本製品・ソリューションは、富士フイルムグループ向けのみの対応になっております。
生産情報システム部は、ICTを活用しFFグループの生産現場の効率化を推進します。FFグループ内のシステム部門として、課題形成からシステム製作・保守までを一貫して担っています。特に付加価値の高い課題形成に重点を置いており、外部のソフトウェアメーカーでは難しい生産現場の調査・課題発掘・施策立案し、客観的な視点で提案します。

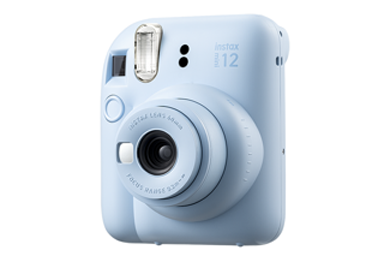
インスタントカメラ
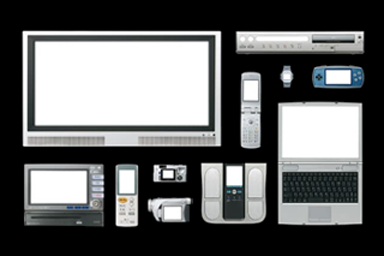
液晶画面
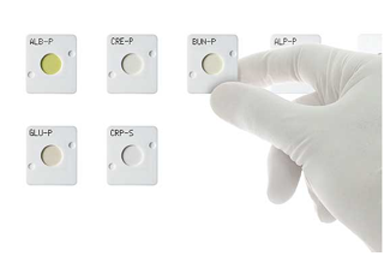
体外診断用医薬品
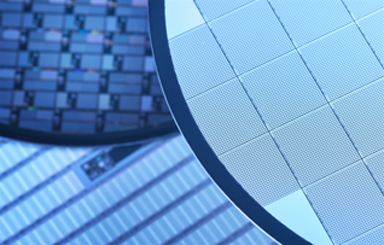
半導体
