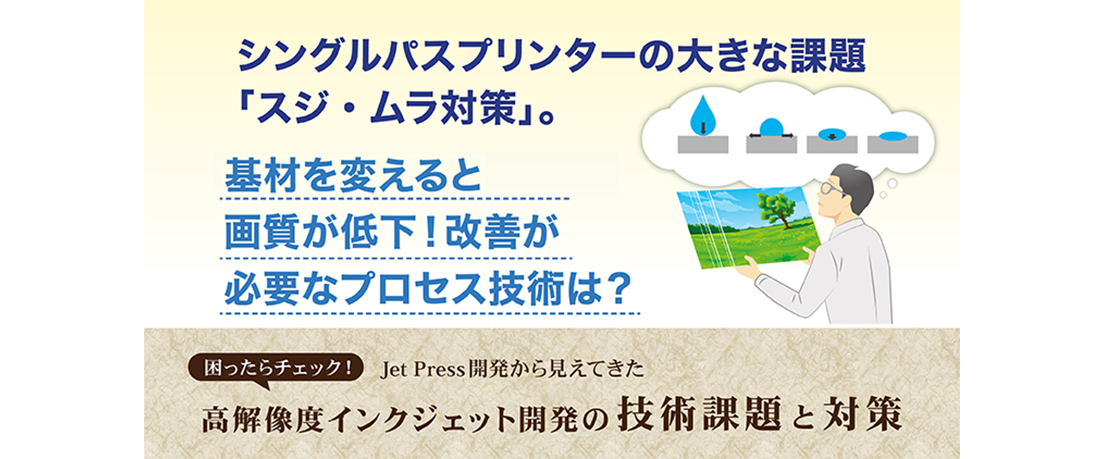
1200×1200dpiの解像度を持つシングルパス・インクジェットプリンター「Jet Press」の開発でさまざまなトラブルを経験した富士フイルムの技術者が、試行錯誤の中でわかった技術課題と対策についてご紹介します。
本記事の「3つのポイント」
- 基材を変えると思ったように印刷できない? 対策のポイントは基本的な画像形成プロセスの理解
- 画像形成プロセスは、(1)濡れ広がり、(2)浸透、(3)乾燥・定着の3つに分けて考える!
- さまざまな技術を投入することで、広範な分野にインクジェットを応用することが可能
インクジェットプリンターで印刷するときに、「この基材にはきれいに印刷できるのに、基材を変えると画質が安定しない」という経験はありませんか?
もちろん、基材の搬送方法がその原因となる場合もありますが、今回は、基材そのものが変わることにより印刷物の画質が変わる原因について解説します。
インクジェットの印刷対象となる基材の種類はさまざまに広がっている!
インクジェット技術の適用範囲は年々広まり、その印刷対象はインクジェット専用紙にとどまらず、汎用的な塗工紙・非塗工紙、さらには、テキスタイルやセラミックといった基材への印刷も一般に行われるようになってきました。
加えて、ガラスや金属などのインクが全く浸透しないような基材上に機能性インクを吐出し、アンテナやディスプレイの製造などを行う、いわゆるプリンテッドエレクトロニクス分野にも、インクジェット技術が適用され始めています(図1)。
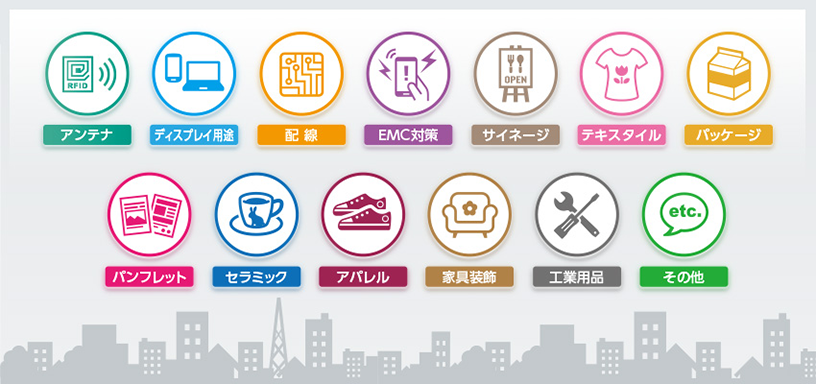
図1 インクジェット技術の応用展開例
富士フイルムでは、さまざまな基材に対するインクジェット印刷を実現させています。特にJet Pressの開発では、図1に示した応用展開例の中の「パッケージ」「パンフレット」など、主に紙基材に対しての印刷の知見を蓄えてきました。しかし、一口に紙基材といっても、後述するように、基材の物性により最終的な画質が異なるため、さまざまな紙基材に対応できる性能を確保するまでには、多くの苦労がありました。
また、富士フイルムでは、紙以外の基材に関するインクジェットの開発ノウハウも蓄積してきました。
では、さまざまな紙やその他素材にまで印刷対象を広げる場合、基材起因による画質トラブルにはどのような対策が必要になるのでしょうか。
インクジェットの画像形成プロセスを理解して、基材ごとの対策を!
