2021.11.22
フロントローディングとは?前倒しで不具合対策をしてクレーム・リコールゼロを達成
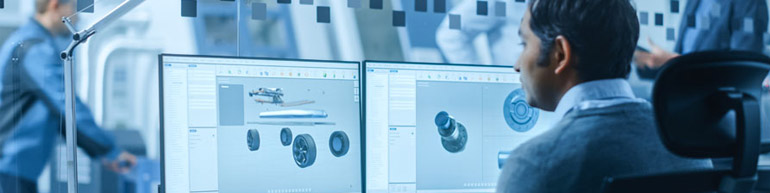
『フロントローディング(前倒し)』を行うことにより、製造分野や建築分野で設計から生産完了までの工程を効率化できるようになります。またそれだけでなく、いままで製造工程で判明した不具合などに対してはその都度修正を入れる必要がありましたが、フロントローディングによって初期段階で不具合の発生の予測ができることで対策が立てられるようになります。
このコラムでは、フロントローディングとは何か?どんな手法や活動・関連する技術があるのか、そのメリット・デメリットのほか、実施に効果的なツール・システムまで解説します。
フロントローディングとは
『フロントローディング』とは前倒しできる作業工程を初期段階で行うことで、生産効率と品質の向上を図ることを言います。従来の場合、不具合が製造中に発生した時はその段階で修正を入れていました。そのため、不具合を修正するために製造ラインをストップしたり、金型や設備を修正したりすることが必要になり、コストがたくさんかかるという問題が常にありました。
ですがフロントローディング活動を行うことによって、発生する可能性のある不具合を初期段階で予測できるため、設計段階で対策が可能になり、修正によるコストを大幅に減少させることが可能になります。
つまりフロントローディングを行うことで、量産立ち上げの前に品質のつくり込みと検証を行い、試作後の手戻りを防ぐことができるようになったのです。
また、フロントローディングで強化する施策には、以下のような活動が存在するので、自社の商品・工程・作業効率などをもとにどの活動に力を入れるのが理想か検討してみてください。
- DR(デザインレビュー)
- 検図
- コンカレントエンジニアリング
DR(デザインレビュー)
DR(デザインレビュー)とは、製造工程に携わる各部門の担当者が集まり、設計の段階で『どんな不具合が出る可能性があるか?』『どうすれば効率的な製造ができる設計になるか?』などを話し合うことで効率化を図る方法です。
DRを行うことによって、設計者の意図を下流工程へ認知してもらえるだけでなく、製造時の懸念点やそれに対する対策案について議論しあうことができます。これにより、製造の効率化を図るとともに、製品の質を高めていくことが可能です。
しかし理想とは裏腹に、DRは議論の場であるにもかかわらず、設計者の一方的な説明で終わってしまったり、形だけの会議で終わってしまったりすることの方が多いという問題があります。そのため、DR行う意味は『製品の不具合をなくし、効率性を高めること』であるのを忘れずに会議を取りまとめられる人物を中心に実施するのが意味のあるDRにするコツです。
コンカレントエンジニアリング
コンカレントエンジニアリングとは、製品開発において複数のプロセスを同時に並行して進めることを言います。
DRは構想設計・詳細設計・生産準備・生産といった各段階で審議会をして、検討が不十分な設計情報を後ろの工程へ流さないようにする活動ですが、コンカレントエンジニアリングでは初期段階から設計と生産準備を並行して進めるので、開発スピードを大幅に向上できるうえに最小限のコストで生産まで進めることができます。
また、コンカレントエンジニアリングで特に注目すべき点は『改善スピードが早い』ことです。3次元CADデータを設計、生産準備、調達、生産、物流、品質管理などの関係者全員で共有し、生産準備をしながら問題点や改善点があった場合、並行して設計の見直しを進めることができるので、常に理想とする生産体制・品質を追い求めることができる方法となっています。
検図
検図とはその名の通り、図面を検査することを言います。検図では図面が完成後に『品質・コスト・期日・特許』の4つのポイントをチェックすることで、製品の品質確保と技術の保護を図ることが可能です。
検図において品質の確保は重要な項目の一つですが、品質だけに固執せずに図面から『コストはどれくらい想定する必要があるのか?』『期日を確実に守れる生産性を見込めるのか?』を読み取り予測して質の高い図面に仕上げる必要があります。
現在の日本の企業で行われている検図は、『品質』の部分にしか注力していない企業が多く、コストや期日まで配慮した図面を作ることに力を注ぎ込めていないのが現状です。品質にしか注力できていない企業は以下の5点しかチェックできていないという特徴があります。
- JIS製図法に沿って作図されているか否か
- 誤記の有無
- 寸法抜けの有無
- 最適な公差が記入されている否か
- 加工できるか否か
このように品質のことをチェックしただけで検図を完了してしまうので、生産コストや期日について考慮しきれておらず、結果として後から修正が入る可能性が高くなってしまいます。そのため、検図は『納品まで』を意識して行うことが重要になります。