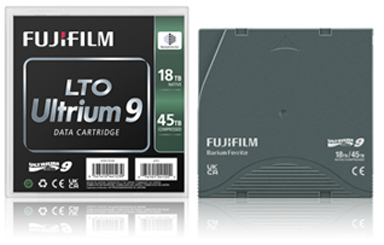
磁気テープ

内視鏡
生産現場の調査分析・課題発掘・提案に重点を置き、客観的視点からさまざまな事業分野の課題解決を目指します。
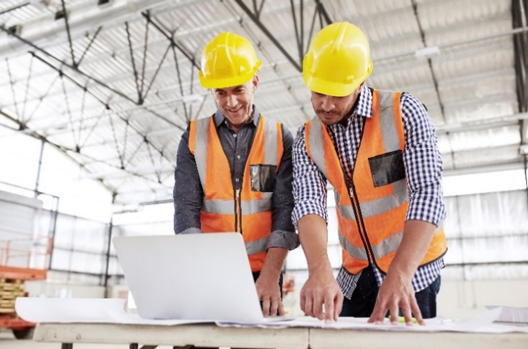
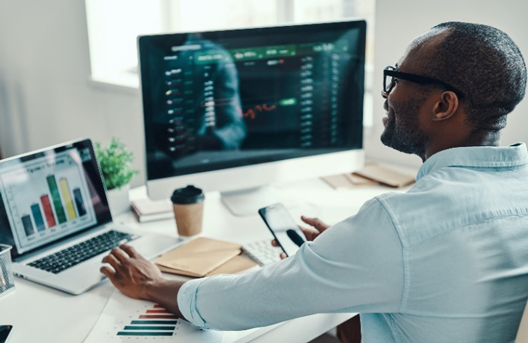
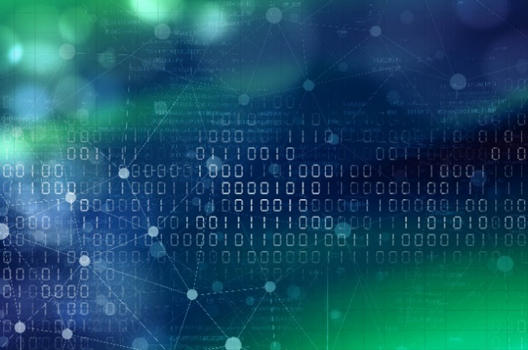
生産現場に製造実行システム(MES)を導入することで、計画から出荷までを作業手配・品質管理・製品在庫管理などの機能で効率化することができます。
「どのような原料をいくら使ってどのような製品をいくつ作るのか」「製品に対してどのような検査をするのか」など、製品独自の製造方法や品質管理方法をヒアリング・調査し、最適なシステムを提案します。
