2020.07.01
予防保全とは?事後・予知保全との違い、メリット、IoT活用による効果を解説
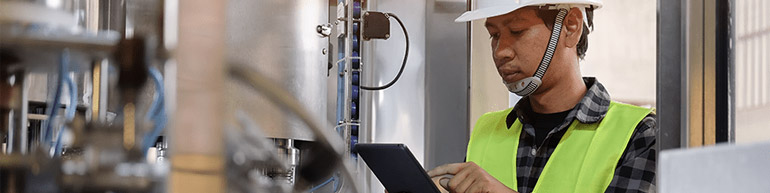
製造業の工場・生産現場では様々な設備が稼働し、様々な"もの"を生産しています。安定した高い稼働率を維持するためには、生産現場で稼働する設備の保全活動が必須です。その保全活動にも、事後保全、予防保全、予知保全といった様々な保全活動があります。ここでは、予防保全について詳しくご紹介します。
予防保全とは?
予防保全(英語:Preventive Maintenance)とは、工場の設備・機械が壊れないように事前に行う設備保全のことです。決められた期間で、決められた内容の保全業務を定期的に行い、壊れる前に事前に手を入れる、壊れないようにするのが予防保全です。自動車におきかえて説明すると、自動車は故障が発生しないように定期的にメンテナンスや車検が行われますが、これが自動車の予防保全と言えます。
予防保全の目的や実施する意味
予防保全はなぜ行う必要があるのでしょうか?それは、工場・生産現場の設備・機械を安定して継続的に稼働させ、設備や機械が壊れないようにすることです。突然、設備が故障したり停止したりすると、ものづくりの品質低下、納期遅延につながります。だからこそ、定期的に予防保全を行う意味があるのです。
事後保全との違い
事後保全とは?
事後保全(英語:Breakdown Maintenance)とは、工場・生産現場の設備・機械の「故障」「生産能力の低下」「不良品発生」などのような時に行う保全業務のことです。何かトラブルが起きてから設備を保全するので、事後保全と言われます。
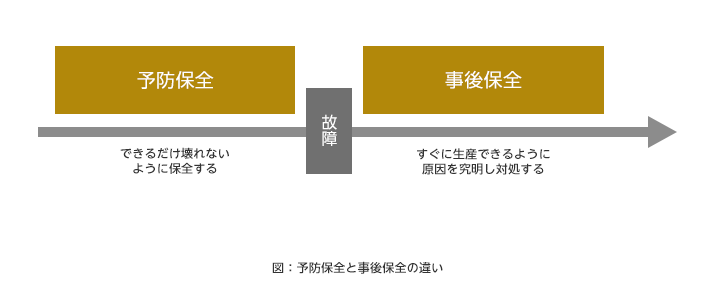
このため、予防保全との違いは、予防保全は「故障しないように事前に保全する業務」であり、事後保全は「故障したら保全する業務」となりますので、保全業務の目的やタイミングが違います。
予知保全との違い
予知保全とは?
予知保全(英語:Predictive Maintenance)とは、工場・生産現場の設備・機械の故障の兆候を事前に検知し保全することを言います。設備・機械が故障するときは、何らかの「兆候」があります。その兆候を事前にキャッチし、保全業務を行います。
予防保全と予知保全は、「故障しないようにする」「事前に保全する」という意味では、同じ保全業務です。ですが、予防保全と予知保全は、保全業務のきっかけが違います。
予防保全は「定期的に行う保全」ですので、時間がきっかけになります。しかし、予知保全は「兆候があれば保全する」ので、保全業務の「きっかけ」は「故障の兆候」になります。
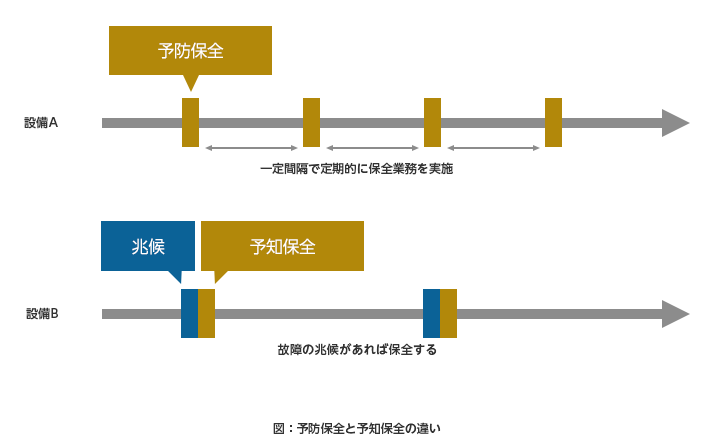
「故障の兆候」を100%確実につかむ・キャッチすることができれば、予防保全よりも部品代、人件費などを確実に削減でき、かつ、設備・機械の稼働率も向上します。
予防保全のメリット・デメリット
予防保全にはメリットとデメリットがあります。事後保全や予知保全とも比べながら、そのメリット・デメリットをご紹介します。
予防保全のメリット
生産品質の担保
設備が故障する前に部品交換などを実施しますので、製品の品質が担保できるようになります。事後保全だといつ故障するかわからないので品質担保ができません。
ダウンタイムの回避による生産性向上と物損の削減
予防保全は設備の部品を定期的に交換しますので、不良品の発生が抑えられます。そのため、作り直しといった生産性悪化を招くようなことが発生しません。
保全要員(エンジニア)のスキルアップ
事後保全だと、故障してからの対応であるため、エンジニアが作業に追われてしまい、スキルアップに繋がりません。しかし予防保全は、「故障を防ぐ」という意識が高まりますので、故障を防ぐための行動が能動的に発生し、スキルアップにつながっていきます。