フロントローディングのメリット
フロントローディング活動では前倒し可能な工程を初期段階で行うため、以下のようなメリットがあります。
【フロントローディングのメリット】
- 設計と現場の認識ギャップを埋められる
- 製品の品質が上がる
- 全体を通してコストの削減が可能
大きい企業になればなるほど、設計課・営業課・製造課のそれぞれの関係性が薄くなりやすいので、お互いに責任転嫁してしまうような関係性に陥りやすいです。これでは良い製品も作れませんし効率の悪い会議ばかり増えて企業の発展に繋がりません。
そこで、フロントローディングを取り入れることでそういった問題点も解決できるので、関係性・品質・コストについて1つでも悩みをお持ちの企業であればフロントローディングを取り入れる検討をしてみてください。
設計と現場の認識ギャップを埋められる
DRやコンカレントエンジニアリングを行うことで、上流工程(設計・企画)と下流工程(製造現場)の担当者が議論する場が設けられるので、お互いの情報を共有することができます。
それにより、一方的な見解を押し付けあうことなく製品を立ち上げていくことができるうえに、懸念点などのシェアもできるのでその製品に対する認識を統一していくことが可能です。各部門の担当が、自身の部門のことだけでなく、他の部門の知識や技術を知ることで企業全体の能力の底上げが図れることもまた大きなメリットとして挙げられます。
製品の品質が上がる
DRや検図を行うことは品質の向上に繋がります。
なぜなら、不具合の発生を防ぐことで『不具合が減る=良品の数が増える』という構図が出来上がり、連鎖的に品質が向上するからです。また、フロントローディングの特徴として『各部門の意見を多く取り入れることが出来る』という点があり、他部門の意見を取り入れることで設計部門だけでは思いつかないような不具合対策案をもとに設計することが出来ます。
注意点として、品質の向上は良いことに変わりありませんが、あまりにも品質が良すぎると現場の検査工程に負担が増える可能性があるので気を付けなくてはなりません。なので、許容できる品質限度の取り交わしも合わせて議論しておく必要があるでしょう。
全体を通してコストの削減が可能
生産が開始してから修正が必要になると、生産ラインの停止による損失や形状変更の費用がかかるので負担が大きくなってしまいます。
ですが、フロントローディングで初期段階の議論によって、技術的な問題点やコストの問題を事前に発見・改善し、図面に盛り込むことで、後工程での修正の可能性が減少してコストを削減することが可能です。
また、問題点の対策をしておくことで生産前に行う試作の回数も最低限に抑えることが可能になり、試作にかかる費用を削減することもできます。
フロントローディングのデメリット
フロントローディングは品質の向上・コストの削減といったメリットがある反面、以下のような注意すべきデメリットもあります。
【フロントローディングのデメリット】
- 設計者の負担が大きくなる
- 各部門の協力が得られないと進まない
各部門全体で議論をするので、全員が品質の向上・生産効率のUPという目標に向かって対策案を考えないと質の高い対策案が出ません。また、それだけでなくフロントローディングは初期段階に工程を前倒しするので設計部門に負担が偏りやすいです。
そのため、全部門が協力し合ってデメリットがあることを意識してフロントローディングを進める必要があります。
設計者の負担が大きくなる
フロントローディングでは他部門を巻き込み製品の開発・製造についての議論を積み重ねるので効率や質を向上させられるメリットがあります。しかし、結果的に効率や質を向上させるための案が採用されたら、それらの作業の負担を一番受けるのは設計部門の人たちになります。
初期段階の作業の大部分は設計に集中してしまう上に、見直しや再設計の回数が増えるとさらに負担が増えてしまいます。そこで、企業としてはフロントローディングをうまく機能させるためにも、設計者の負担をなるべく軽くしてあげられるように以下のような改善策を練ることが必要です。
- 担当設計者の人数を増やす
- 案件数を減らすなど数量のコントロールをする
- 案件に対する適切な担当者を選定することで再設計の可能性を減らす
- 全てを統括できる人材を配置する
- デジタルトランスフォーメーション(DX)の導入をする
人材を用いて負担を減らすのか、技術を駆使して負担を減らすのか、企業によって適した方法は異なりますが、基本として案件着手前に負担を軽減するためにどうするべきか全体で話し合っておくことは、その後の生産性を上げるためにも必要なことです。
各部門の協力が得られないと進まない
フロントローディングでは製造に関わる部門の担当者全員で、情報の提供・共有をして生産性・品質の向上について議論します。そのため、各部門の協力無しではフロントローディングを行うことが出来ません。