基材が変われば、インクジェット印刷で必要になる技術は変わりますが、基本となる画像形成プロセスは変わりません。つまり、画像形成プロセスを理解することで、トラブルが発生しても適切な対策を打つことができます。
画像形成プロセスは、(1)濡れ広がり、(2)浸透、(3)乾燥・定着の3つに分類できます(図2)。それぞれのプロセスにおいて、基材が画質に及ぼす影響を見ていきましょう。
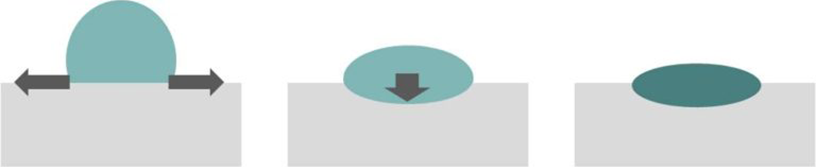
図2 画像形成プロセス(左:濡れ広がり、中央:浸透、右:乾燥・定着)
(1)「濡れ広がり」プロセス
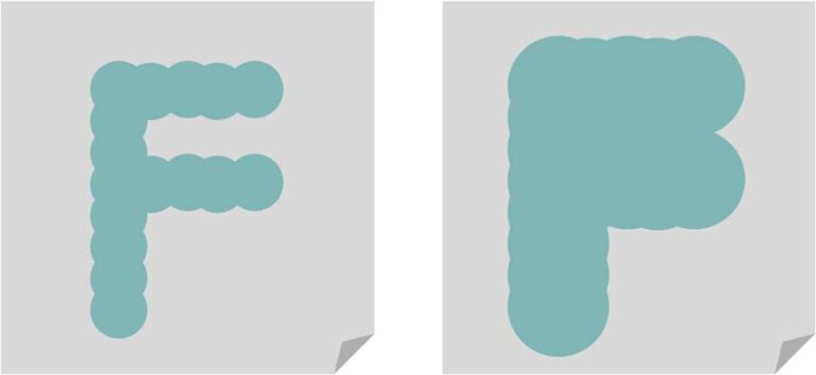
図3 広がり率の差による文字の可読性の違い
(左:広がり率が「低い」、右:広がり率が「高い」)
インクが基材に着弾した後、基材表面におけるインクの濡れ広がりやすさは、インク・基材の表面張力や、インク粘度、基材の表面粗さなどの物性に依存し、この物性値によって画質が変化します。
一般的に、インクの広がり率が大きいとき、解像性は低下する傾向にあります(広がり率については、「シングルパス・インクジェットプリンターにおける印刷速度の決定方法」をご覧ください)。例えば図3に示すように、同じドットの配置だとしても、広がり率の程度により文字の再現性が変化します。ドットが広がりすぎると、ディテールが失われてしまい、小さな文字が可読できなくなります。
