半導体の微細化に伴い、「圧力ばらつき」「治具の平行度」などの製造時の圧力が半導体品質に及ぼす影響は高まりつつあります。プレスケールは半導体製造における製造データ取得・設備メンテナンス・品質検査に加えて、「CMP研磨装置の当たり具合確認」・「静電チャック/セラミックヒーター製造時の平行度確認」・「モールド装置の圧力分布確認」などの半導体製造装置や装置の関連部材などにおいても幅広く使用されております。
当ページにて半導体製造のフローに沿って使用事例をご紹介致します。下記事例以外にも様々なシーンでご使用頂いております。簡便に、コストを抑え、「面」で圧力を測定したい方は是非プレスケールをご検討下さい。
高純度のシリコンを円板状に切り出したものをシリコンウエハを呼びます。ウエハのサイズは、直径200mm/300mmが一般的です。次世代の規格として、450mmサイズの検討も始まっています。
購入したばかりのウエハには、さまざまなゴミや金属イオンが付着しているため、高純度の酸やアルカリ系の薬品を用いて、取り除きます。
半導体に使われる絶縁膜や、導電膜をウエハ上に成膜します。
レチクルを使って、ウエハ上に回路パターンを描画(転写)します。
フォトマスクやウエハに対するUV光量分布の確認。
UVスケールは「面」での測定が可能であるため、ランプの不具合などを即座に可視化することが可能。
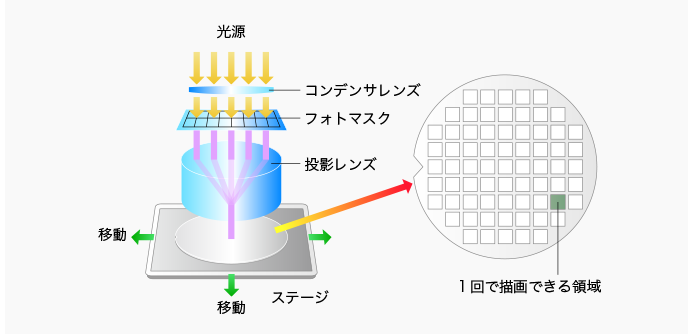
半導体の電気特性(P型、N型)を決めるリン、ボロンなどの不純物をウエハ内部に入れます。
レジストのパターンの下にある膜を残して、成膜した膜を除去します。
静電チャックやセラミックヒーターなどのセラミック製品はセラミックを積層プレスなどで押し固めて製造するが、
セラミックは粉末状であるため製造時のハンドリングが難しい。 一方で、ウエハを均一に吸着する為に
静電チャックやセラミックヒーターに対しては高い平行度が要求されるため、積層工程などにおいて
