富士フイルムビジネスイノベーションがご支援する
生産環境の最適化による
「スマートファクトリー」の実現
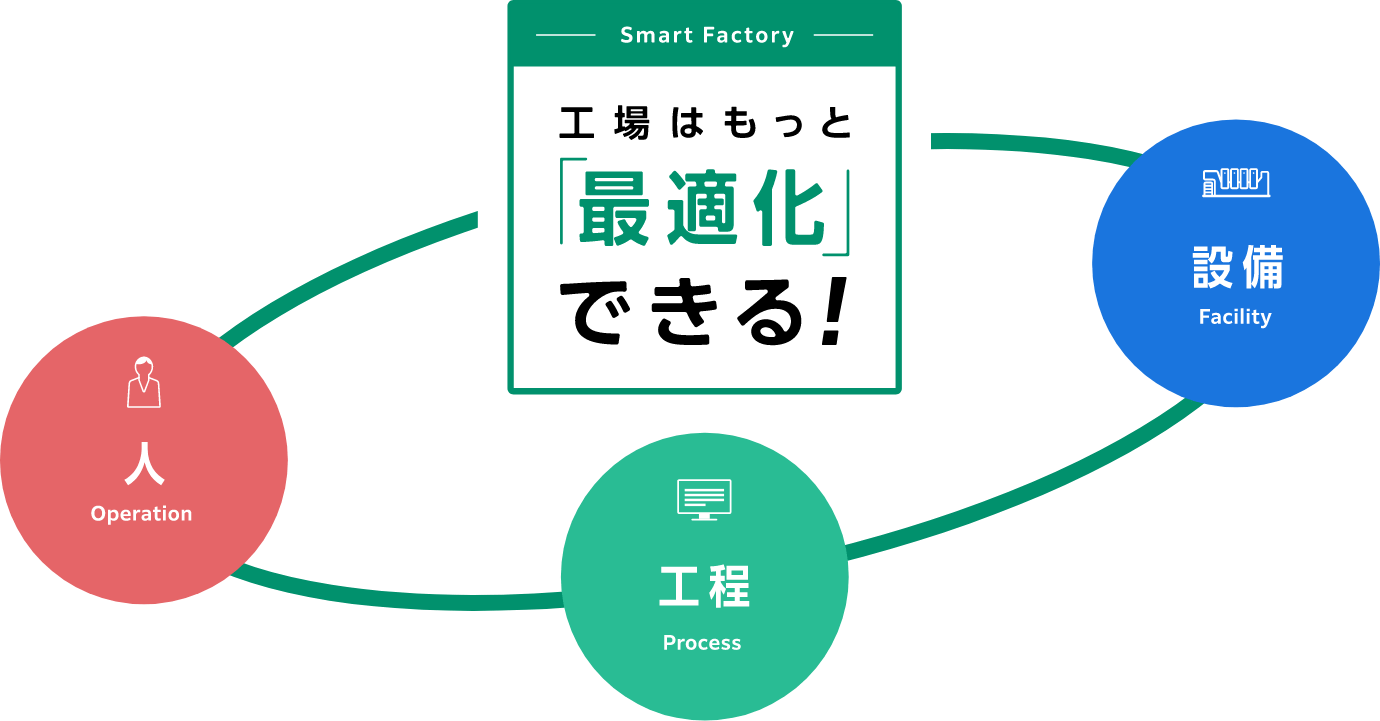
無駄を省き効率化し、利益率を改善『利益を生む生産環境』の実現へ
スマートファクトリーに取り組む必然性富士フイルムグループがご支援する生産環境の最適化
印刷業界は今「人材不足」「小ロット・多品種対応」「稼働率低下」といった課題への取り組みに迫られています。
富士フイルムグループは印刷物の生産における「人」・「工程」・「設備」に関する情報をシームレスにつなぎ、
それぞれの観点から生産環境の最適化をご支援します。
