商品における資源循環の取り組み
取り組みの全体像
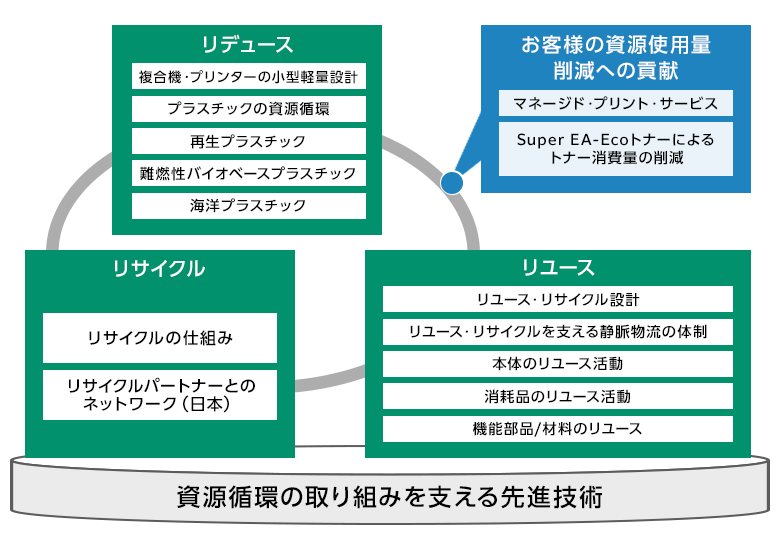
資源循環の取り組み
富士フイルムビジネスイノベーション リサイクル方針
「限りなく『廃棄ゼロ』を目指し、資源の再活用を推進する」
クローズド・ループ・システム
「使用済み商品は、廃棄物ではなく、貴重な資源である」という考え方に基づき、1995年に構築した商品企画/開発/製造段階から廃棄に至る商品のライフサイクル全体を視野にいれた循環型システムです。
限りなく「廃棄ゼロ」を目指し、回収した使用済み商品から取り出した部品を再生技術によりリユース活用し、資源として循環させています。
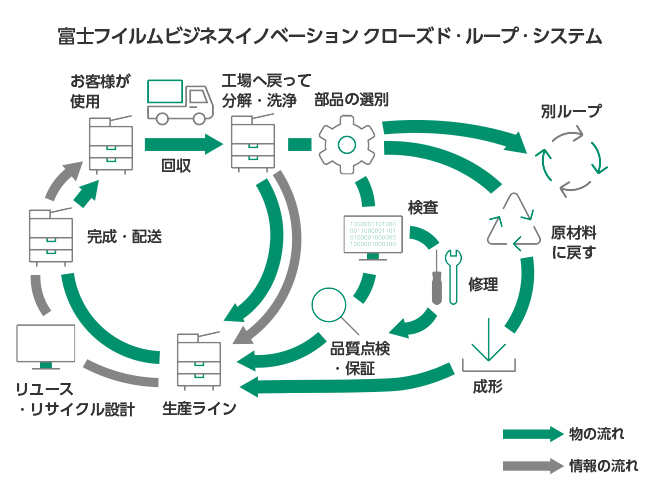
取り組みの歴史
当社は、1995年に富士フイルムビジネスイノベーション リサイクル方針を定め、お客様使用済み商品の回収、リユース・リサイクルを行い、1996年、業界で初めてリユース部品を使用した商品を市場に投入しました。
2000年には、日本の業界で初めての廃棄ゼロ(再資源化率99.9%以上)を達成しました。
2008年、中国の蘇州にリユース・リサイクル拠点を設立し、海外へも活動を拡げています。
また、リユース部品の活用拡大を推進し、2010年には製品としての再生した機械を商品化しました。
2024年5月には、富士フイルムグループのCSR計画「Sustainable Value Plan(サステナブル・バリュー・プラン)2030(SVP2030)」で、資源循環に関する新たな目標を掲げました。
さらに、マネージド・プリント・サービス(MPS)の提供により、お客様の出力環境における資源使用量削減に貢献しています。
新規資源投入率注1の目標と実績
2030年度までに新規資源投入率60%以下を目標としサーキュラーエコノミーへの移行に貢献します。
使用済み複合機、トナーカートリッジやスペアパーツ等のリユース拡大に加え、再生プラスチックや再生鉄等、再生材の活用を拡大することで、新規資源の投入を抑制します。
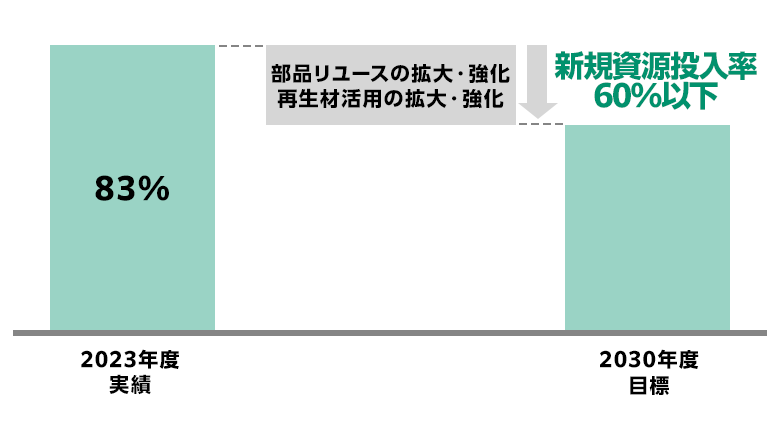
- 注1新規資源投入率:トナー方式の複合機/プリンタ/プロダクション機、包材、トナーカートリッジ、オプションの総重量における新規資源投入量