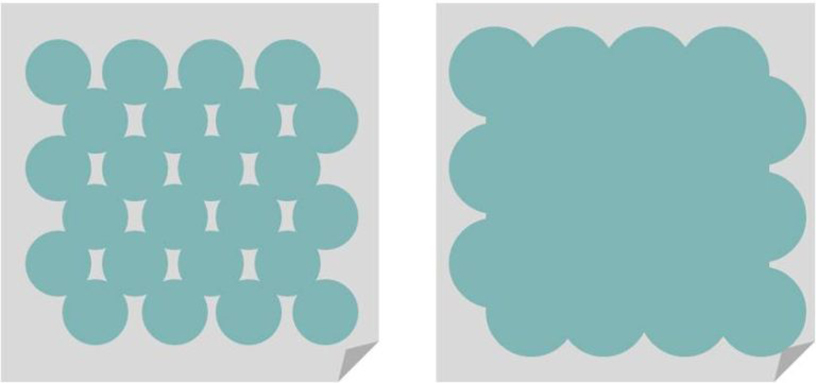
図4 広がり率の差によるベタ部の見え方の違い
(左:広がり率が「低い」、右:広がり率が「高い」)
それでは、広がり率が低い方が良いかというと、必ずしもそうではありません。
例えば、広がり率の低いインク・基材と、広がり率の高いインク・基材とで、同じドットパターンを印刷する場合を考えてみましょう(図4)。
図4のように狙った位置にインクが着弾した場合、マクロ(肉眼で)に見ると、どちらもきれいにベタが埋まっているように見えます。
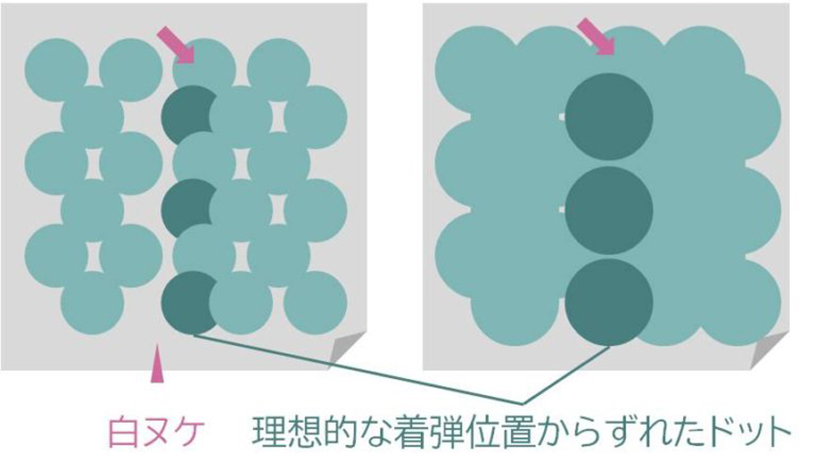
図5 着弾位置のずれが起きた場合の広がり率の差と白ヌケの発生しやすさ
(左:広がり率が「低い」、右:広がり率が「高い」)
では、プリントヘッドの劣化などにより、ドットが理想的な着弾位置からずれてしまう場合を考えてみましょう(図5の濃い色のドット)。
このとき、広がり率が高い場合では白ヌケは見られませんが、広がり率が低い場合はライン状の白ヌケが見られ、マクロで見たときに、印刷物上の白スジという画像欠陥として見えてしまいます。
このように、印刷物の白スジの発生を防止するためには、高い広がり率を持つことが望ましい一方、高精細性を実現するためには、広がり率が低いことが望ましいといえます。
それでは、広がり率を制御するにはどうすればよいでしょうか?