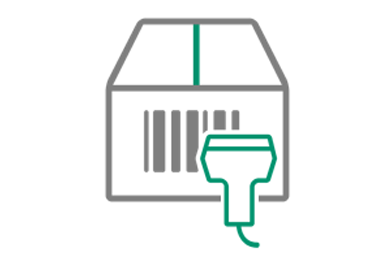
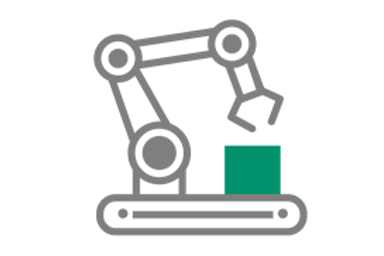
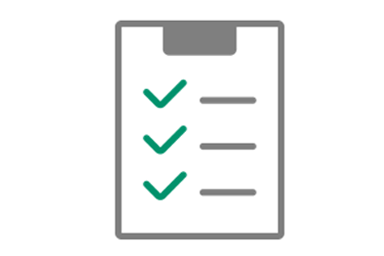
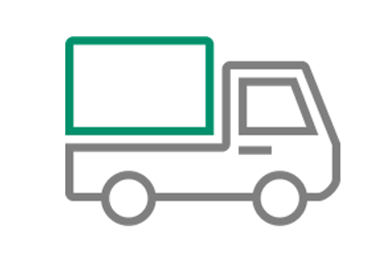
計画・製造・検査・出荷のすべてを効率化できるシステムを提案します。
問題点:計測機器の数値を紙に転記して帳票を作成すると、
- 読み間違い、書き間違いなどのミスが起こる
- 計測機器を見て回るので時間がかかる
- 紙で保管するので、過去の帳票を見つけるのが大変
施策
- 計測した数値の取得と帳票への記入を自動化する
- 帳票をデータとして保管する
効果
- 人が転記する必要がなくなり、負担や作業ミスを削減
- 過去の帳票をすぐに検索できる
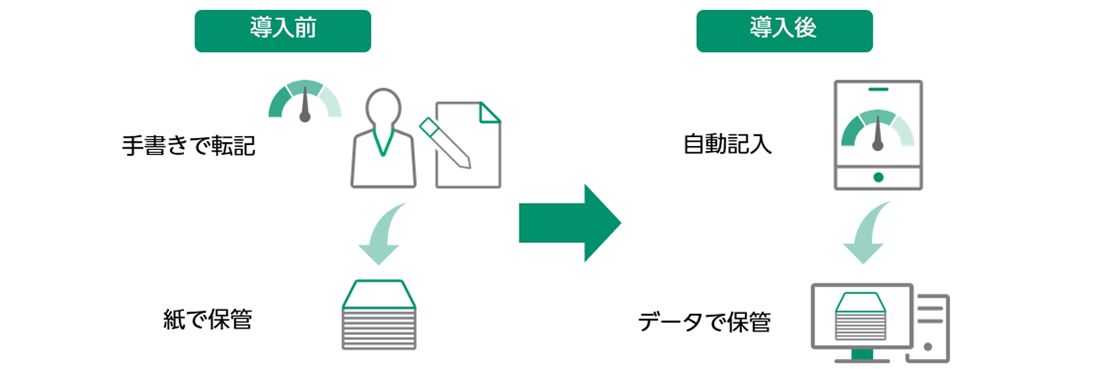
