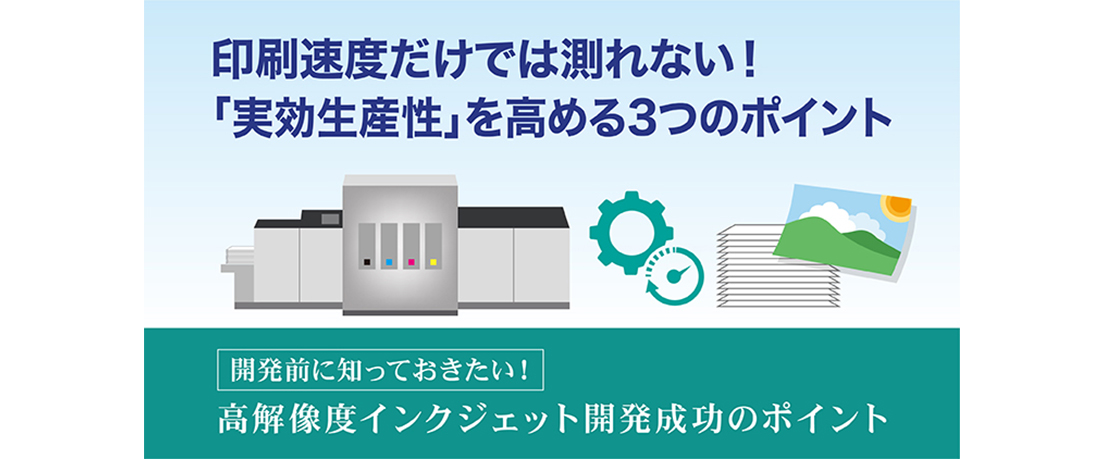
富士フイルムが1200×1200dpiのシングルパス・インクジェットプリンター「Jet Press」の商品化を通じて培った、高解像度インクジェットプリンター開発の「虎の巻」を特別に公開します。
本記事の「3つのポイント」
- 瞬間的な印刷速度だけでプリンターの生産性は測れない。「実効生産性」が重要
- 適切なメンテナンスによるヘッド吐出状態の維持で、印刷前準備時間を短縮
- 不良ノズルの検出と画像補正により、余計な印刷調整時間・検査時間を削減
「シングルパス・インクジェットプリンターにおける印刷速度の決定方法」でご紹介したように、プリンター購入時の比較検討で重視される指標の一つが印刷速度です。しかし、ユーザーにとって本当に生産能力が高いプリンターを実現するためには、プリンターの瞬発力である印刷速度だけではなく、さまざまな要因が影響する「実効生産性」をきちんと測り、高める必要があります。
印刷速度が速いのに生産性が低い?!本刷り以外の時間短縮が生産性向上には必須
印刷速度の向上以外において実効生産性を高めるためのポイントは3つあります。
- 印刷前準備時間の短縮
- 印刷調整時間の短縮
- 検査(再印刷を含む)時間の短縮
製品の印刷(本刷り)以外のこうした時間をおろそかにしてプリンターを開発すると、印刷速度は優れているにも関わらず、1日あたりの印刷量が少ない、つまり、実効生産性が低いプリンターになる恐れがあります。
実際に生産性が印刷速度だけでは測れない例について考えてみましょう。
例えば、A社製のプリンター(以下、プリンター A)とB社製のプリンター(以下、プリンター B)があり、Aの印刷速度は Bの印刷速度の2倍だとします。
しかし、製品の印刷以外の時間、例えば、印刷前準備時間、印刷調整時間がすべて、AはBの2倍の時間がかかるとします。
このとき、AとBで同じ量の印刷をした場合の所要時間例を示します。

図1 印刷所要時間の例
このように、Aの方が印刷速度は速いにも関わらず、製品の印刷以外の時間がBより長くかかるため、結果としてAの所要時間はBよりも長く、つまり、実効生産性は低くなることが分かります。
では、製品の印刷以外の時間に行う作業には具体的にどのようなものがあるのでしょうか?
一般的なインクジェットプリンターでは以下のものが挙げられます。
表1 インクジェット印刷機における製品以外の時間に行う作業時間の具体例
工程 | 詳細 | 内容 |
---|---|---|
印刷前準備 | ウォームアップ | インク温度調整、乾燥温度調整など |
装置メンテナンス | プリントヘッドのクリーニングなど | |
印刷調整 | 補正 | スジ補正、濃度補正など |
試し刷り | 色味や原稿の仕上がりを確認するための印刷 | |
検査 | 検品 | 印刷物にスジがないかの検査など |
再印刷 | 不良品となる部分の再印刷 |
これらの作業のほとんどはプリンターの運用に必要不可欠なもので、最小限に抑えて実効生産性を高めるかが重要です。
では、実効生産性を高めるにはどうしたらよいのでしょうか?