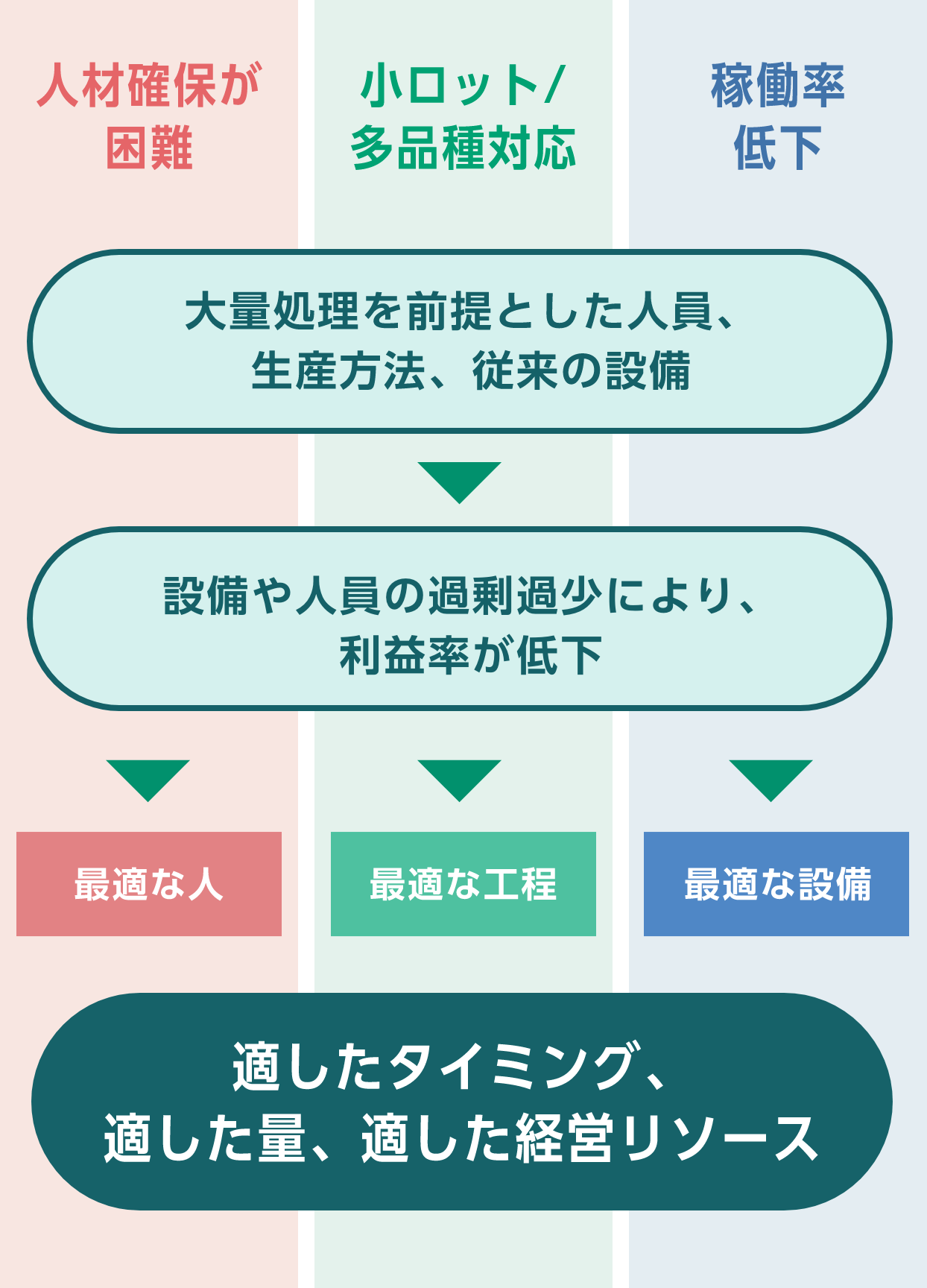
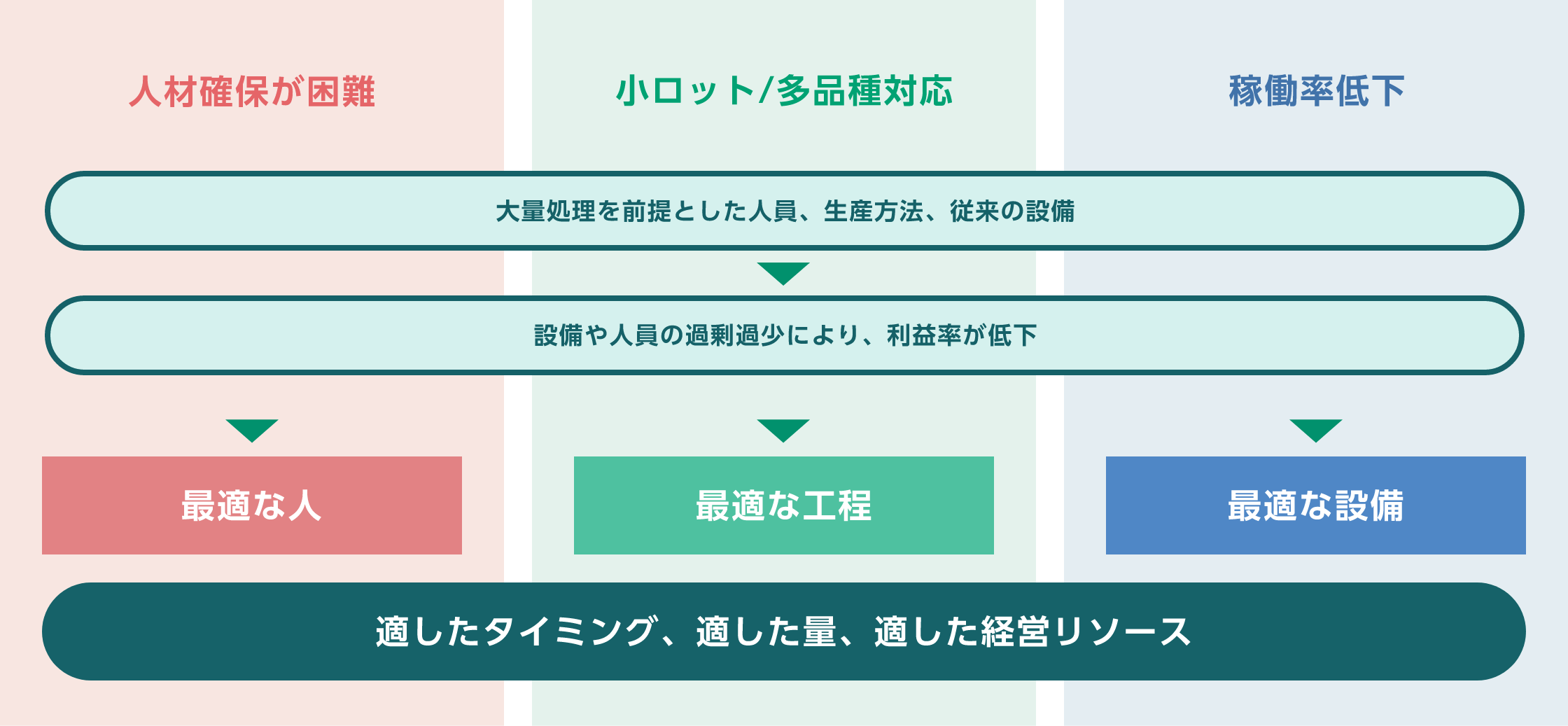
スマートファクトリーの実現に向けた3つの最適化ポイント
01人
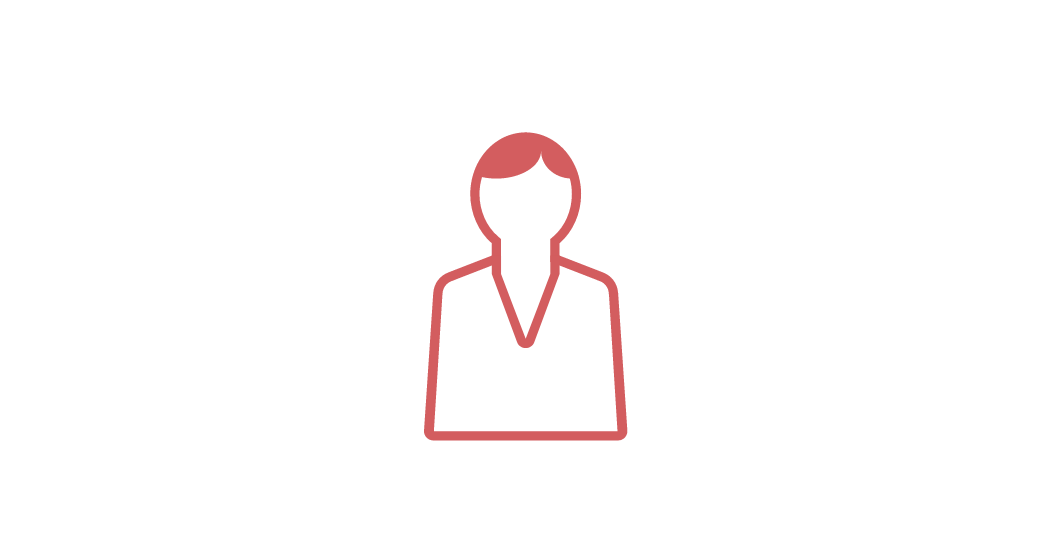
業務標準化により、スキルレスで『人に依存しない』生産工程の実現
02工程
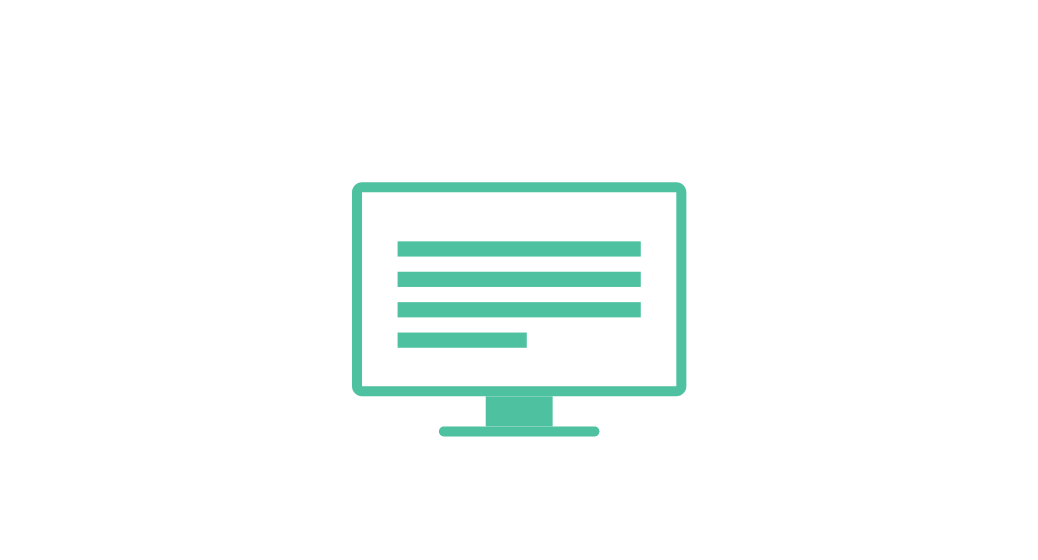
稼動状況・進捗状況の把握(無駄や滞留の可視化)による『継続的な改善活動』の実現
03設備
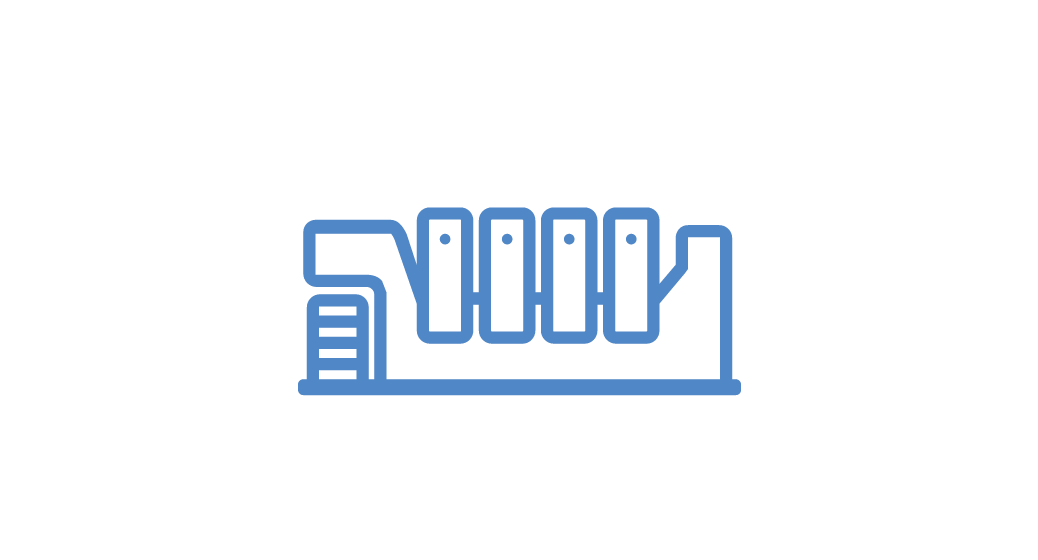