新規資源:化石燃料、金・銀・銅・鉄などの地下資源(枯渇資源)を含み、再生鉄、再生プラなどの再生材、木、紙等の非枯渇資源を含まない
リデュースの取り組み
2. プラスチックの資源循環
再生プラスチック
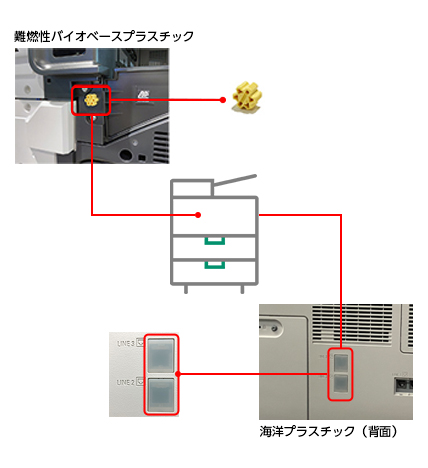
難燃性バイオベースプラスチック
海洋プラスチック
海洋生物や生態系への深刻な影響を及ぼしている海洋ごみ問題の解決に向け、海洋プラスチックごみの回収促進に貢献すべく、複合機の本体部品に海洋プラスチックごみを原材料にしたプラスチックの活用に挑戦しました。
2024年2月、業界初注1の試みとなる再生機本体に、海洋プラスチックと再生プラスチックを原材料としたプラスチックカバー部品の投入を開始しました。
- 注1自社調べ
リユースの取り組み
1. リユース・リサイクル設計
当社では、回収された使用済み商品から取り出した部品を効果的にリユースするために、リユース・リサイクルを前提とした指針のもと複合機などの製品を設計しています。
設計指針
長寿命設計:再使用できるように部品を長寿命化する
分離設計:短寿命部品のみを分離して、再使用可能な部品は再使用する
強度設計:使用・回収・再生作業時における部品の損傷を最小にする
分解設計:解体・材料分別のために分解しやすい設計にする
再使用可能な材料の使用:材料リサイクルができるように再材料化が可能な材料を選択する
設計の共通化:他機種/後継機で再使用できるように共通化する
「使用済み製品は廃棄物ではなく、貴重な資源である」という考え方に基づき、1995年からリユース・リサイクルの設計指針や調達方針を策定し、ガイドラインとして展開しています。
社内のみならず、サプライチェーンの上流にも展開し、ノウハウの共有化、リユース・リサイクル技術の共同開発など部品・素材メーカーとの連携を強めています。
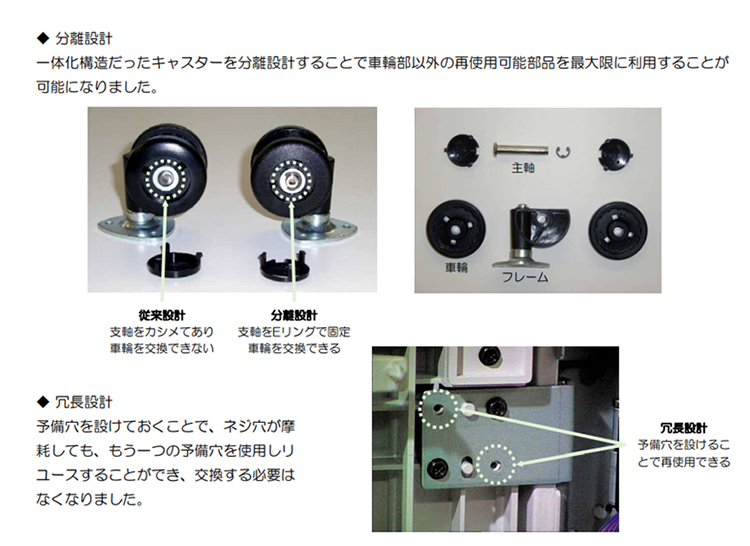
リユース/リサイクル設計の具体的事例
2. リユース・リサイクルを支える静脈物流の体制
当社では、発生した使用済み商品は、基幹システムに登録される解約/回収オーダーを受け、「回収判定システム」によりリユース対象・リサイクル対象機に自動区分されます。
発行された回収指示により、リユース対象機は再生機の生産拠点へ、リサイクル対象機は再資源化協力会社により回収され、リユース・リサイクル工程に進みます。