プリントヘッドのメンテナンスと画像補正が重要!!
表1で紹介した各工程において、プリンターの実効生産性を高めるためのポイントを1つずつご紹介します。
ポイント1:【印刷前準備】プリントヘッドの吐出性の維持
印刷前準備で重要な作業として装置のメンテナンスが挙げられます。
インクジェットプリンターの場合には、特にプリントヘッドの吐出性を維持することが重要です。
プリントヘッドの吐出が安定しないと、インクの吐出方向が曲がって画像にスジが発生したり、ノズルから吐出されるインクの滴量が変わって濃度ムラが発生したりします。そのため、繰り返しのプリントヘッドのクリーニングが必要となり、補正を行うための印刷にすら、なかなか入れないという事象が発生します。
吐出状態を維持するためには、高性能なプリントヘッドの使用だけでは不十分です。例えば、インクの安定的な供給、適切なプリントヘッドのクリーニングの実施、非印刷時のプリントヘッドの適切な保管などが必要です。
ただし、安定的なインク供給や適切なクリーニングの実施は非常に難しく、例えばインク供給ユニットが原因でスジ・ムラが発生したり、誤ったクリーニングで逆に吐出状況が悪化することもあります。
また、そもそも吐出状態を定量的に把握すること自体が困難であり、吐出状態を維持できているかの把握は難しい課題です。
吐出状態の管理や、クリーニング、インク供給ユニットについては、本サイトでもご紹介していますのでぜひご覧ください。
ポイント2:【印刷調整】印刷前の不良ノズルの検出&画像補正
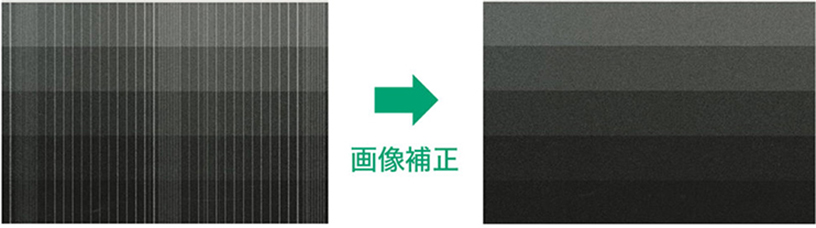
図2 画像補正の例
(左)意図的に多数のノズルの吐出をOFFにし、スジを再現(右)画像補正を行うことで、スジ欠陥が見えなくなる
デジタル印刷機の場合でも、印刷方式によっては、色が安定するまで時間がかかる、再印刷時に過去の印刷物と色が合わない、などの理由で印刷調整に時間を要する場合があります。
インクジェットプリンターの場合、ポイント1で紹介したとおり、プリントヘッドからのインクの吐出状態(吐出方向の曲がり、吐出滴量)を一定に保つことが最重要です。
とはいえ、大型のインクジェットプリンターの場合、プリントヘッドの総ノズル数が数十万以上になることもあり、それら全てを常に良好な状態に保つのは容易ではありません。
そこで頼りになるのが、画像補正技術です。
「画像欠陥を撲滅する鍵は画像処理技術にあり!」でご紹介したように、吐出状態が悪化した不良ノズルがあったとしても、画像補正技術により、良好な画質を保つことができます。
また、プリントヘッド間で濃度ムラが存在する場合にも同様に、画像補正によりムラを視認できなくさせることが可能です。
これらの補正技術により、印刷調整時間を大幅に削減することができます。
ポイント3:【検査】印刷中の不良ノズルの検出&画像補正
印刷調整中の補正や試し刷りのときにはスジが出なくても、製品の印刷中に不良ノズルが発生することがありえます。
