することでインク中に混在した気体や溶け込んだ気体を効率的に除去できます。
ただし、過度に脱気をしてしまうと、インクの濃縮などのドローバックが発生するので、インクやシステムに応じた適切な範囲で脱気度を制御することが重要です。
3.インク温度の制御
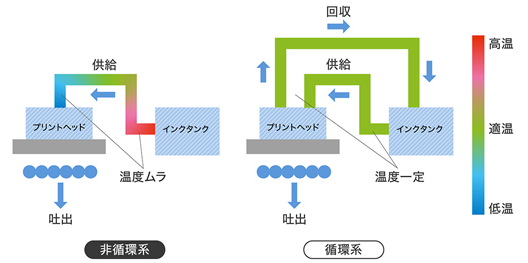
図5 循環機能があるとインク温度を一定に保てる
インクを適切に吐出するためにはインクの粘度も重要です。インクの粘度は温度により変動し、インク温度は外部環境の温度はもちろん、プリントヘッドなどインクジェットプリンター自体が持つ熱、あるいはヘッドに供給・吐出されるインクの量によっても変動し、吐出状態に影響します。特に印刷速度の速いプリンターでは、それぞれの変動幅が大きくなるのでインク温度制御はより困難になります。
このような課題に対する一つの解は、インク循環システムの導入です。インク供給のシステムには、大きく分けて循環不可能なものと、可能なものに分けられます。前者はプリントヘッドにインクを供給するのみで回収はできないのに対し、後者は供給したインクのうち、吐出しなかったものを回収でき、インク温度の制御もしやすくなります。
さらに、インク循環が可能なインク供給ユニットは、インクを常に置換、攪拌するため、ノズルにおけるインク乾燥の抑制、インク中の顔料等の分散成分の沈降抑制も可能になります。これにより、メニスカス表面のインク状態が安定し、吐出性も安定させることができます。
メニスカスの制御の重要性ついては、次節でも紹介します。
4.ノズルにおけるメニスカスの制御
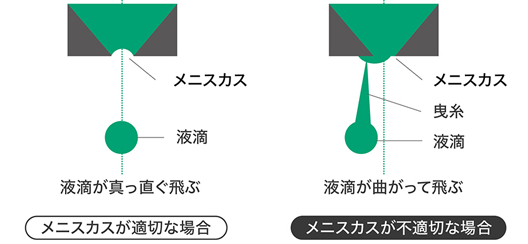
図6 メニスカスの形状が吐出に与える影響
インクジェットプリンターでは、ノズルにおけるインク面のメニスカスの形状を制御することで、高い精度での吐出を行っています。インク供給系が適正な背圧制御ができないと、メニスカスがノズル内に引き込まれすぎたり、出すぎたりして、適切なメニスカスの状態が保てません。
メニスカスを安定させるため、最新のインクジェットプリンターでは、背圧変動を計測し、インクの供給圧力と回収圧力をアクティブに制御する仕組みも採用されています。
例えば、図7のような縞状のベタ画像を印刷する場合を考えてみましょう。
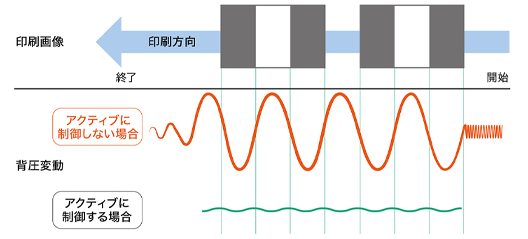
図7 印刷画像と背圧変動の例
ノズル面の圧力は、印刷開始時に背圧が下がり、印刷が終わると中心値に戻ろうとします。
アクティブに制御しない場合には、印刷中の圧力下降が大きいだけではなく、印刷後に背圧が中心値に戻ろうとする際にオーバーシュートが発生してしまい、メニスカスの状態が大きく乱れてしまいます。
メニスカスが大きく乱れると、図6で示したように、ノズルからインクがあふれて液滴が曲がってしまう恐れがあります。またメニスカスが凹みすぎた場合にはノズルから気泡を巻き込んでしまうこともあります。
また、こうした不具合に至らない場合でも、ノズルから吐出されるインク滴量が安定せず、印刷物上に濃度ムラが発生することもあります。
このように、メニスカスの状態が適切に保たれないと、スジ・ムラは容易に発生し、特に、印刷初期にはスジ・ムラがなかったのに、印刷中に発生し始める場合は、印刷中に気泡を巻き込んでいたり、ノズルからインクがあふれていたりする恐れがあります。
インク供給ユニットを用いてプリントヘッドを安定的に使いこなす
ここまで紹介した「異物」「気泡」「インク温度」「メニスカスの状態」は、印刷速度や印刷画像の絵柄・濃度などに依存します。例えば、高速での印刷時や、印刷する絵柄・濃度が複雑な場合、特にメニスカスの制御が困難になります。これは、吐出されるインク量と供給されるインク量の変動が大きくなりやすいためです。
富士フイルムは、シングルパス・インクジェットプリンター「Jet Press」の開発を通じ、プリントヘッドを安定して使用するためのインク供給ユニットの最適化に取り組んできました。そして、その技術ノウハウを基に開発したインクジェットコンポーネント「Samba JPC」では、適切なインク供給を実現する「液循環ユニット」、高精度の吐出性を誇るプリントヘッドをアセンブリした「プリントバーユニット」を提供しています。これらをご使用いただくことで、上記の「異物対策」「気泡対策」「温度制御」「メニスカス制御」を実現いただけます。
さらに富士フイルムは、Samba JPCをお使いいただくお客さまに、インク供給ユニットに関わるスジ・ムラの原因特定から対策まで、幅広い知見やデータ解析の技術の蓄積を生かしたコンサルティングも行っています。ぜひご活用ください。
今後もこのシリーズでは、具体的なトラブルを取り上げ、その原因と対策例についてご紹介していきます。また、開発でのお困りのことや疑問などがあれば、下記お問い合わせフォームよりぜひお問い合わせください。
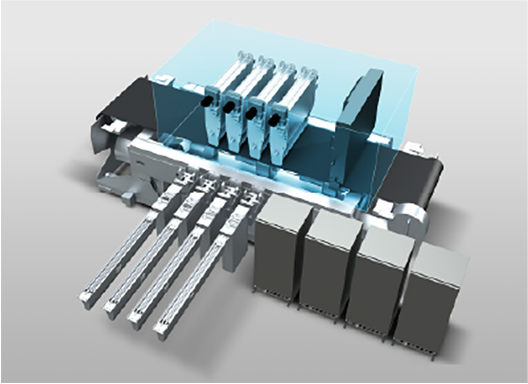
1200dpiの高解像度デジタル印刷機開発にスピード革新を起こすインクジェットコンポーネント「Samba JPC」
世界で評価される「Jet Press」の技術ノウハウを凝縮。1200dpiインクジェットプリンター開発に立ちはだかる膨大な課題を解決し、期間・コストを大幅に削減、出力安定性に優れたシステムの実現を強力にサポートします。