手書きで転記し紙で保管していた帳票を、自動記入により作成しデータで保管します。
課題
- 遠隔地の現場が見えず、検査結果をいつ承認すればよいのか分からない
→ 生産に待ちが生じてしまう
施策
- 工程の進捗をどこからでも確認できるようにする
- 現場で検査結果が入力されたら、承認者にメールを送信する
効果
- 遠隔地の生産進捗状況をいつでも把握できる
- 承認者は、メール受信後すぐに承認作業を行うことができる
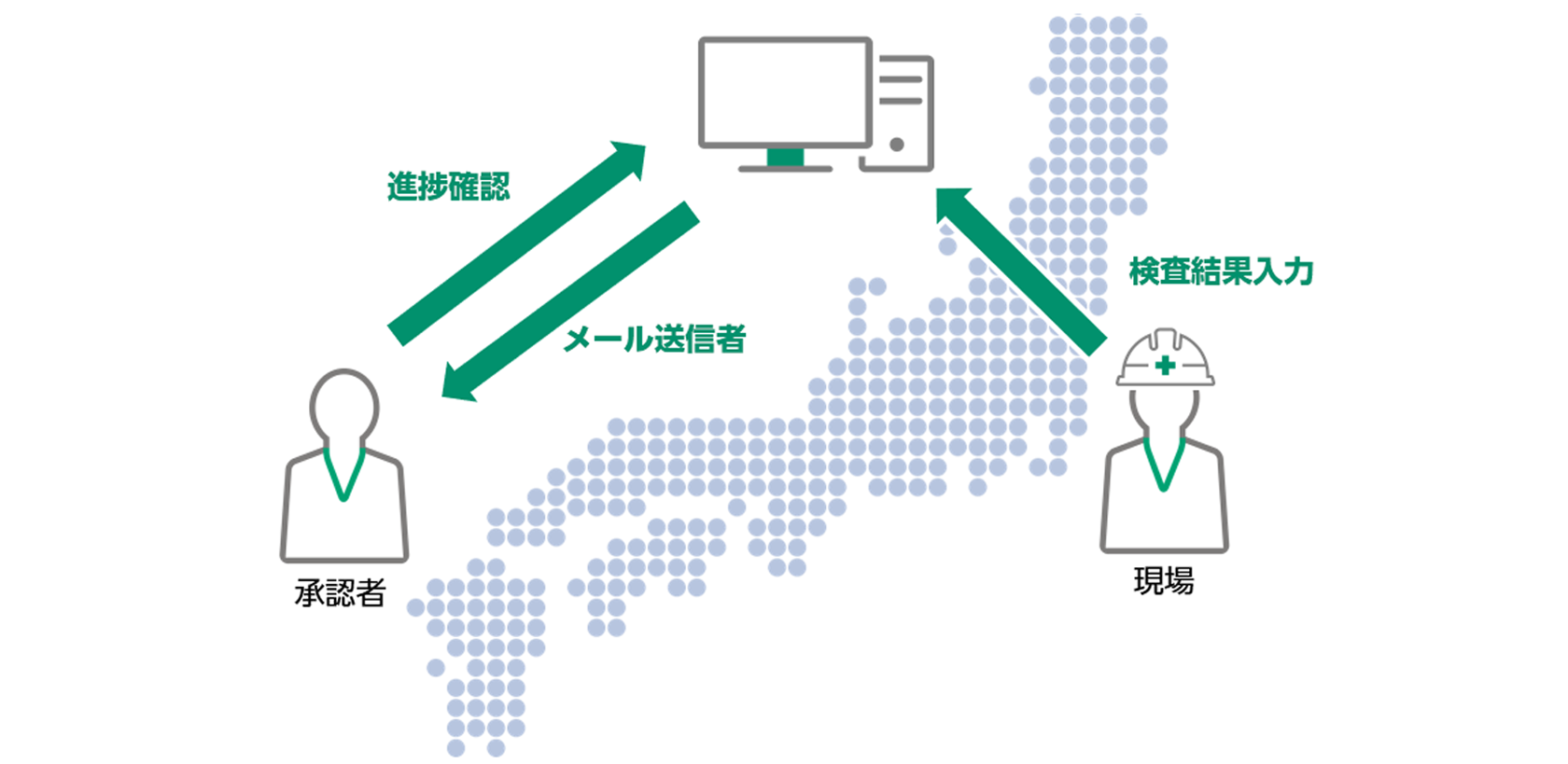
生産進捗状況をどこからでも確認でき、検査結果が現場で入力されるとすぐに承認者にメールが送られ承認のタイミングを知らせます。
さまざまなデータを組み合わせて解析を行うことで、製品の品質向上やロス削減など工場の利益率UPに繋がります。私たちは現場の要望や設備条件に合わせて収集するデータ・計測機器・ツールを選定し、ビッグデータを有効活用できる解析基盤を提案します。