無駄を省き、生産部数に合わせた柔軟な設備選択による『可動率向上』の実現
『スマートファクトリー』の実現
「人」・「工程」・「設備」の3つの観点から生産環境の最適化を図ることが
自動的・自律的に稼働する「スマートファクトリー」につながると考えます。
スマートファクトリーがもたらす3つの効果
『人』にもたらす効果
Before
- 各工程/設備に担当者が張り付く専任配置が前提で、生産状況に応じた柔軟な人員配置が難しい
- 段取りに時間と技能を要し、熟練技術者へ依存している
- 技術の習得が難しいため人材育成に時間がかかり、人材確保が難しい
After
- 機械/システムとの協働により、従業員の業務を適正化
- ワークフローやRPAの活用により作業標準化を進め、スキルレスで特定の人に依存しない生産環境を実現
- 付帯業務の削減により、従業員のスキルアップや多能工化を推進
『工程』にもたらす効果
Before
- 生産状況や進捗状況が可視化されていないため、他工程の状況が分かりにくく、滞留が生じやすい
- 人を介在する作業が多いため、データの取得が難しく、科学的に改善ポイントを見出すことが難しい
- 各工程内の改善活動は進めやすいが、全体最適の観点を持った工程改善が難しく、大きな効果を上げにくい
After
