2021.01.08
チョコ停とは?ドカ停との違い、対策と改善方法、記録や時間計算の仕方を解説
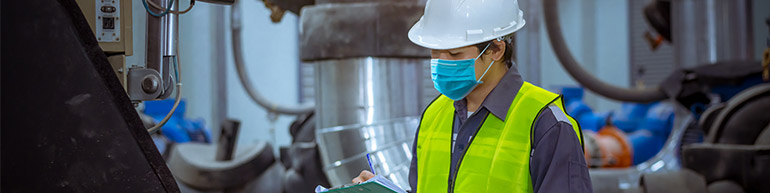
塵も積もれば山となり、工場の稼働率や経営に影響を与える可能性を秘めた「チョコ停」。ここでは「ドカ停」との違いや記録・計算方法、チョコ停が工場に与える影響や対策まで詳しくご紹介します。
チョコ停とは?定義・意味
チョコ停とは、「工場内で何らかのトラブルが発生し数分から数十分レベルでの生産停止」のことをチョコ停といいます。チョコ停の要因となるトラブルの例としては、「取り付ける部品を落としてしまい代わりの部品を準備する」や、「生産材料や生産部品が手元に何らかの理由で届いていない(もうすぐ届くことは分かっている)」などが考えられます。生産停止時間が短いため、ドカ停に比べると優先順位を下げられる傾向がありますが、「塵も積もれば山となる」状態で対処を怠ると大きな損害につながる可能性を秘めているのがチョコ停です。
チョコ停率とは?計算方法
チョコ停率とは、生産設備の稼働時間のうち、チョコ停した時間の割合のことをいいます。
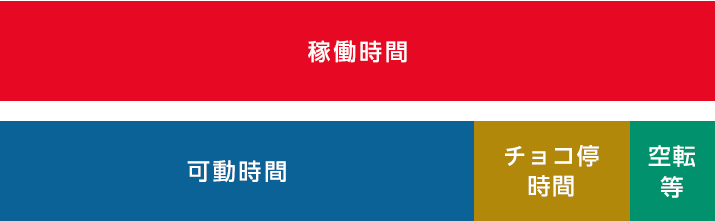
上記のように、稼働時間を可動時間とチョコ停時間と空転等の時間の合計とした時、チョコ停率は下記の計算式で計算できます。
<チョコ停率の計算式・計算方法>
稼動時間=可動時間+チョコ停時+空転等の時間
チョコ停率 = (チョコ停時間/稼動時間)×100
チョコ停とドカ停の違い
ドカ停とは?
ドカ停とは、「すぐに対処できない要因」により、長時間にわたる生産停止のことをドカ停といいます。ドカ停の要因例としては、「生産材料・部品が手元になく入手できるまで時間がかかる」などです。
チョコ停とドカ停の違い
チョコ停とドカ停の違いは、「直ぐに対処できるかどうか」、「対処に時間がかかるかどうか」で異なります。ただし、「この時間止まっていたからチョコ停」や「この時間以上の停止の場合はドカ停」というような基準があるというわけではありません。
チョコ停が工場に与える影響
チョコ停は、ドカ停に比べると時間が短いため工場に与える影響も大きくありません。しかし、塵も積もれば山となるで、積み重なることで大きな影響を与える可能性があります。
影響1:納品期限・遅延の影響
チョコ停の数が多くなると生産性が低下し、納期が守れない、遅延が発生するといったことにつながります。そのためどんな細かいチョコ停でも放置しておくのは非常に危険です。
影響2:品質の低下
チョコ停が発生すると、生産物の品質低下につながることがあります。例えば、人作業などでは、生産の流れが途切れてしまい、リズムがくずれて品質が落ちることがあります。集中力が途絶えてしまうといったことが要因になります。
さらに、生産設備の場合でも、チョコ停が発生すると品質低下を招くことがあります。チョコ停が発生後、生産を再開するには、「再開プロセス」がありマニュアル化されていることが多いです。その再開プロセスで人為的なミスが発生し、品質低下につながることがあります。
影響3:対処の工数がかかる
影響1と同様ですが、チョコ停の数が多くなるとその対処に工数(時間)を取られてしまいます。その結果、残業増加などにつながる可能性もあります。
チョコ停の記録表
チョコ停の記録表とは、チョコ停が発生したらその内容を記録しておく資料のことです。主に、チョコ停の発生日付や時間、チョコ停の理由、その対処方法、対処者名を記録します。
チョコ停の記録表の目的は、工場内での情報共有や申し送りのために記録します。さらにチョコ停の記録表を参考にチョコ停削減の改善策を検討したりすることもあります。
チョコ停の対策・改善策
対策・改善策1「記録表をしっかりつけて現実を把握する」
チョコ停の対策・改善策では、しっかり現実を把握することが最重要です。つまり、いつ、どういう理由でチョコ停が発生し、どう対処したのか?を細かく把握すること(チョコ停の記録表をしっかりつけること)です。チョコ停は細かいためいちいち記録できないといった声も聞かれますが、チョコ停の改善・対策を具体化するには、この記録が最重要になります。現場で何が起きているのか?を正確に把握しなければ、正しい改善策を打つことはできません。
対策・改善策2「対策を打った後、効果が出ているかを確認する」
次に重要なのは、対策を打った後、効果が出ているか?を確認することです。チョコ停の記録表が少なくなればなるほど、チョコ停は削減されていることになります。記録して対処すれば終わりではありません。チョコ停の数が減っているかどうか?までしっかり確認して、初めて「改善策」と言えます。
チョコ停を記録することや改善することは、人が動く以上、時間とお金がかかります。そのため、どうしてもドカ停が優先されがちです。しかし、放置すると工場の稼動に大きな影響を与えかねません。面倒でもしっかり記録して改善することが重要であると言えます。
工場の見える化や予防保全・生産効率改善に関連する資料ダウンロード
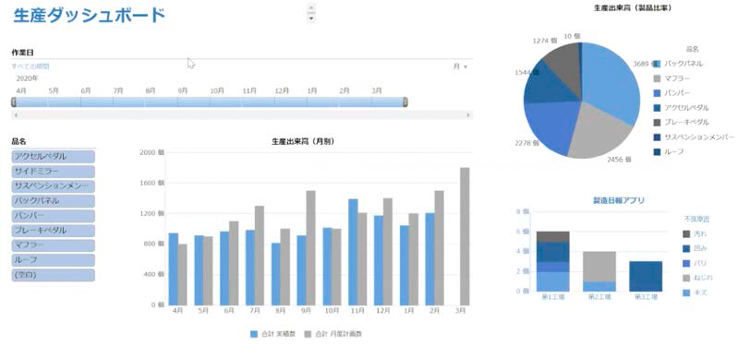
手軽に、気軽に見える化や改善を実現したい方向けの資料
- 設備保全を効率化する製造業向けkintoneテンプレートの使い方
- 製造業向けkintoneテンプレートによるチョコ停対策と可動率向上のやり方
工場や現場の見える化を本格的に検討したい方向けの資料
- 工場の見える化「3つの手順」と良品条件を決める重要ポイント
- 予防保全のメリット・デメリットとIoTを活用した場合の期待できる効果
- 稼働率の阻害要因を改善するものづくり見える化SOL概要資料
- ものづくり見える化SOLを活用した設備保全の計画の立て方・PDCAの回し方