2022.05.26
タクトタイムとは?計算方法やサイクルタイム、リードタイムとの違いも解説
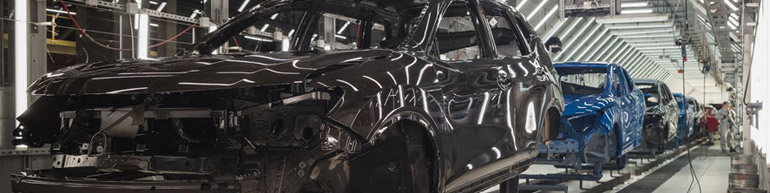
製造業における生産性向上を考えるときに、避けては通れないのがタクトタイムです。似たような言葉にサイクルタイムやリードタイムがあり、違いや計算方法がわからないという人もいるでしょう。業務改善や生産性向上には、これらの違いや計算方法を理解しておく必要があります。
今回はタクトタイムの意味とサイクルタイム・リードタイムとの違い、タクトタイムの使い方とタクトタイムとサイクルタイムが製造業に与える影響を解説します。製造現場の業務改善を検討している人は、タクトタイム・サイクルタイムの見直しを図りましょう。
タクトタイムとは
タクトタイムとは、ひとつの製品を製造するのに必要とする時間のことであり、別名ピッチタイムとも呼ばれています。名前の由来は指揮者が使用する指揮棒(タクト)です。
生産工程において、顧客から何をいつまでに作ってほしいかの要望を聞いたのち、1日あたりの生産必要数を納期で割って算出します。導き出された1日あたりの生産必要数で1日の定時稼働時間を割ることで、1時間あたりの生産必要数がわかります。それをさらに製品ひとつあたりの時間に直しますが、この製品ひとつを生産するのに必要な時間をタクトタイムと呼んでいるのです。
わかりやすく、計算式で表すと次のようになります。
【タクトタイムの計算方法】
タクトタイム=1日の定時稼働時間÷1日の生産必要数(最終的な生産必要数÷納期までの日数)
なお、タクトタイムの計算は1日の定時稼働時間を使用する必要があります。定時稼働時間とは、稼働時間から休憩時間などを引いておかなければなりません。タクトタイムの計算でよくある間違いであるため、算出する際には注意が必要です。
タクトタイムとサイクルタイムの違い
タクトタイムによく似た言葉に「サイクルタイム」があります。サイクルタイムとは、ひとつの製品の工程開始から完了までの1サイクルに対して実際にかかる時間のことを指し、タクトタイムとよく混同されます。しかし、実際には意味が異なるため、注意しなければなりません。
タイムタクトは、顧客から依頼された生産数をこなすため、1個あたり何秒で生産できるかを算出するものです。視点が顧客からであることが重要なポイントです。一方のサイクルタイムは、自社で抱えている生産設備で製品1個を生産するのにかかる時間を表しています。こちらは自社目線であり、それぞれの視点が異なります。
タクトタイムとリードタイムの違い
もうひとつ、製造現場で使われるよく似た用語に「リードタイム」があります。これは製品の発注から納品までの一連の工程にかかる時間のことを指し、タクトタイムとは表している時間軸が異なります。「手配番数」「手番」とも呼ばれるものです。
リードタイムには、「生産リードタイム」「調達リードタイム」「納品リードタイム」などの種類が存在します。要素によって呼び名が違いますが、すべてタクトタイムとは異なるものを差していることを覚えておきましょう。
タクトタイムの使い方
タクトタイムは、製造工程において重要とされる標準作業の三要素に含まれる、非常に重要なものです。標準作業とは、人の動き・もの・設備の3つに焦点を当て、効率的な生産を行う作業のやり方を指します。具体的にはこの3つがもっとも効率よく組み合わさる作業の流れを探し、良いものを早く・安全に、無駄なく作ることが目標です。
この標準作業の三要素を語る上で、タクトタイムはなくてはならない存在なのです。
標準作業の三要素
標準作業は、人の動き中心として考えます。狙いは製造におけるルールの明確化と、改善ツールとしての側面があります。製品を作る上で発生する、人による作業方法や管理方法の違いを統一するとともに、正常な流れと異常な流れを判別するために実行されるものです。