保全要員(エンジニア)の働き方改革
事後保全の場合、いつ故障するかわからないため、土日、休日、夜間の保全要員(エンジニア)の呼び出しが発生しがちです。しかし、予防保全の場合は、故障が減りますので、プライベートな時間が確保できるようになります。事後保全のような急な呼び出しが減ります。
予防保全のPDCAによる工数削減
部品交換の判断基準書、交換基準書を定期的に見直しすることで、予防保全で交換する部品交換費用がどんどん削減できます。
予防保全のデメリット
事後保全や予知保全より作業工数が増える
事後保全は故障したら修理、予知保全は兆候があれば保全という作業であるため、故障や兆候が発生しない限り、作業が発生しません。しかし、予防保全は定期的に作業が発生します。
故障修理か予防かのジレンマがあり予防保全しにくい
事後保全を実施している企業は、急に予防保全を実施することが難しいです。設備が故障したら故障の修理を優先しなければならず、予防保全ができなくなります。予防保全ができないと、設備がまた故障します。そうすると、また予防保全ができなくなります。このようなジレンマが発生し、なかなか予防保全に取りかかれないことがあります。
予防保全とIoT
IoTを活用することで予防保全をより効率化することができます。予防保全でIoTを活用した時にどんな効果が期待できるのか、ご説明しましょう。
カン・コツからの脱却
予防保全をIoTを使わずに実施すると、どうしても保全業務が定性的(カンやコツ)になってしまいます。しかし、IoTを使うと、センサーデータのように情報が数値化されますので定量的な判断で予防保全ができるようになります。そのため、保全業務の属人化の脱却や知識・技術伝承などが行いやすくなります。
予防保全の集計・分析が高速化
設備日報などのデータを紙で収集していると、どうしても集計・分析に時間がかかります。IoTの場合は全て 電子化されますので、集計・分析が楽になり、予防保全のスピード・工数が大きく削減できます。
レガシー設備の予防保全も可能に
古い設備(レガシー設備)でIoTに対応していない場合でも、カメラやOCRを活用すれば設備の状態監視が可能となります。そのため、要員が見回りをしなくても、少人数で工場全体の設備の予防保全が可能になります。
設備の異常に素早く気が付く
IoTを活用しない場合は、作業員が設備を見回り、確認して異常を検知をしていました。しかし、IoTを活用すればアラートを鳴らすことですぐに異常検知ができるようになります。閾値を決め、閾値を超えるとアラートをだすというように設定しておくだけです。
予知保全へと進化
IoTで設備データを数値化・定量化し、故障データなどを蓄積していけば、故障の予兆をデータで掴めるようになります。その結果、予知保全の実現につなげることも可能です。
このように、予防保全をIoTを活用して実施すると、より効率よく効果的に予防保全が可能になります。人手不足の中、カン・コツから脱却し、安定した稼働率と品質、生産力を生み出すためには、IoTの活用は必須と言えるでしょう。
工場の見える化や予防保全・生産効率改善に関連する資料ダウンロード
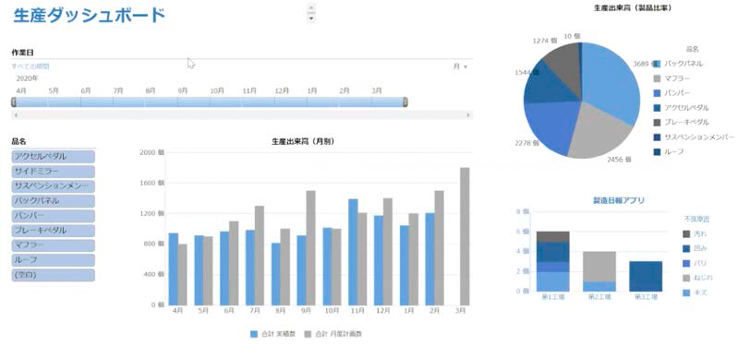
手軽に、気軽に見える化や改善を実現したい方向けの資料
- 設備保全を効率化する製造業向けkintoneテンプレートの使い方
- 製造業向けkintoneテンプレートによるチョコ停対策と可動率向上のやり方
工場や現場の見える化を本格的に検討したい方向けの資料
- 工場の見える化「3つの手順」と良品条件を決める重要ポイント
- 予防保全のメリット・デメリットとIoTを活用した場合の期待できる効果
- 稼働率の阻害要因を改善するものづくり見える化SOL概要資料
- ものづくり見える化SOLを活用した設備保全の計画の立て方・PDCAの回し方