そこで、企業としては以下のような対策を取り、各部門が協力しあえる環境を作ることが責務と言えます。
- 『自工程の作業だけ考える』という受け身体質を取らないように意識づけ
- 担当者全体で情報共有を行う(一部の人だけに情報が偏らないようにする)
- 再設計などによる遅れは工程全体に影響が出る事を認知させて質の高い情報共有を目指させる
- 全体を統括できる担当者を配置して各部門の担当者をまとめられるようにする
ひとつの製品に対して担当者全員が当事者意識を持つことが重要です。そのためにも、社内の人間関係を気にして人材配置をしたり、責任感のある人材配置を配置したりするのが重要となってきます。
フロントローディングの実施に効果的なツール・システム
フロントローディングでは各部門を交えた議論だけでなく、以下のようなツールを利用して実施することで、効率的にフロントローディングを進めることができます。
- CAD
- CAM
- CAE
これらのツールはそれぞれ機能が違いますが、すべて合わせると設計だけでなく製品の製造シミュレーションまで行うことが出来ます。特にCADはほとんどの製造業で使われており、取引先との情報共有においても活用できるので、利用する場面も多くあります。
CAD
CADは図面を作成するソフトで、製品設計を行う部門のほとんどで活用されています。また、CADには『2D CAD』と『3D CAD』があるのですが、最近では3D CADを使用しているところが多くなっています。
2D CADと3D CAD
2D CAD:平面のみの図面作成ができるソフト。従来の/紙で起こしていた図面をパソコンで作成できるようにしたもの。
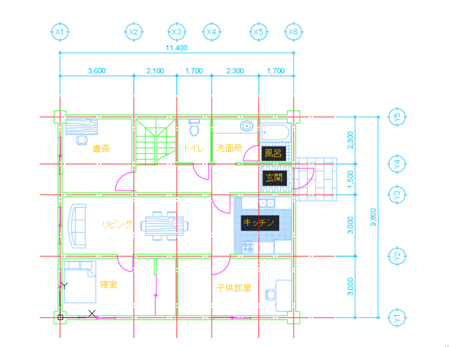
3D CAD:立体で作成することが出来る図面ソフトで『3次元CAD』とも言う。完成図がイメージしやすく2Dのように各面(上・下・側面・正面)をばらして記載する必要がなくなる。(ただしPCでしか確認できない)
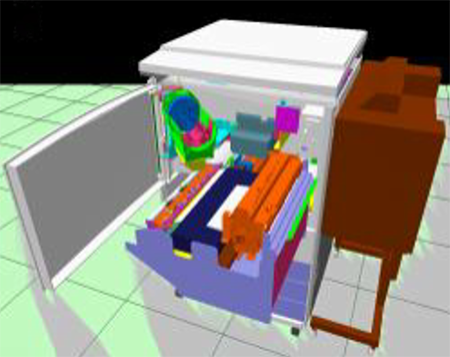
一般的に、どちらか片方のみを利用することは少なく、3D CADは企画・設計・打合せなどで、2D CADは各現場で利用されるなど、状況に合わせて使い分ける場合がほとんどになります。
フロントローディングにおいては、3D CADを用いて各部門誰でもイメージできるように図面を作成するのがおすすめです。
CAM
CAMとは、3D CADで作成した図面をもとに加工プログラムを組み、工作機械にデータとして落とし込むことでその図面通りに制作を行わせるソフトです。従来、金型を製造する業者では手作業でデータを打ち込んで金型加工を行っていましたが、CAMができたことによって打ち込む手間が大幅に減少することが可能になりました。
また、CAMではプログラムを組むだけでなく、その加工にかかる時間を概ね算出することが出来るので、設計の段階で生産工程までの予測が立てやすくなります。そのため、製造現場の担当者にとっても予定の把握がしやすくなるので、CAMの利用するメリットは大きいです。
注意点として、CAMを導入する場合は工作機械と3次元データに互換性があるように設定をする必要があるので、導入後は各企業に合わせて設定をする必要があります。
CAE
CAEとはCADで設計した3次元データをもとに、『もしそのデータで製造したらどんな製品が出来上がるか』をシミュレーションできるソフトです。これにより、フロントローディングで製品の流動解析などを行うことが出来るようになり、製品の試作回数を大幅に減少させることを可能にします。
- 力の状態・流体・熱・電磁場などの物理現象を計算可能
- 応力、温度、電磁場のように目では見えない物体内外の現象を可視化することが可能
CAEを使うことで、現物がまだない設計初期段階で、設計の根拠を確定することができます。これにより発生する可能性のある不良内容まで分析することが出来るため、設計後期の手戻りを防止することによる設計効率の向上と、実機での評価を仮想評価に置き換えることによるR&D費の抑制が可能です。
まとめ
フロントローディングは製造の工程において前倒しが可能な工程を初期段階で行うことを言います。これにより、製造途中で修正を入れる回数を減らすことができるので、コストを大幅に落とすことが可能になるだけでなく、生産効率を向上させることもできるようになります。
しかし、フロントローディングは設計部門に負担が偏りやすいので、企業が設計部門に負担がかかり過ぎないような環境構築をすることが重要です。そのためにも、部門間の関係性や人材の質・量などを把握しておくことが必要になります。
また、CAEなどの技術ソフトを利用すればフロントローディングの質を高められるので、導入コストと修正コストを比較して導入の検討をしてみてください。