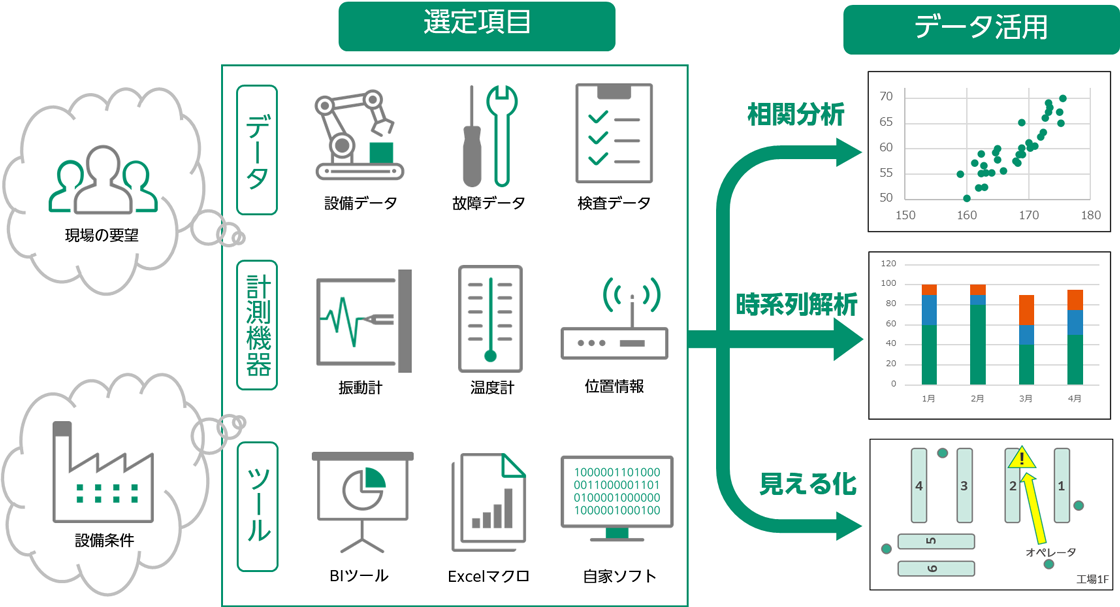
現場の要望や設備条件に合わせて収集するデータ・計測機器・ツールを選定し、相関分析・時系列解析・見える化などビッグデータを有効活用できる解析基盤を提案します。
問題点:故障により設備が停止した際、原因特定に時間がかかる。
- データが各所に点在し、データ収集に時間がかかる。
- グラフ化するためにデータを成型するのが大変。
→ 生産再開が遅れてしまい、製品を供給できない。
施策
- 生産データをデータベースへ一元化し、整形した状態で保管する。
- 保管されたデータをもとに見える化ツールを選定し、解析できる環境を提供する。
効果
- データ収集・整形の手間がなくなり、すぐに故障解析へと取りかかることができる。