- 工程のデジタル化・自動化によりデータを取得。分析・シミュレーションにより、全体最適の観点で改善ポイントを科学的に発見
- モニタリング・解析を続けることで、無駄や滞留を可視化し、継続的な工程改善活動を可能に
『設備』にもたらす効果
Before
- 小ロット多品種生産のニーズが高まり、稼働率向上につながると考え増強してきた設備が過剰となった
- 印刷、後処理工程の設備のバランスが悪く、設備使用待ちの滞留が生まれている
After
- データ/生産マネジメントと連携することで各設備の負荷を可視化し、予防保全によるダウンタイムの短縮と品質向上に貢献
- 工場全体の可動率向上という観点で遊休設備の見直し、最適生産を実現
富士フイルムグループが考える
印刷スマートファクトリー
『データ/生産マネジメント(Revoria One Production
Cockpit)』を中心に工程のデジタル化と自動化を進め、工程全体を統合管理。さらに、蓄積されたデータを解析し、シミュレーションを行うことで継続的な工程改善を支援します。
スマートファクトリーの実現にあたっては、生産性の向上のみならず、業務品質を担保した現実的な運用と、柔軟性と可用性を考慮した工程設計をご提案します。
このような取り組みによって三適生産(タイミング・量・経営リソース)を実現し、「顧客提供価値の最大化」と「利益最大化」を両立できる『スマートファクトリー』を実現していきます。