この標準作業を成す三要素とは、タクトタイム・作業順序・標準手待ちの3つを指しています。ひとつずつ解説します。
タクトタイム
製品1個を何秒で生産するかを表す時間のことです。対象となる「標準作業」のサイクルタイムにタクトタイムを近づけていくことが目的です。まずは人・もの・設備の標準作業を設定、つまり効率の良い組み合わせを設定します。決定後、生産のサイクルタイムがタクトタイム以内になるよう、各作業者・各工程の「標準作業」を設定。実際に稼働してみた上で得られた情報をもとに、作業の改善などを検討するのです。
理想はサイクルタイムとタクトタイムが同じになることですが、作業工程のなかには外注やサイクル外のことも入ってくるため、同じ時間に収めることはほぼ不可能です。そのため、できる限りサイクルタイムとタクトタイムを近づけていくことが重要になります。
作業順序
作業順序とは、その名のとおり作業者がもっとも効率よく良いものを生産できる順序のことです。具体的にはものを運ぶ、機械への取り付けを行う、加工・組み立ての作業を効率よく行うための順序を指します。
作業順序を考える時点でもっとも最適な順序が決まっていることと、誰が行っても同じ作業が可能になるような順序になっていることが重要です。逆に言えば、特定の作業員しか効率よく作業ができていない状態では、作業順序が設定できていないということになります。優先順位としてはあくまでも作業順序を決めるのが先であるため、もっとも効率よく良いものを生産できるか、誰が作業しても同じ品質で、同じ要領で生産できるかを検討するべきです。
標準手持ち
タクトタイムとサイクルタイムが製品生産に与える影響
タクトタイムとサイクルタイムは製品生産に大きな影響を与えます。もう一度、それぞれの意味を理解しておきましょう。
- タクトタイム:オーダー数量をこなすのに1個あたり何秒かかるか
- サイクルタイム:自社の生産設備の標準能力
両者が示すものはまったくの別物です。しかし、双方の関係が製品生産に与える影響は大きく、どちらかをおろそかにすることはできません。バランスを意識しなければ、無駄な生産をし続けてしまうことになるのです。
タクトタイムとサイクルタイムが等しい場合
タクトタイムとサイクルタイムが等しいときは、オーダー数量と自社の生産設備のバランスがとれている証拠です。生産における理想的な状態で、無駄な生産が発生しない形となります。
ただ、現実問題としてタクトタイムとサイクルタイムを等しくすることは、不可能と言っても過言ではありません。生産工程においてすべて自社で行っている場合であっても、生産サイクルには含まれない工程があれば、その時点でサイクルタイムのほうが長くなってしまいます。また、一部工程を外注している場合も同様です。
そのため、タクトタイムとサイクルタイムを等しくするのではなく、双方が五分五分に近づくようにする努力が大切です。
タクトタイムがサイクルタイムより短い場合
タクトタイムがサイクルタイムより短い場合、オーダー数量に対して製造が追いついていない状態です。この状態が続くと欠品が生じることとなり、顧客の注文に応えられなくなってしまいます。
この場合、問題は標準作業の三要素のどこかに問題がある証拠です。タクトタイムなのか作業順序なのか、それとも標準手持ちなのかを洗い出し、サイクルタイムとタクトタイムの差を短縮する必要があります。
タクトタイムがサイクルタイムより長い場合
タクトタイムがサイクルタイムより長い場合、オーダー数量よりも多く生産できている証拠です。一見すると良い状態にも見えますが、この状態が続くと過剰な製造に転じてしまい、在庫が発生する原因となります。
この場合は標準手持ちの見直しが必要です。最低限の標準手持ち数を見直し、量を増減させながら、タクトタイムとサイクルタイムのバランスをとっていきます。標準作業を運用する目的は、あくまでも良いものを無駄なく生産することであるため、生産が早ければ良いという問題ではないことを忘れてはいけません。