- 素早く原因を特定し、生産再開することができる。
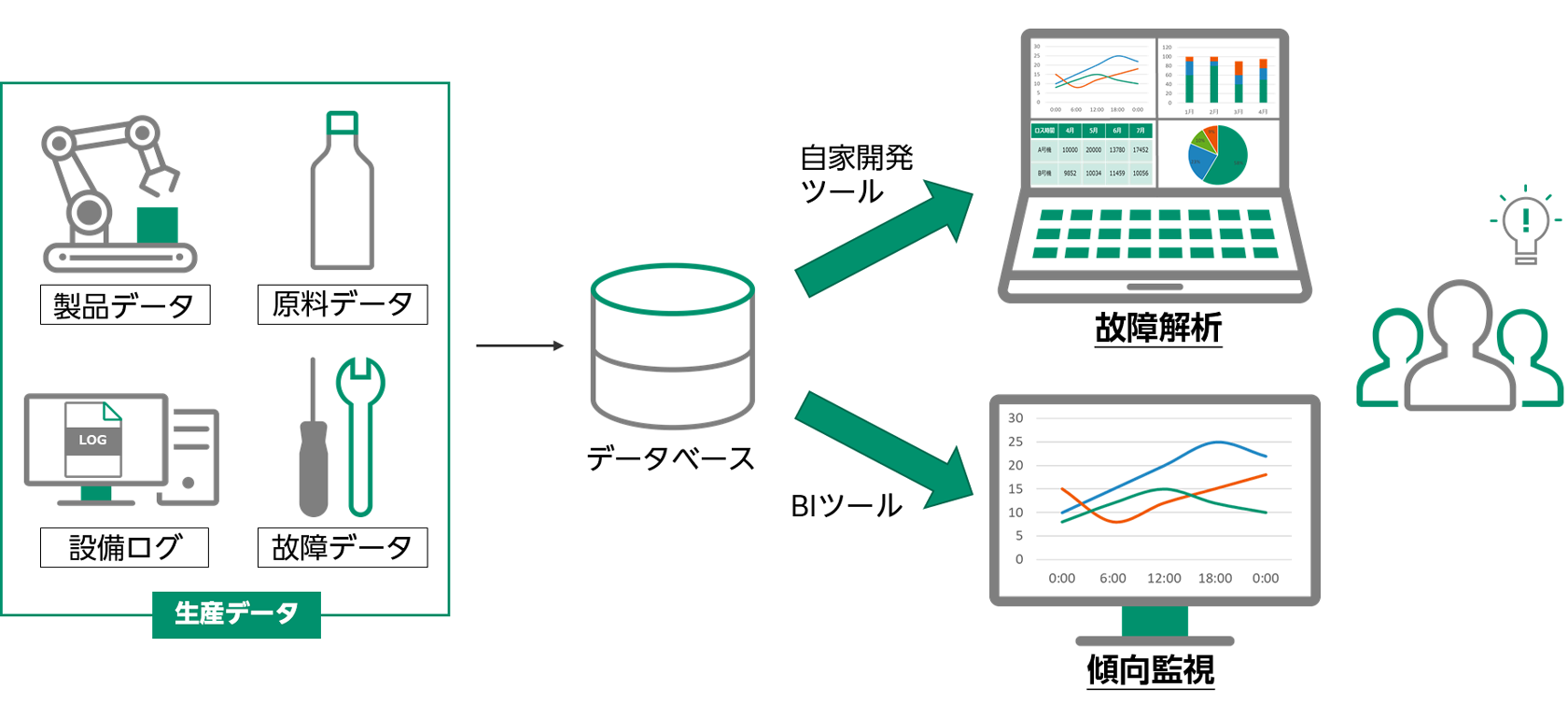
製品データ・原料データ・設備ログ・故障データなどの生産データをデータベースに蓄積し、現場の運用に適したツールを選定することで、故障解析・傾向監視などの解析基盤を構築します。
問題点
- 設備のトラブル発生時にオペレータが近くにいないことがあり、すぐに対応できない。
- 手の空いているオペレータがどこに居るか分からず、責任者が的確に指示を出せない。
施策
- ビーコンから位置情報を取得して表示することで、オペレータの位置情報を見える化する。
効果
- トラブルが発生した際、手が空いているオペレータに適切な指示が出せる。
- 素早く生産を再開し、製品が供給できる。
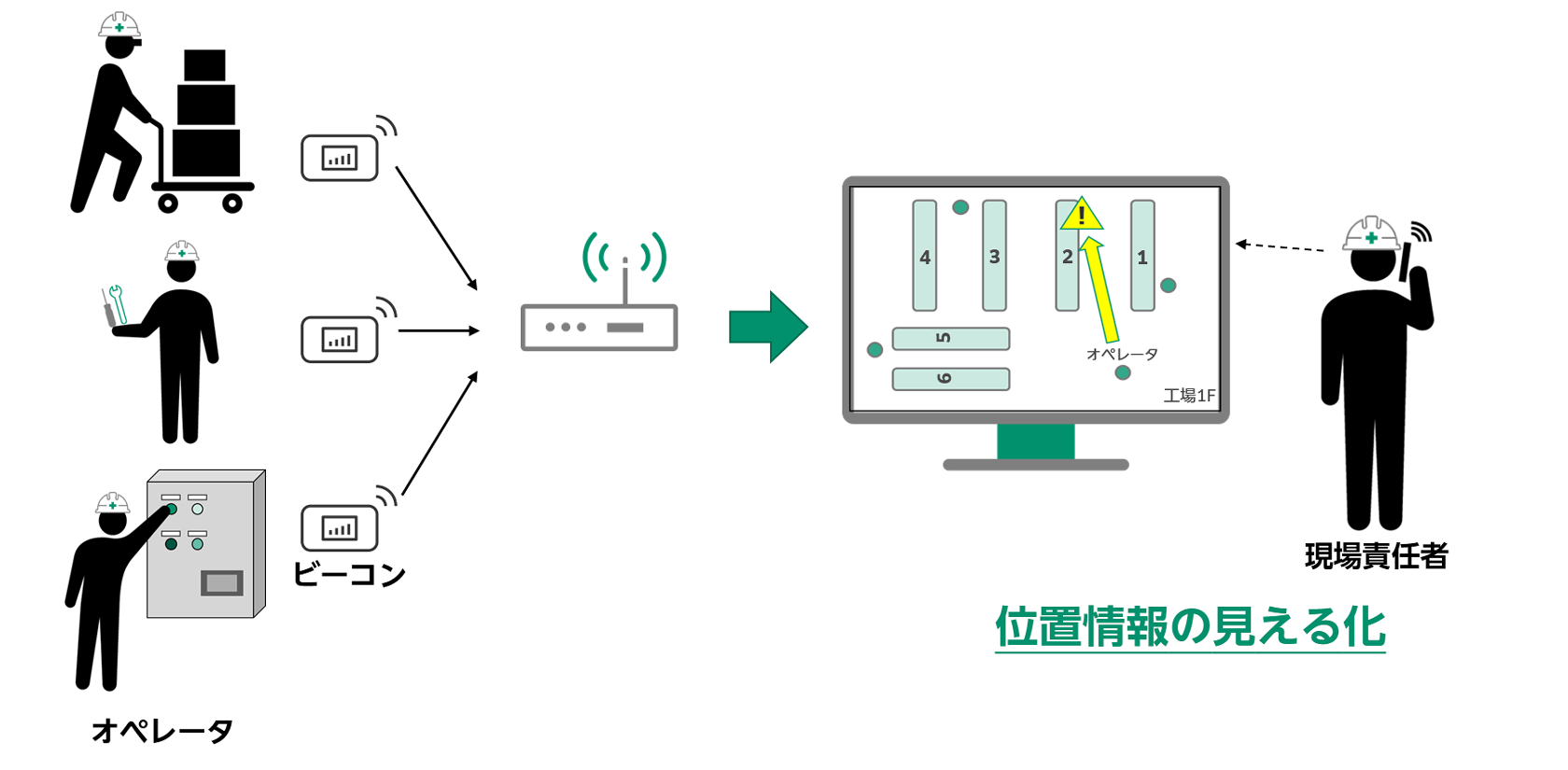
