高度な素材設計技術を活かし、多彩な高性能インクを開発
UVインクの技術
1. ソルベントUV ハイブリッド インク
優れた柔軟性と、高耐久性・高耐擦性を両立
富士フイルムは、高度な素材設計技術を活かして、「光沢性に優れたソルベントインク」と「後加工性に優れたUVインク」の特長を併せ持つユニークなハイブリッドインクを開発しました。
ハイブリッドインクの特長&メリット
ソルベントインク同様に膜が薄い
⇒ 基材の風合いを残したまま「光沢のある美しい印刷仕上がり」が得られます
基材との密着が強くインク膜の柔軟性が高い
⇒ 延伸を要する用途に最適です
「高耐久・高耐擦性」を兼ね備え、印刷物の取り扱い性にも優れる
⇒ 印刷後ただちに後加工に入ることができ、生産性が向上します
インクの安定性が高い
⇒安定的な吐出が可能で、効率的な印刷が可能となります
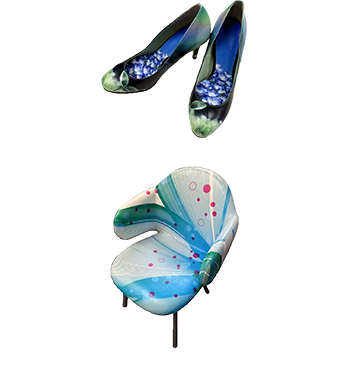
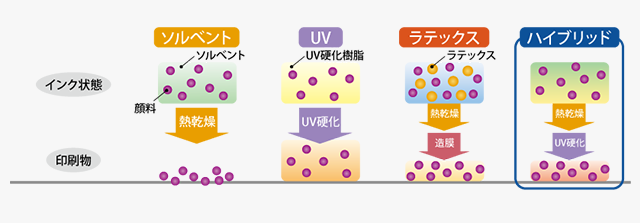
ソルベントインク
揮発性の溶媒に樹脂を溶解させ、顔料を分散させたインク。インクジェット後、溶媒を乾燥させると基材には顔料と少量の樹脂しか残らず「薄い膜」になるため、質感や柔軟性に優れた印刷物が得られます。
UV インク
液体状のUV 硬化樹脂に顔料を分散させたインク。インクジェット後、UV 光をあてて樹脂を硬化させると、基材と強く接着した「強い膜」が瞬時に形成されます。
ラテックスインク
水性溶媒に顔料と樹脂 (ラテックス) を分散させたインク。インクジェット後、加熱乾燥させるとラテックスが溶けてフイルム状になり、「ソルベントインクよりも強い膜」が形成されます。反面、吐出前のインクを乾かさないよう、取り扱いに注意が必要です。
ハイブリッドインク
揮発性の溶媒に、UV インクの素材を分散・溶解させたインク。インクジェット後、溶媒を乾燥させUV 光で樹脂を硬化させることで、基材接着性のよい「強い薄膜」が瞬時に形成されます。
シンプルな描画プロセス
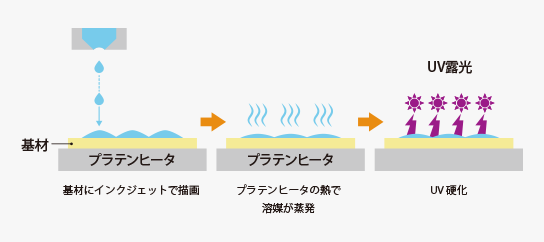
一般的なソルベントインクの乾燥技術とUV露光技術の組み合わせにより、『ハイブリッドインク』ならではの優れた特性をフルに引き出すことができます。
2. 高延伸性UVインク(KVインク)
インクジェット方式による「真空成形の加飾印刷」を実現
室温では強固な膜となり高温では基材の伸びに追従する、相反する二つの要求に同時に応える高延伸性UVインク『KVインク』は、インクジェット方式での「真空成形の加飾印刷」を可能にしました。二律背反を解くカギは、富士フイルム独自の素材技術。インク薄膜が柔らかいと延伸性に優れる反面、転写の原因になってしまうので、「柔らかい膜」をサポートする特殊モノマーを最適なバランスで加えることで、「常温での充分な膜強度」を実現しました。
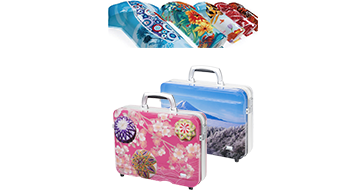
温度vsインク薄膜の弾性
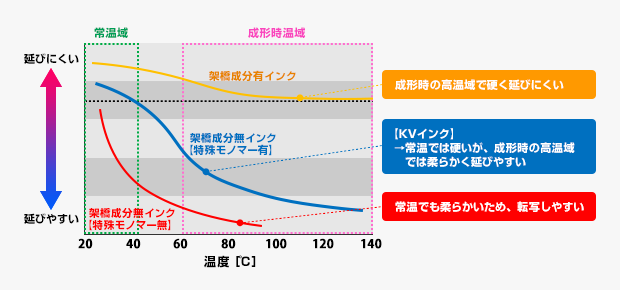
インク薄膜のミクロな構造 (イメージ)

水性インクの技術
1. 独自の顔料分散技術
富士フイルムならではの高次元な顔料分散技術
微小粒子である顔料を長期間安定的に分散させることは、インクジェット用インクにとって重要な要素であり、「吐出性能」「印刷画質」「インク膜の性能」へ大きな影響を及ぼします。富士フイルムは、立体構造と電気的な特性によって安定した性質を示す高分子分散剤を開発し、各種水性インクに導入。分散剤を架橋させることで分散剤自体の脱離を抑制する独自技術により、各種溶剤や樹脂などのインク処方設計に対するロバスト性が大幅に向上しました。インク処方設計の幅が大きく広がると共に、インクジェットの応用範囲が一気に拡大します。
顔料分散構造 (イメージ)

一般的な顔料分散では、分散剤 (ひも状のポリマー) が顔料に吸着しています。インク化のための新たな素材が加わると、顔料から分散剤が脱離しやすくなり「分散の安定性が低下する」ことがあるので、インクの素材を注意して選定する必要があります。
富士フイルム独自の顔料分散技術では、分散剤同士が顔料を閉じ込めるようにして互いに架橋するため、 分散剤の顔料からの脱離が大幅に抑制されます。 そのため、インク素材の選択肢が大きく広がります。また、高度な精製技術で不純物を除いているため、安定性に優れる吐出が期待できます。