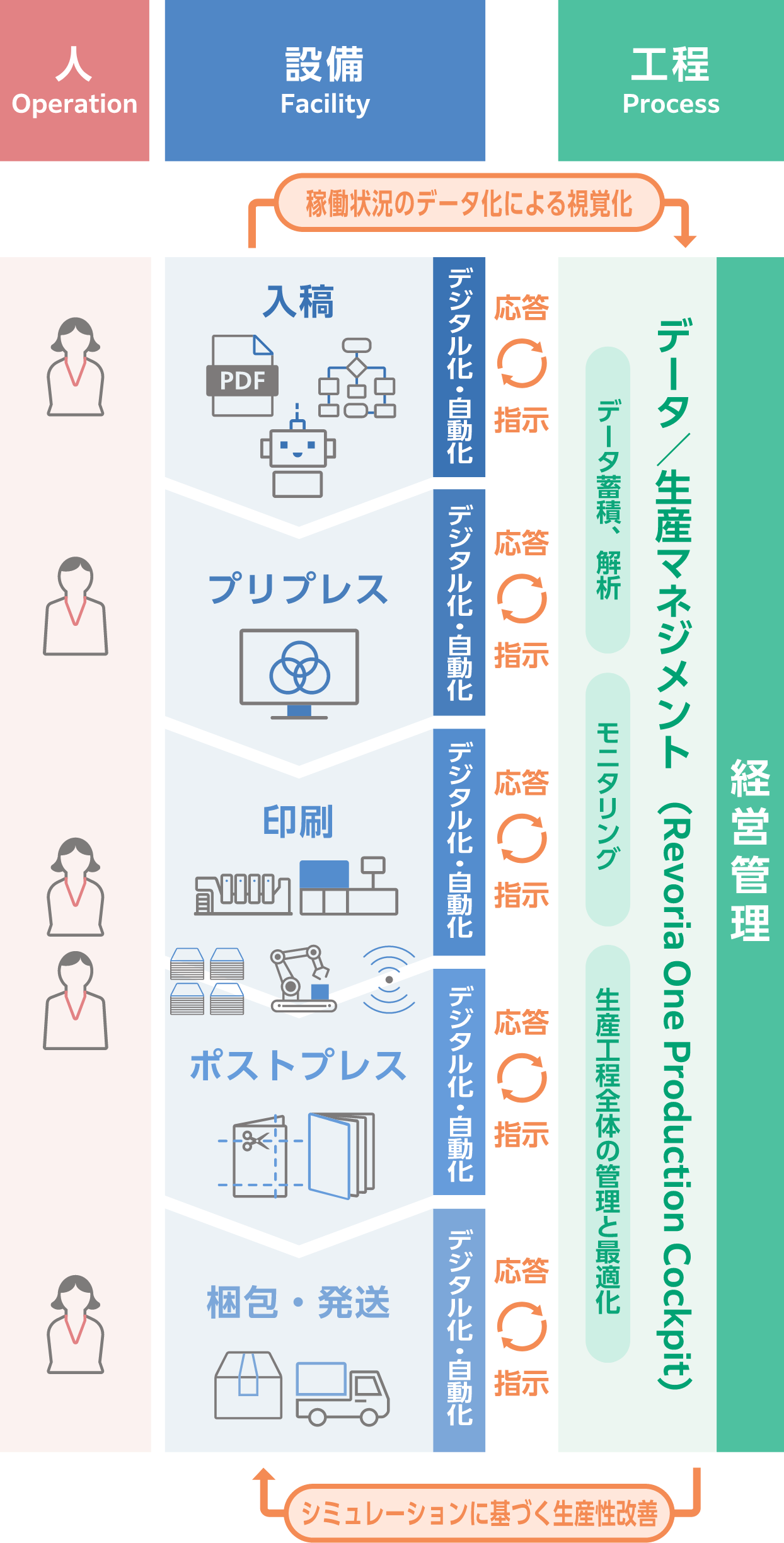
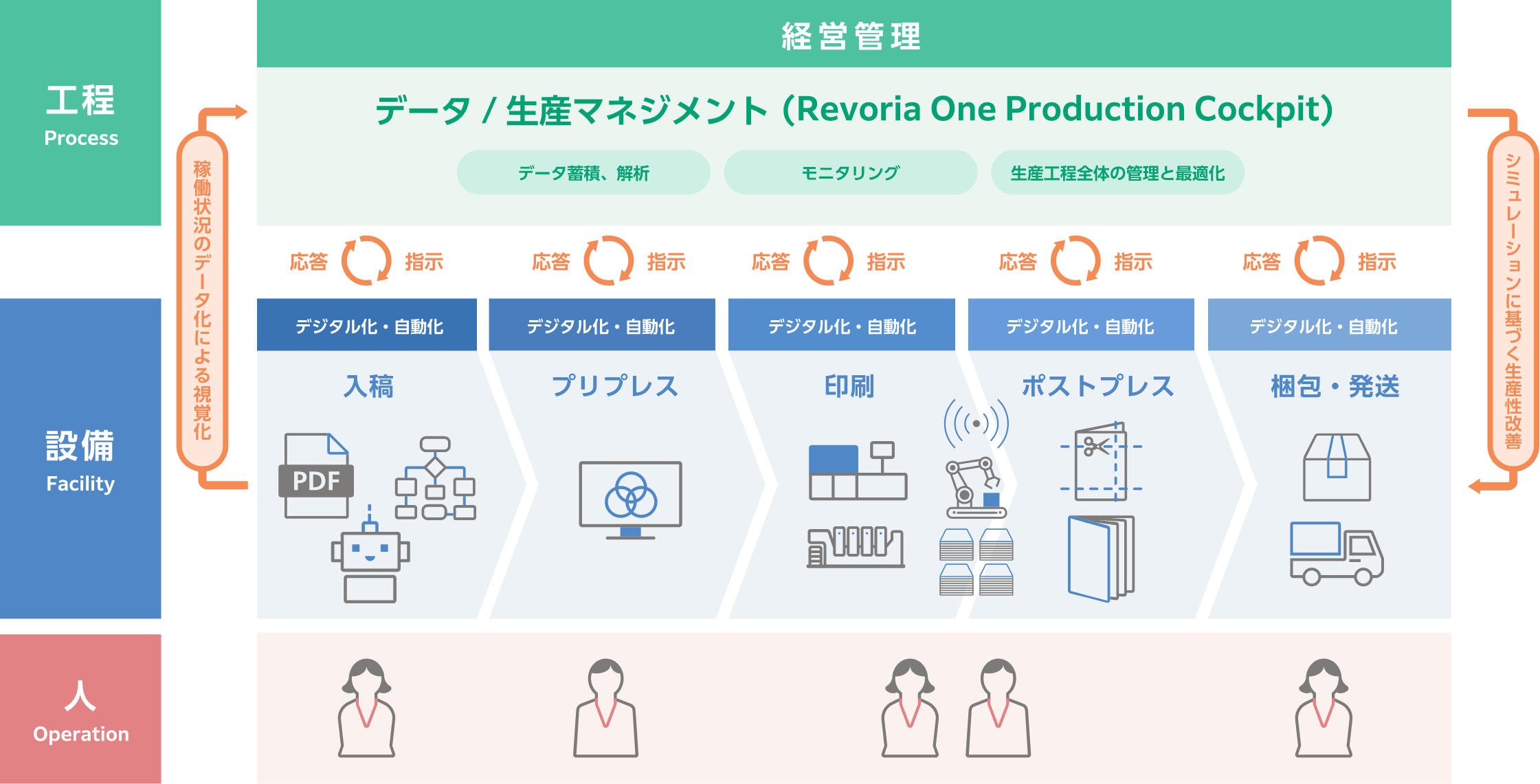
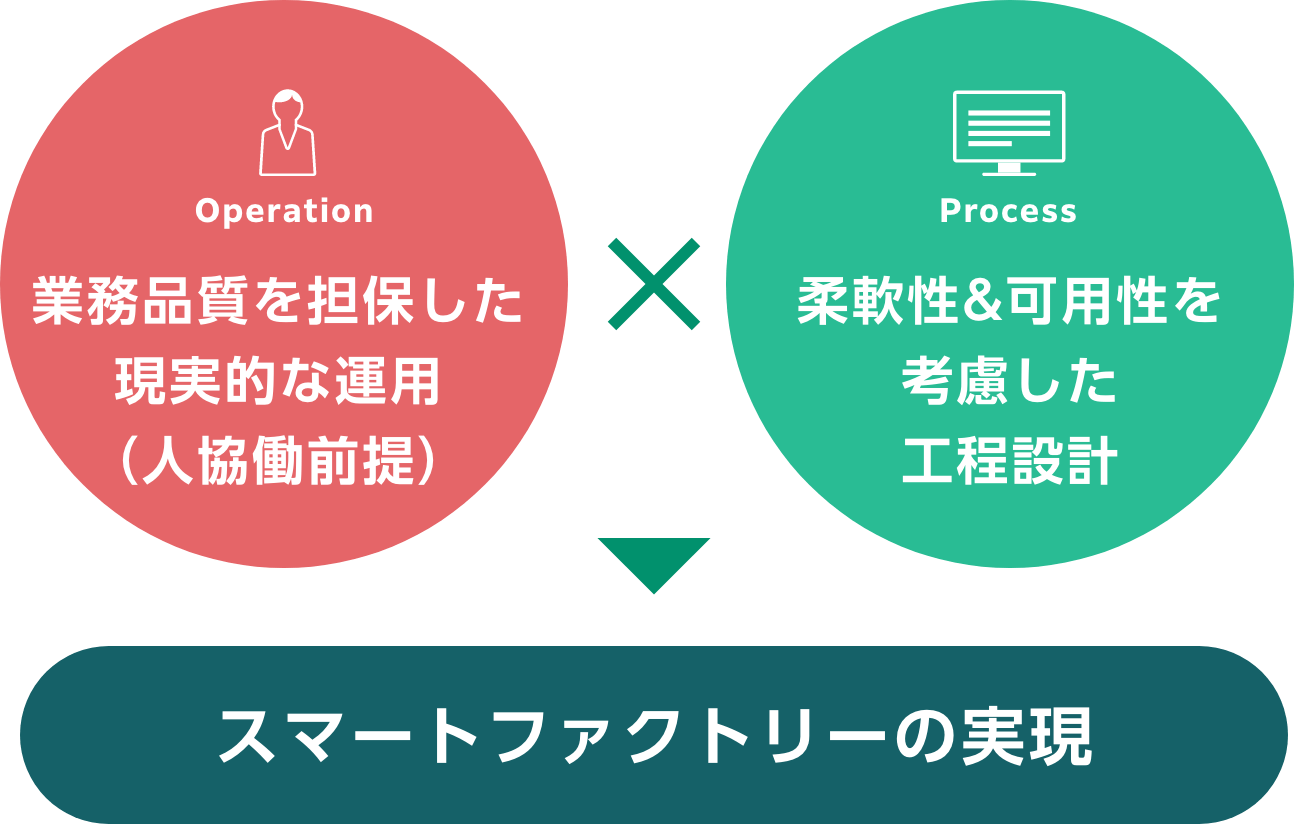
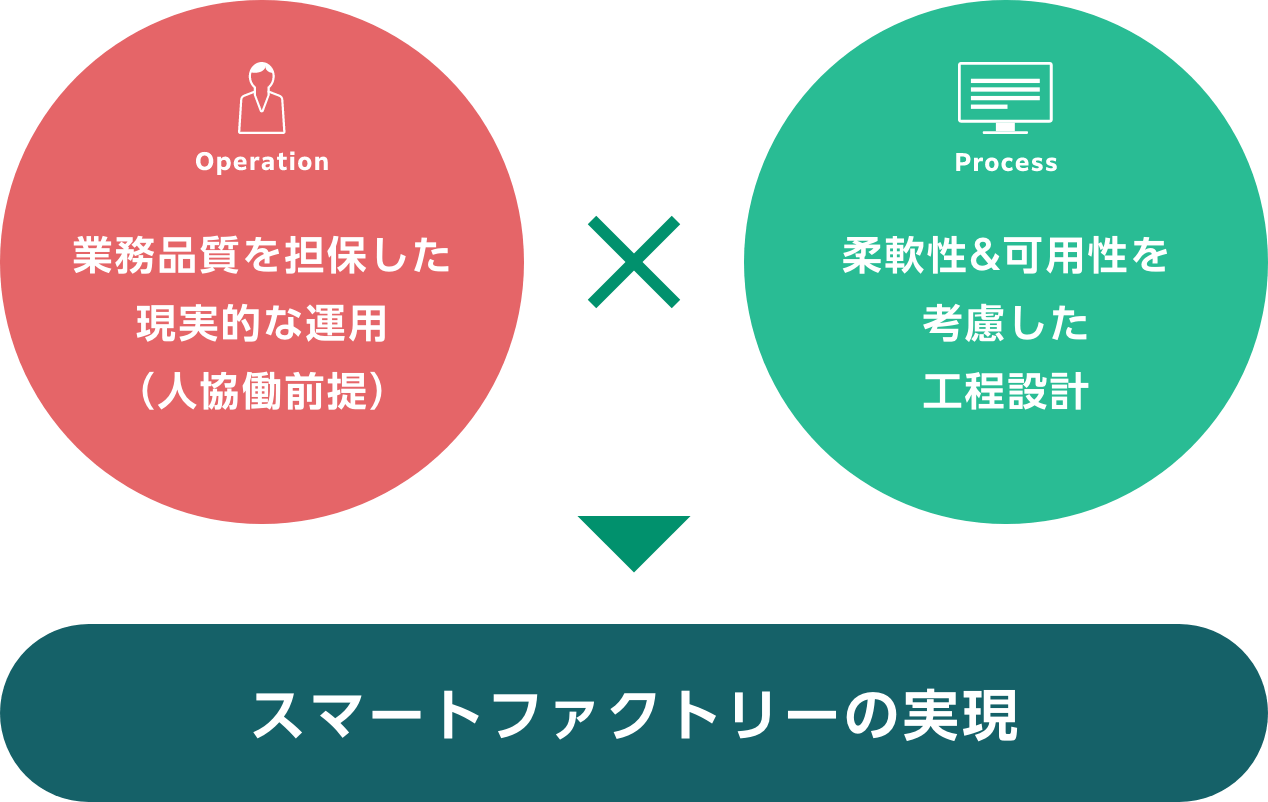
スマートファクトリーの
取り組みステップ
まずはデータを活用して現状を見える化。その後、『人』・『工程』・『設備』の観点で最適な生産リソースを科学的にシミュレーションし、自動的・自律的に稼働する『スマートファクトリー』を目指します。