もし、そのまま製品の印刷を続けてしまうと、その印刷物や印刷時間が無駄になるばかりか、過去に作成した印刷物の検品、再印刷まで必要になることもあります。
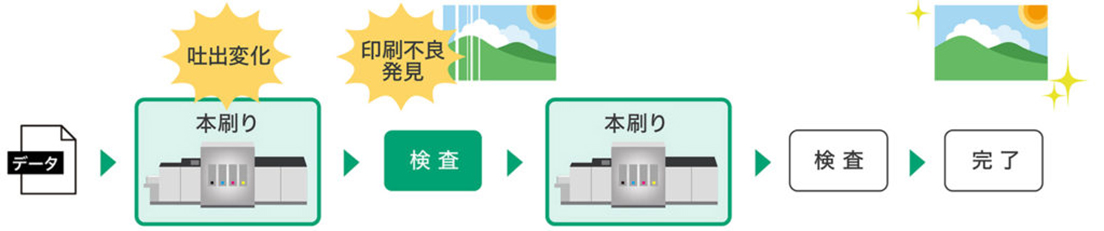
図3 印刷中に画像補正を行わない場合
不良ノズルを印刷中に検出し、補正ができれば、再印刷を防ぐことができ、結果として実効生産性が高まります。
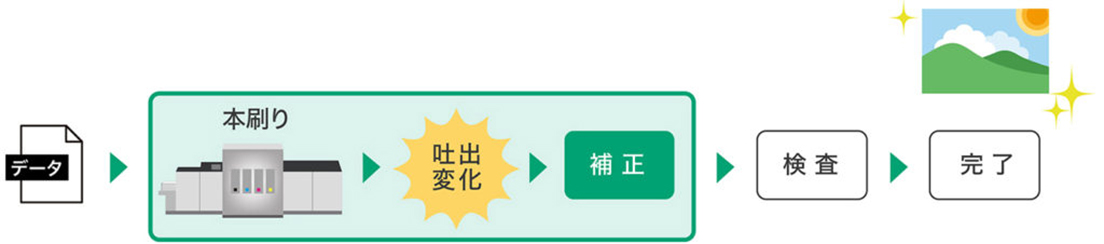
図4 印刷中に画像補正を行う場合
吐出性の維持・不良ノズルの検出・画像補正にはノウハウが必須
今回はインクジェットプリンターの実効生産性を高めるポイントとして、1.印刷前準備時間の短縮 、2.印刷調整時間の短縮、3.検査時間の短縮の3つを紹介しました。
そしてこれらの実現には、プリントヘッドのクリーニングと、不良ノズルの検出・画像補正が重要であることをご紹介しました。
しかし、これらの実現にはシステム全体での最適化が必要であり、多くのノウハウが必須となります。
例えば、プリントヘッドのクリーニングだけでも、インク循環の圧力制御や払拭方法なども考慮する必要があり、すべての最適化には非常に膨大な開発期間が必要になります。
また、不良ノズルの検出・画像補正の難しさについても、「スジ・ムラを体系的に分析するには?」でご紹介しているとおり、不具合箇所や原因の特定、対応方法決定まで多くの困難が存在します。それらを一つひとつ解決することにより、実効生産性の高いインクジェットプリンターが実現可能となります。
富士フイルムでは、Jet Pressの開発でこうした課題を解決する手段を開発し、高い生産性を実現するまでに、数年を費やしました。
この経験で得た知見・技術を整理し、高解像度シングルパス・インクジェットプリンター開発に取り組む方にご利用いただける、インクジェットコンポーネント製品「Samba JPC」を提供しています。「Samba JPC」を通じて私たちの知見・技術を活用いただき、御社の開発を効率化することで、プリンティングのデジタル化を一緒にリードし、インクジェット市場の拡大と発展に寄与したいと考えています。ぜひご利用ください。
また、今回は紙面の都合上、画像補正に関するポイントを重点的にご紹介しましたが、他にも実効生産性を高めるポイントは複数あります。次回以降にご紹介しますので、ぜひご期待ください。
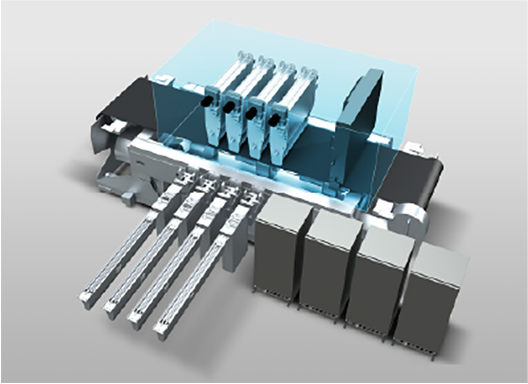
1200dpiの高解像度デジタル印刷機開発にスピード革新を起こすインクジェットコンポーネント「Samba JPC」
世界で評価される「Jet Press」の技術ノウハウを凝縮。1200dpiインクジェットプリンター開発に立ちはだかる膨大な課題を解決し、期間・コストを大幅に削減、出力安定性に優れたシステムの実現を強力にサポートします。