オペレータにビーコンを持たせることで位置情報を取得し、モニタにオペレータの位置情報を表示させます。現場責任者はオペレータの位置を常に把握することができ、トラブル発生の際に素早く指示を出すことができます。
危険な場所(高所、熱源、ロボット、etc.)や監視か所が多い現場では、画像処理を活用し、安全性や工数の削減を実現しています。現場の状況と担当者の声から必要とされる要件を捉え、それぞれの現場に合った方法を提案します。導入後も効果検証し、課題解決までサポートします。
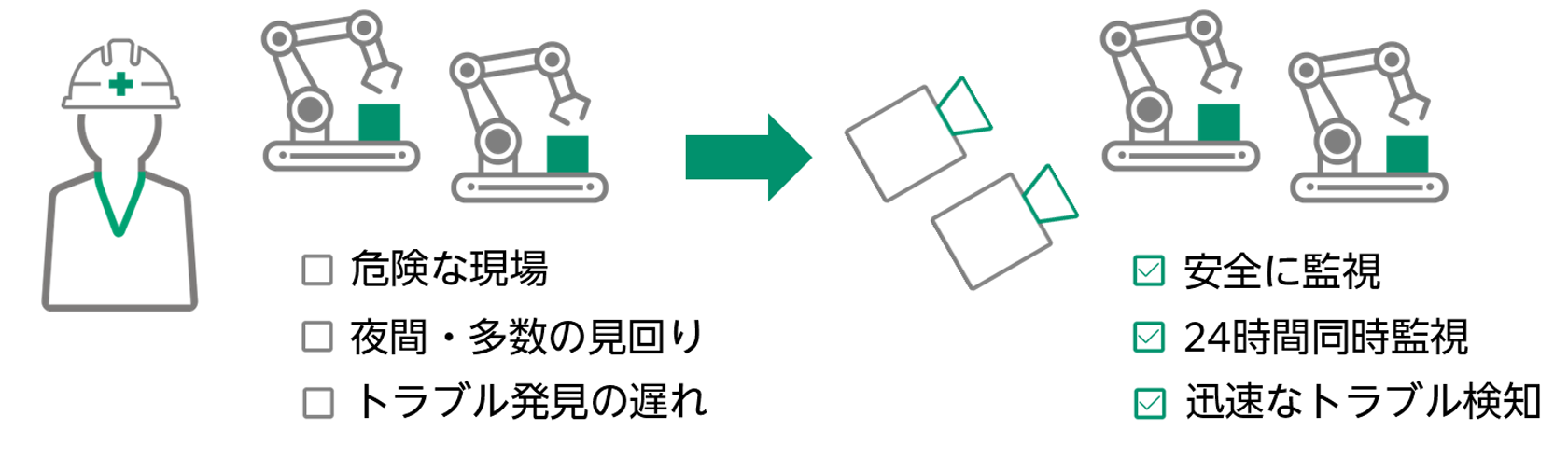
カメラを設置し、画像処理を活用することで、対象の多い定常監視作業や危険な現場での作業を削減できます。
見回りか所が多く、頻繁に見回りできない場合でも、トラブルの早期発見ができます。
問題点
- 誤作動によりロボットが間違った位置に製品を置いてしまう。
- そのまま自動で作業が進み、ロボットが製品と接触し製品が破損する。