3. 本体のリユース活動
4. 消耗品のリユース活動
リサイクルの取り組み
2. リサイクルパートナーとのネットワーク(日本)
お客様使用済みの機器は、全国のリサイクルパートナーでリサイクルしています。
各地域のリサイクルパートナーとの協業により、最新のリサイクル技術を活用するだけではなく、運搬距離を減らすことで、CO2排出量の削減にもつながっています。
お客様の資源使用量削減への貢献
1. マネージド・プリント・サービス
資源循環の取り組みを支える環境技術
1. 使用履歴情報を活用する技術
当社は、複合機に記録されている約200種の使用履歴情報から、約30種の使用履歴情報と、部品寿命データベースを使用履歴情報システムで照合し、部品単位で余寿命を診断し再利用の可否を自動で判断することで、部品のリユース率を拡大しています。
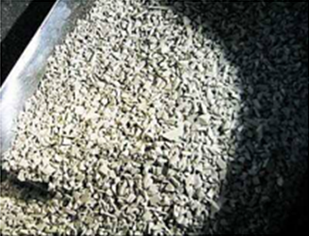
2. 再生プラスチック技術
当社は、1998年、回収した自社商品を原材料に、リサイクルした再生プラスチックの活用を開始しました。
使用済み商品の外装カバーや用紙トレイのABS樹脂製の部品を分別・破砕・洗浄し、これらを原料として新造ABS樹脂と同等のリサイクルプラスチックとして自社商品に導入しています。
この再生プラスチックは、新造ABS樹脂と同等の品質を保証し、米国の安全試験機関であるUL(Underwriter's Laboratories)認証を取得しています。
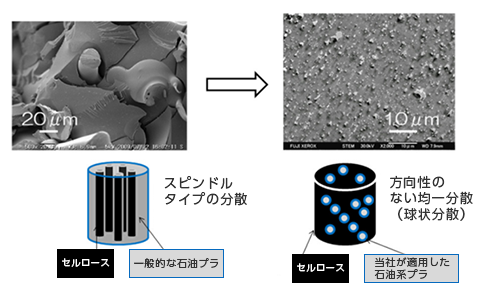
3. 難燃性バイオベースプラスチック技術
石油由来のプラスチック利用の削減に向けて、植物由来のバイオベースプラスチックの研究開発を進めています。従来の木質系バイオベースプラスチックは、高い難燃性と寸法の安定性を実現させることは困難でした。
セルロースとの親和性が高い難燃剤を徹底的にスクリーニングし、セルロース/ABSアロイ技術により、均一で等方的な分散させることでこの課題を解決し、商品の内装材として使用しています。
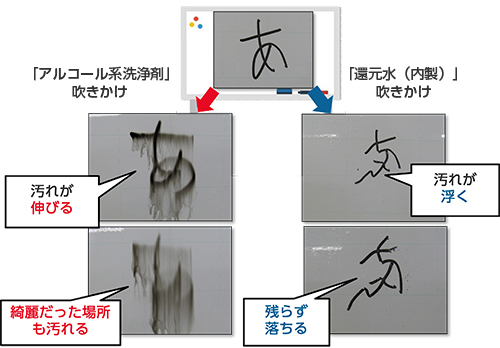
4. 洗浄技術
回収した使用済み商品から取り出した部品をリユースする際に、自社工場で内製した油脂系汚れに対する洗浄力が高い還元水を用いて部品を洗浄しています。