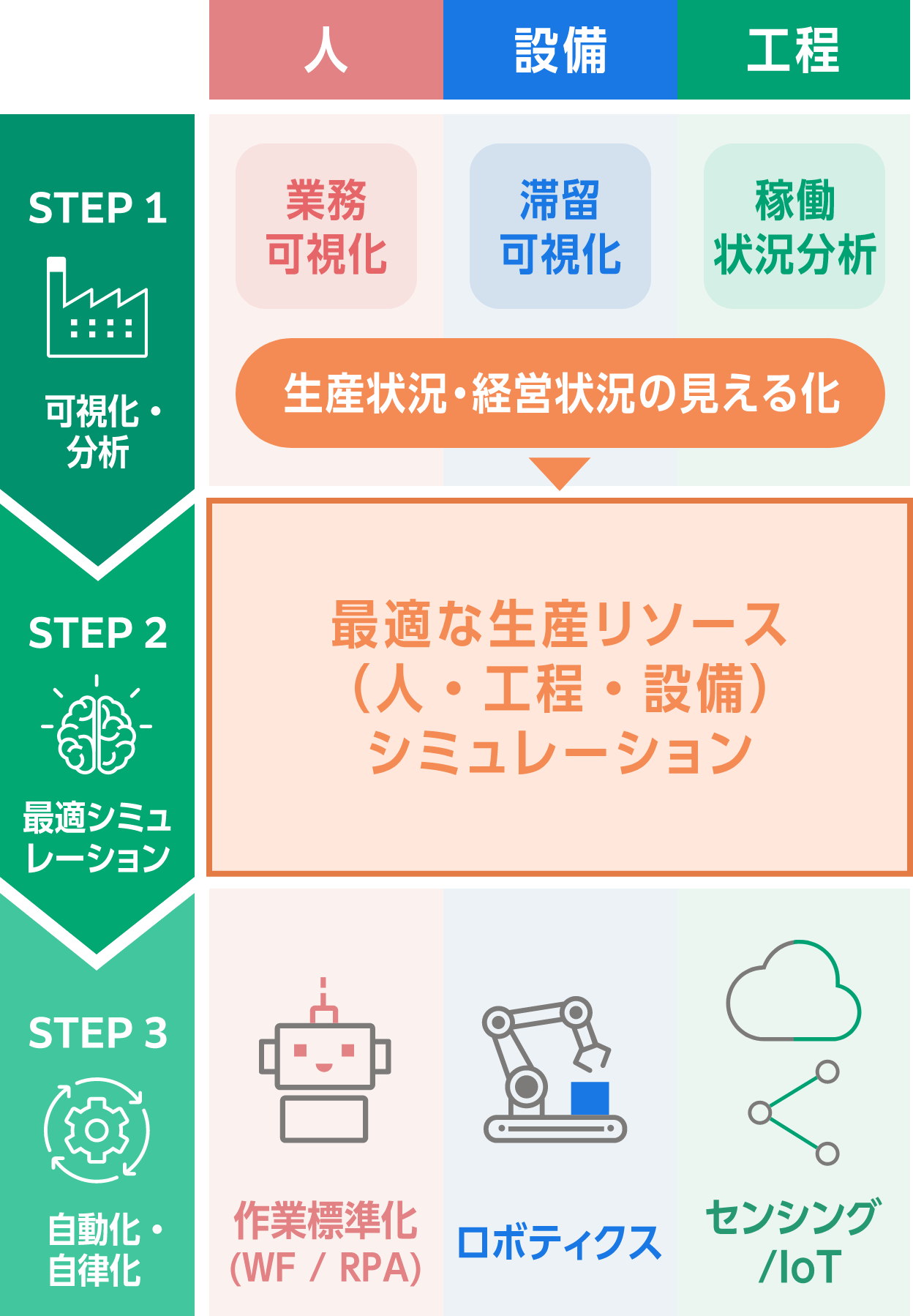
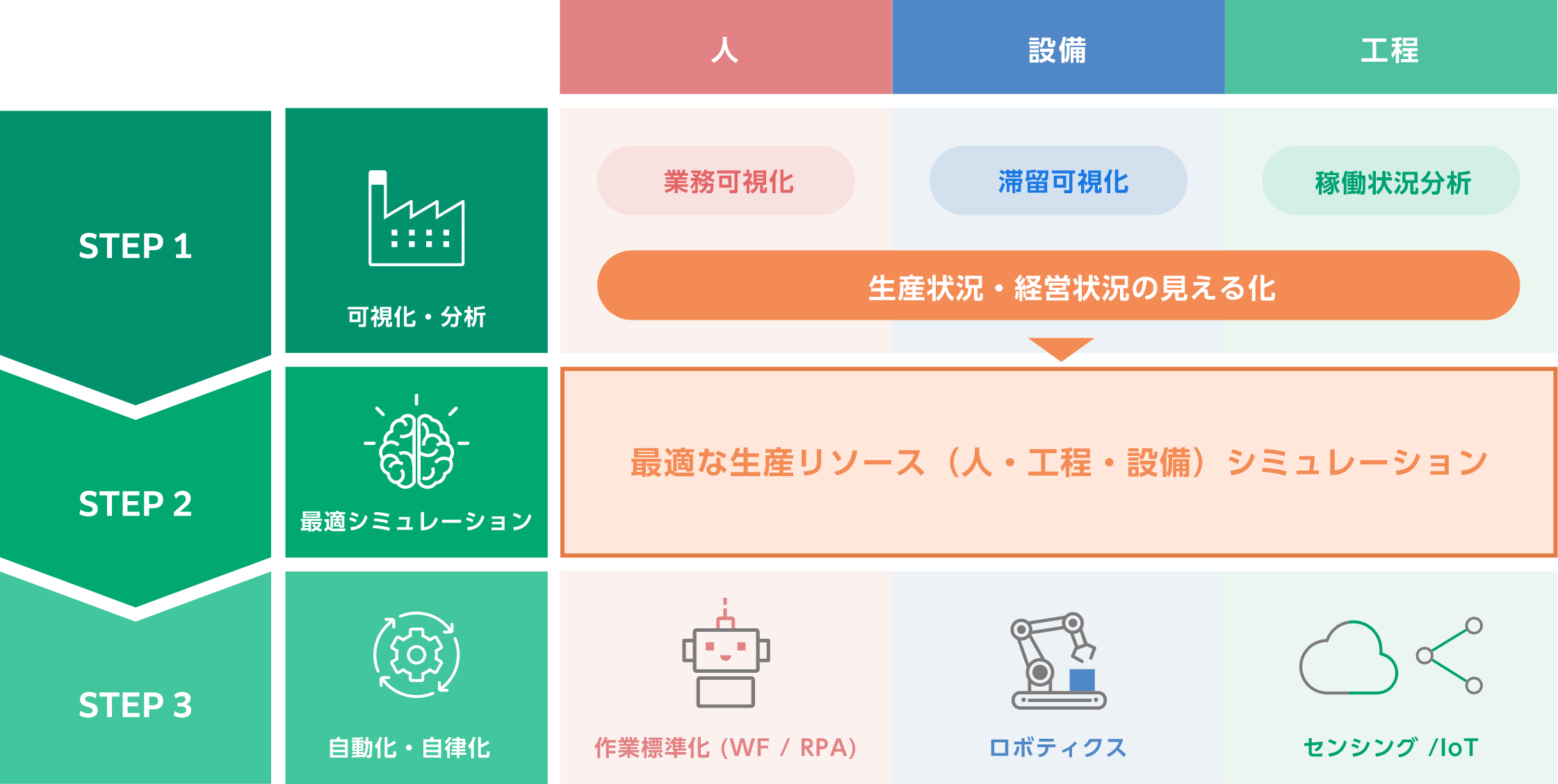
スマートファクトリー事例
スマートファクトリーの
ご提案
わたしたちがスマートファクトリーの実現に向けて、各プロセスでご提供する事例をご紹介します。
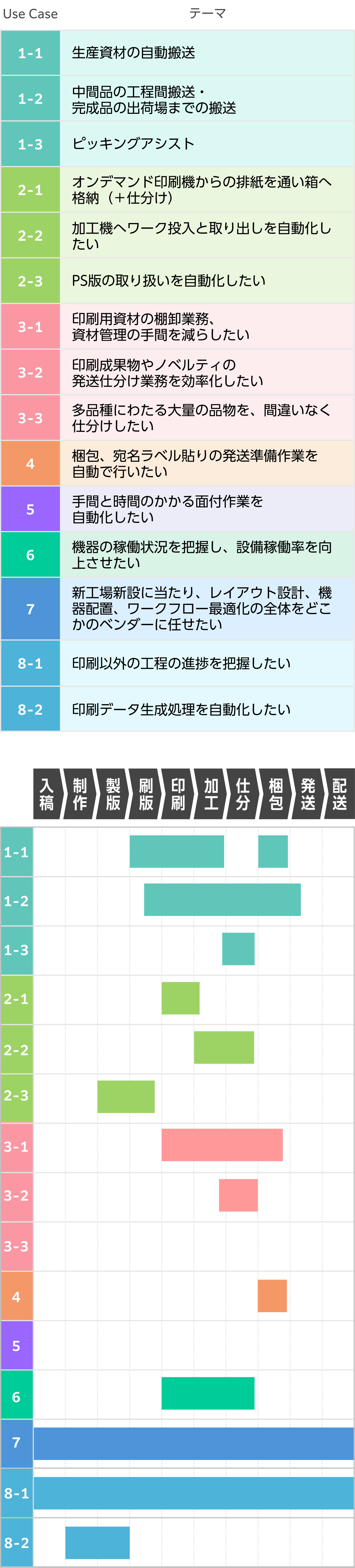
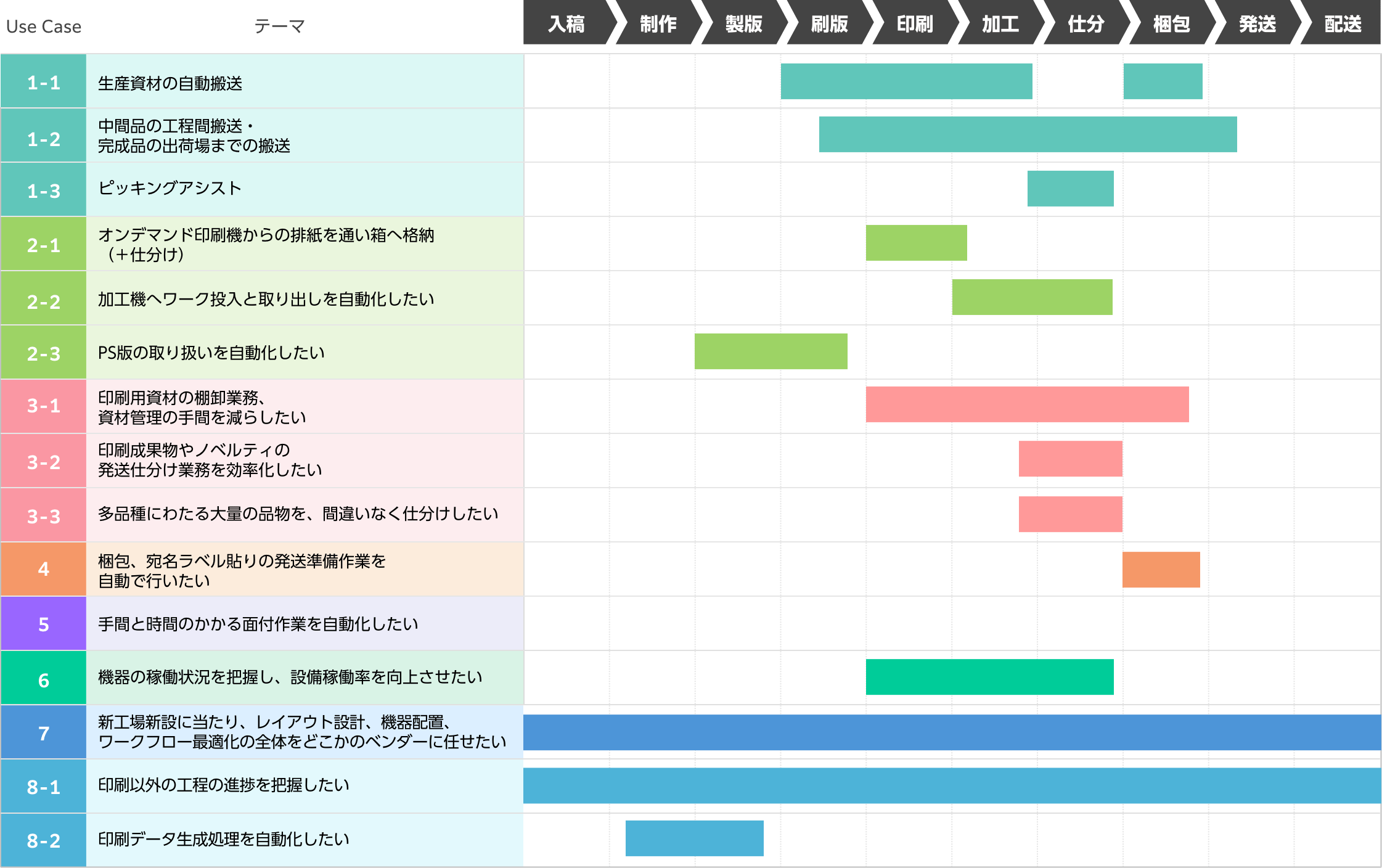
-
印刷工場の生産性/人材確保・育成などに関するお悩みはお気軽にご相談ください。
印刷事業に関するお悩みはお気軽にご相談ください
- ご相談受付中