プレスケールにて圧力分布を確認し、 設備メンテナンスや品質検査を行う。
- * 画像は静電チャックのもの
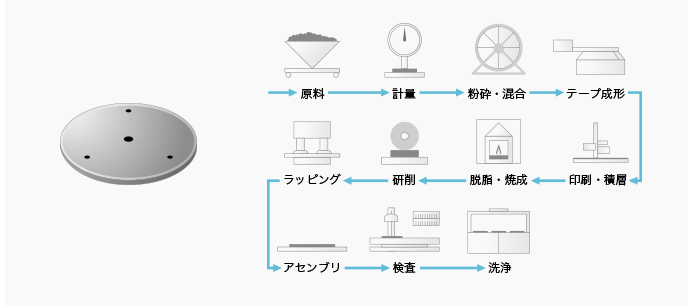
成膜工程やエッチング工程ではウエハを静電チャックに吸着させる。その際に静電チャックを通じて
ウエハが熱せられるが、吸着の均一性がウエハへの伝熱性に影響を及ぼす懸念があるため、
プレスケールでウエハと静電チャックの圧力分布を確認する。
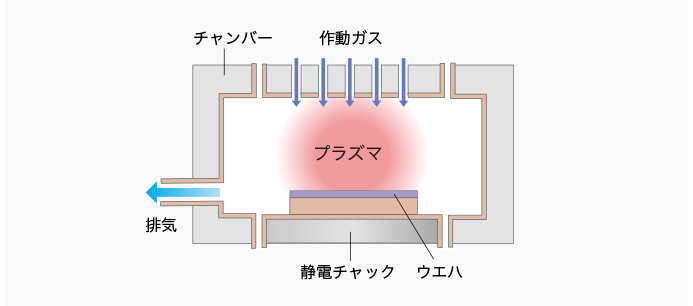
ウエハ搬送時のロボットアームのウエハに対する当たり具合またその圧力値の確認。
発生している圧力を確認し、装置メンテナンスや装置開発のためのデータ取得を行う。
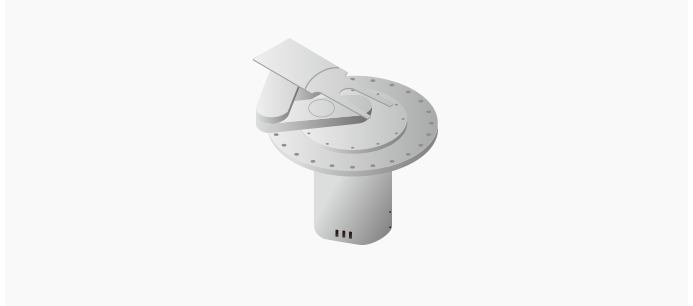
階層ごとに配線を分離する絶縁膜で覆います。
次の加工をしやすくするために、ウエハ表面を平らにします。
ウエハの研磨と圧力の相関関係のデータをプレスケールを用いて測定し、
装置メンテナンスや装置開発のためのデータ取得を行う。
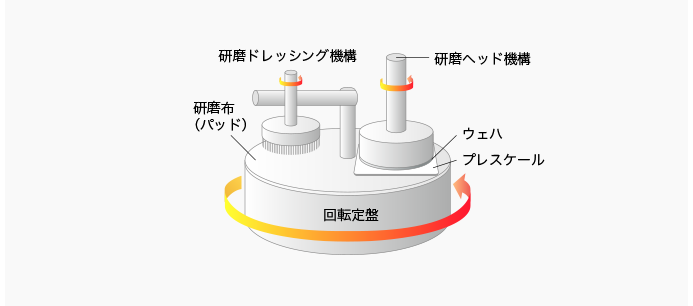
バッググラインド時にウエハの回路面を保護する表面保護テープを貼り付けます。
バッググラインドテープが適正な圧力で貼り付けられているかを確認する。
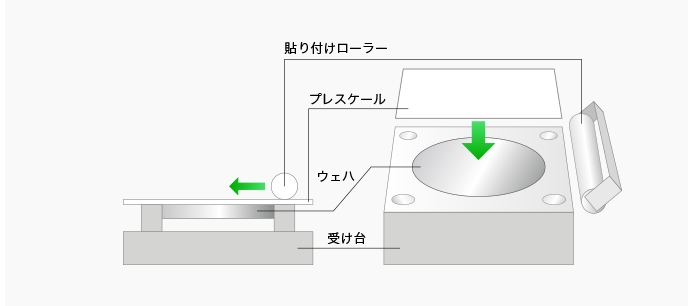
ウエハの裏側を削って、全体的に薄く仕上げます。
固定するためにウエハにテープを貼り付けます。
ウエハからチップを切り出します。
ダイシングテープに対して均一にUV光を照射しているかどうかの確認、及びその際の積算光量値の測定。
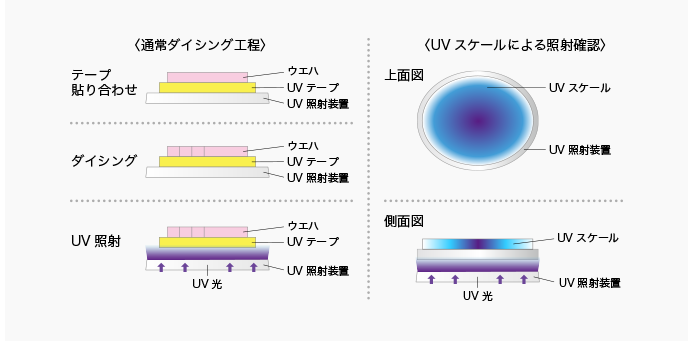
金属のリードフレームにチップを貼り付けます。