5. ブラスト処理を活用した加工技術
経年変化による黄変によりリユースできなかった外装プラスチックを、ブラスト洗浄技術の導入により黄ばみを除去することに成功し、リユース可能な部品として再生することができました。
ブラスト加工技術は、一般的に樹脂の表面を削るバリ取りやすりガラスの製造に使用されていますが、外装カバーを傷つけないが黄変を除去できる強度を持った適切な研磨剤を見つけることが非常に困難でした。
その適切な研磨剤の発見により、ブラスト加工技術での外装カバーの黄ばみ除去への活用に成功し、外装カバーのリユース率の拡大に貢献。
2023年6月から生産工程に導入することで、外装カバー部品のリユース率は、技術導入前の50%程度から80%程度まで向上することができました。
6. 包材設計シミュレーション技術
当社はシミュレーション技術を活用し、試作機の完成前から物流試験に必要な包装品質をつくりこむなど、包装設計技術の開発を進めてきました。
最近は包装使用量の削減に取り組み、資源循環の促進にも貢献しています。
自社活動における資源循環の取り組み
1. スマート工場での不良品削減による廃棄物削減
生産工程で商品毎に収集するデータは、通常は市場での不良発生後や出荷時に確認されます。富士フイルムビジネスイノベーションでは、事前にねらい値や技能など良品を作る条件をデータとして設定し、同条件以外でラインを動かなくすることで、不良品の発生を減らし、廃棄物の発生を抑える取り組みを進めています。
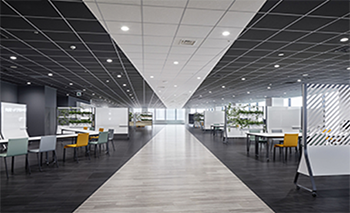
2. オフィスでの廃棄物削減活動
当社は、事業活動で使用する資源の有効活用を進めるため、生産事業所と同様にオフィス(非生産事業所)でも適切な廃棄物の管理を行っています。国内オフィス系事業所では、マニフェスト(産業廃棄物管理票)を電子化し、産業廃棄物の遵法管理レベルの向上を進めています。海外オフィス系事業所では、各国の法令やインフラに応じた廃棄物の管理が行われていることを確認しており、今後もコンプライアンス遵守を前提とした管理を継続していきます。
3. 海老名事業場食堂での生ごみ堆肥化
海老名事業場では、年間約20tの生ゴミが発生していました。2022年8月より全量を堆肥リサイクル活用に転換しました。