前述したように、広がり率はインクと基材の物性に依存し、これらを制御することが重要です。
基材の物性を制御する方法としては、基材に下塗り剤を塗る方法が挙げられます。下塗り剤の種類によって、広がり率を大きくすることも小さくすることも可能です。
その他の方法としては、基材に放電照射を行う「コロナ処理」が挙げられます。コロナ処理により、濡れ性が向上し、インクを広がりやすくさせることが可能です。
(2)浸透プロセス
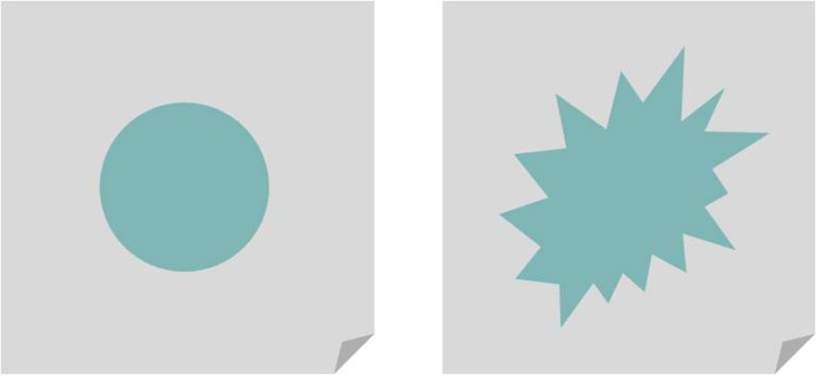
図6 フェザリングの有無
(左:なし、右:あり)
紙などの基材では表面に微細な穴が多数存在し、その穴を通してインクが基材内部に浸透していきます。
この浸透性が画質に与える影響として、「にじみ」が挙げられ、その中には「フェザリング」や「ブリーディング」があります。
フェザリングとは、非コート紙などの基材において、インクが基材内部に浸透するよりも紙表面の繊維に沿って移動し、図6の右側のように輪郭が毛羽立ってしまうことです。結果、文字の可読性を低下させてしまうため望ましくありません。
フェザリングを抑制するには、上述した下塗り剤を塗ることで表面を平滑化する方法が考えられます。
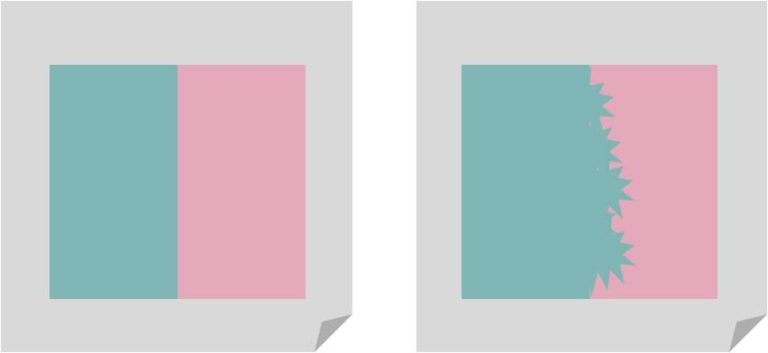
図7 ブリーディングの有無
(左:なし、右:あり)
次にブリーディングとは、図7右のように異なる色のインクが境界でにじむ現象です。インクが基材中に浸透する前に、他色のインクが基材上に着弾し、互いに混ざりあうことによって発生します。ブリーディングを抑制するには、異なる色のインク間の印字タイミングをずらして時間を空ける方法や、下塗り剤を使ってインクの凝集を起こす方法、打滴直後に温風やUV光(UV硬化インクの場合)を当てることによりインク粘度を急速に高める方法が挙げられます。
また、インクジェットインクは溶剤をはじめとする種々の成分を含みますが、最終印刷物ではそのうちの色材のみを見ることになるので、基材中での色材の移動が重要です。
ここで、コート紙と非コート紙に、染料インクもしくは顔料インクで印刷する場合を考えてみましょう。
このコート紙の塗工層表面に存在する穴は細かいため、色材が溶媒中に分子レベルで溶解している染料インクでは色材が基材中に浸透しますが、色材が固形物で分散されている顔料インクでは大部分の色材は基材表面に残存します。
一方で、非コート紙では顔料インクでも基材内部に色材が浸透します。
また微細な穴がなく浸透がそもそも起こらないプラスチックや金属などは、色材はすべて基材表面に残存します。
この色材の存在位置の違いは、画質にどのような影響を与えるのでしょうか。
色材が基材表面に偏在するほど、基材中での光の拡散・反射が抑制されるため、濃度が高くなり、逆に色材が基材中に浸透すると、濃度は低くなり、ひどい場合には紙の裏面にまで染み出します(裏移り)。色材が浸透しやすい非コート紙において濃度低下を抑制したい場合にも、浸透を抑制する下塗り材を塗布するという対策が考えられます。