設備メンテナンスのためにウエハに対して吸着ノズルが適切に当たっているかを確認する。
装置開発のために吸着ノズルの接触圧とウエハへのダメージの相関関係データの取得する。
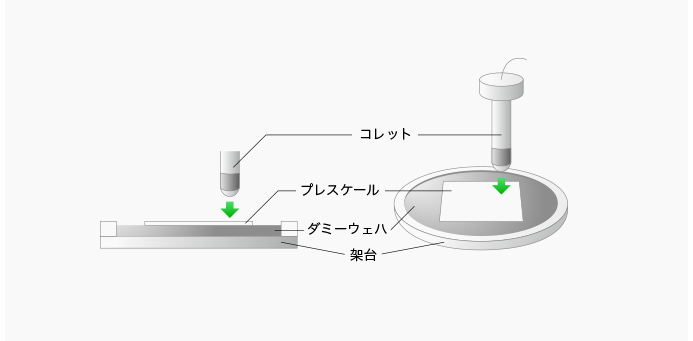
チップとリードフレームの電極を金線で接続します。
装置開発のためにリードフレームのクランプ圧データを取得する。
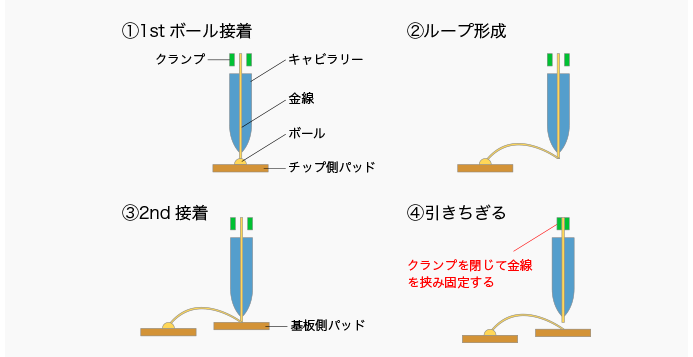
樹脂の封止材で密封します。
モールド時の圧力分布及び圧力値を測定。モールド装置出荷時の品質検査や
クライアントに対する品質検査証として使用。
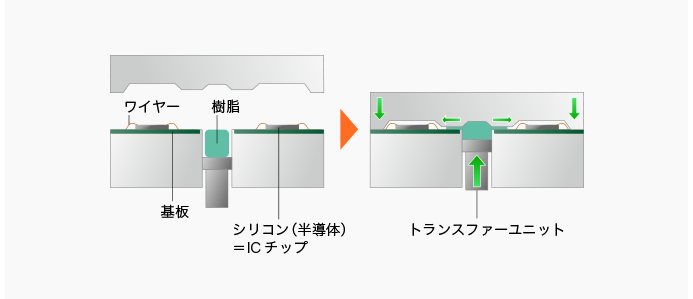
社名、製品名などを印字します。
良品を選別して梱包します。
小型化、高性能化に向けて、回路基板の上に、LSIなどの小さな部品を取りつける技術です。
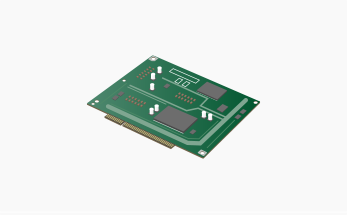
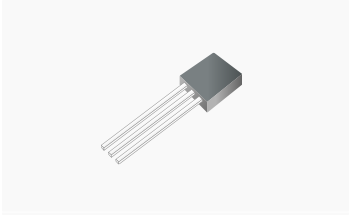
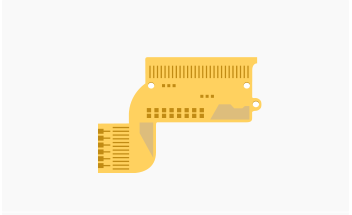
グリーンシートの積層プレス工程における面圧分布及び圧力値を測定。
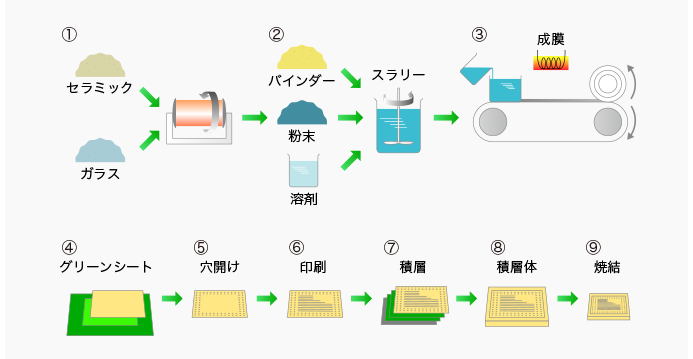
真空ラミネート機の平坦化プレスのプレス圧分布の確認。真空ラミネート機の出荷前検査・
クライアントに対する検査証、及び不具合確認として使用。
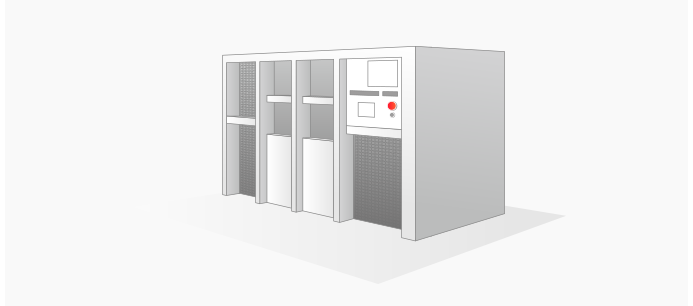
圧接型パッケージPPI(ハイパワーデバイス)の製品品質検査の1つとして、
プレスケールにて平行度を確認。
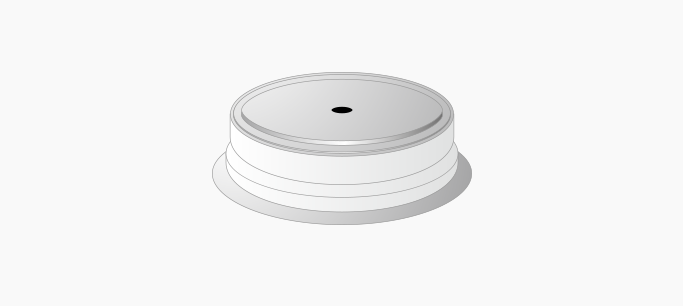
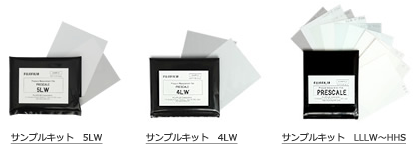