施策
- カメラを設置、画像認識で製品の有無を自動判定し製品の配置ミスを分かるようにする。
効果
- 衝突を未然に防ぎ、製品の破損を防止できる。
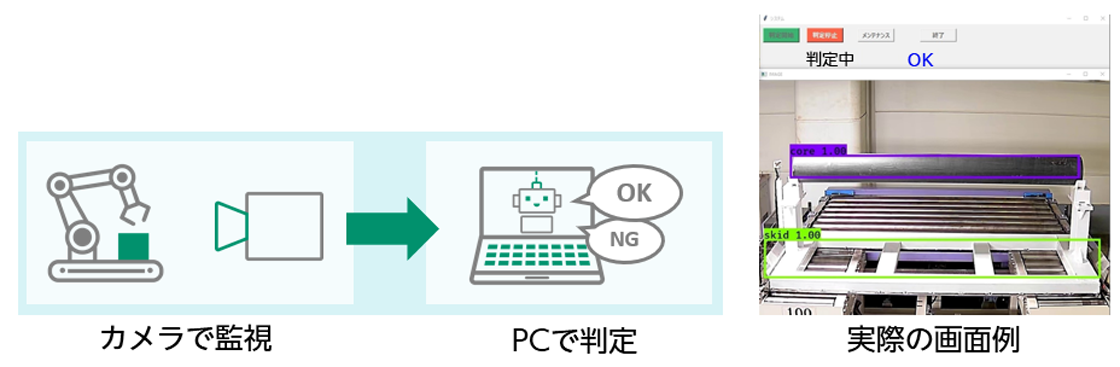
カメラで撮影した画像を自動判定することで、製品の配置ミスを検知することができます。
問題点
- 普段立ち入らない場所に製造管理のサーバがあり、故障が発生しても気付かない。
- 発見が遅れてしまうとサーバが停止し、製造停止につながる。
施策
- カメラを設置し、サーバを常時監視する。
- 異常を検知した際、担当者にメールを送信する。
効果
- 故障の早期発見が可能になりサーバ停止を回避できる。
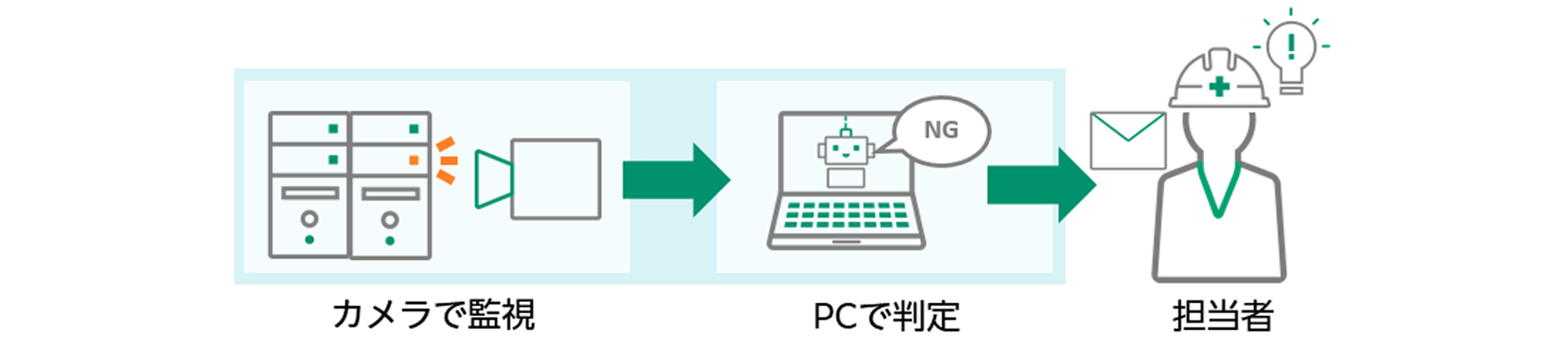
カメラでサーバを監視して、異常を検知した時に担当者へメールを送信します。