(3)乾燥・定着プロセス
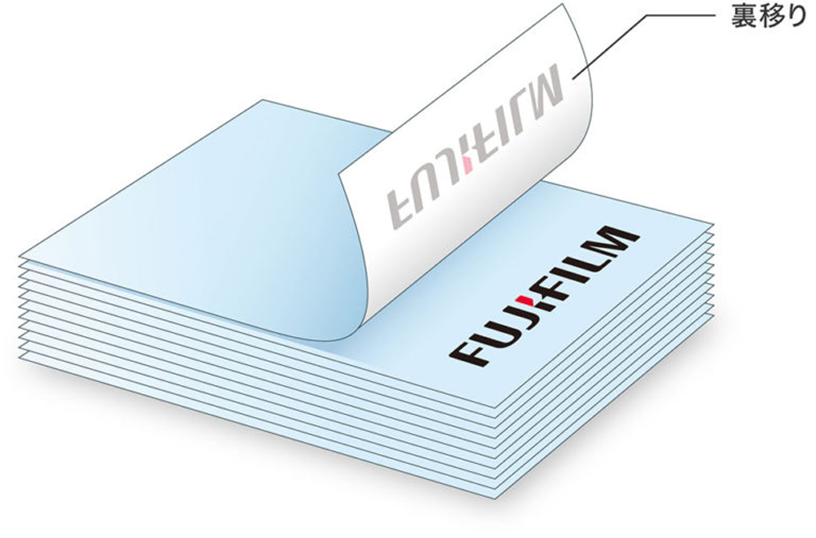
図8 インクの裏写り
基材上でインクが液状のまま残ると、インクが裏写りしたり(図8)、基材の強度を弱めたりするため、インクを乾燥する必要があります。
しかし、本プロセスも大きく印刷基材に依存します。
例えば、インクを加熱乾燥する場合、基材の厚みは厚いほど、基材の浸透性は低いほど、より多くの熱が必要になります。このように基材が変わると、それに応じて乾燥プロセスを調整する必要があります。
また、熱に対する耐性がない基材では、短時間で多くの熱を加えることが難しくなります。例えば、熱により変形するプラスチック基材の場合、乾燥に長時間を要してでも穏やかに熱を加えるか、あるいは熱ではなく風で乾燥させる必要があります。
乾燥時間を短縮あるいは装置を簡易化にする方法としては、インク中の溶媒としてより沸点の低いものを用いたり、UVインクを使用するという対策が挙げられます。
しかし、このようなシステムを実現するのは容易ではない
以上、ほんの一例ですが、さまざまな基材に対するインクジェット印刷による画像形成の課題と対策を示しました。インクジェットの画像形成プロセスは一見シンプルであるものの、基材が変われば適用する技術が広範にわたって変化することがご理解いただけたと思います。逆にいえば、さまざまな技術を投入することで、広範な分野にインクジェット技術を応用することが可能です。
とはいえ、広範な技術分野すべてをカバーするのは時間がかかり、容易ではありません。富士フイルムでは、さまざまな基材に対するインクジェット技術のノウハウを数多く蓄積しており、こうした印刷に必要なインクも各種コンポーネントも取りそろえています。特殊な基材へのインクジェット印刷に関する開発でお困りのことや疑問などがあれば、どのようなことでも構いませんので、下記フォームよりお気軽にお問い合わせください。
参考文献
日本画像学会・藤井 雅彦,インクジェット, シリーズ「デジタルプリンタ技術」,東京電機大学出版局, 2008
Werner Zapka, Handbook of industrial inkjet printing: A full system approach, Wiley‐VCH Verlag GmbH & Co. KGaA, 2018
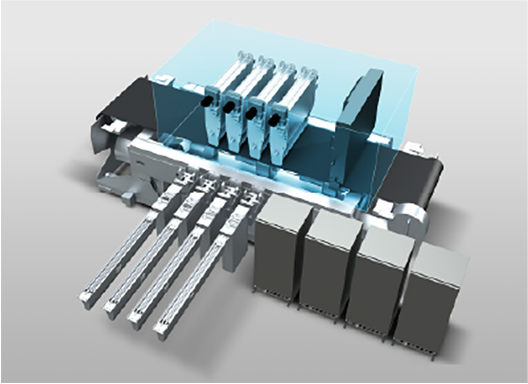
1200dpiの高解像度デジタル印刷機開発にスピード革新を起こすインクジェットコンポーネント「Samba JPC」
世界で評価される「Jet Press」の技術ノウハウを凝縮。1200dpiインクジェットプリンター開発に立ちはだかる膨大な課題を解決し、期間・コストを大幅に削減、出力安定性に優れたシステムの実現を強力にサポートします。