スマートフォンやパソコン、家電、自動車など、あらゆる製品やサービスに利用される半導体。技術が日々進歩し、市場環境も目まぐるしく変化し続ける分野の最前線で、入社以来半導体材料の研究開発に携わってきた研究者がいます。最近では東アジア市場向けに多くの商品を開発。“動ける研究者”をモットーとする彼に、その意味や、東アジア市場でのチャレンジなどを語ってもらいました。
主な業務
- 半導体材料(フォトレジスト)の研究開発。
- フォトレジスト開発を通じて5Gをはじめ、現代社会のさまざまな機器やシステムを支えている。
挑戦エピソード
- よりよい製品開発のために“動ける研究者”を目指す。
- 海外顧客のコンペで2位に。諦めずに品質改善を続けた結果、逆転勝利を収める。
- 幅広い専門家がいる富士フイルムの強みを生かし、社会に貢献する。
半導体製造に欠かせないフォトレジストの研究開発に取り組む
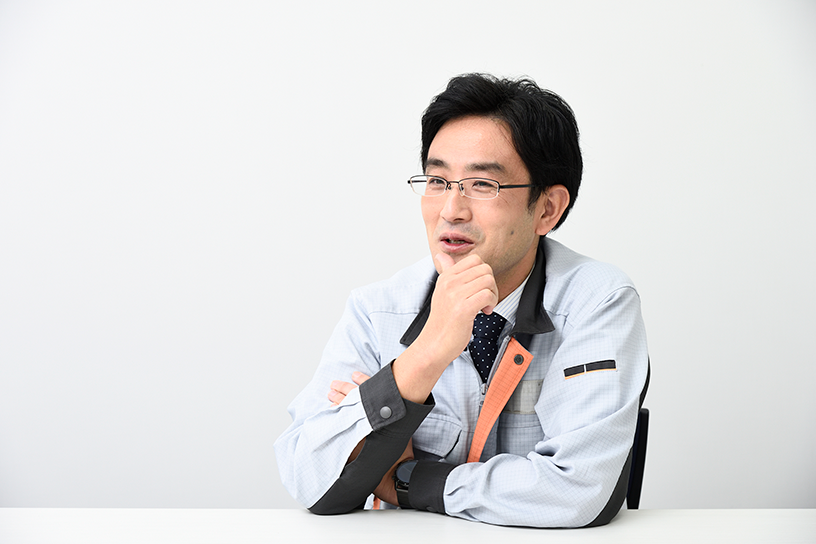
2005年に入社し、半導体材料研究所(現エレクトロニクスマテリアルズ研究所、以下EM研)へ配属となって以来17年、半導体用のフォトレジスト材料の開発に携わっています。
私たちは、メモリーやチップなどの半導体デバイスそのものを作っているわけではありませんが、その製造になくてはならない材料を開発・提供しています。半導体材料の分野では、日本企業が大きなシェアを持つ材料がいくつかあり、特にフォトレジスト*では、主要企業のほとんどが日本企業です。その意味では間接的にではありますが、富士フイルムを含む日本のメーカーが、身の回りのさまざまな製品からインフラを含む各種システムにまで不可欠な存在となった半導体の製造を支えていると言えます。
例えば5G対応のスマートフォンに採用されている半導体デバイスには、EUV*レジストと呼ばれる最先端のフォトレジストが使われています。そういう意味では5Gの発展にも関わっているとも言えますね。
フォトレジストとは?
フォトレジストとは?
光を受けて化学変化を起こす性質を持つ感光材料で、半導体に回路パターンを描くために用いられる。半導体製造に欠かせないもの。露光、現像によるパターン形成後のエッチング(酸の腐食性を利用して表面を削る加工の技法の1つ)に耐える液状の化学薬剤で、ポリマー・感光剤・溶剤を主成分とする。
半導体は土台となるウエハーに微細な素子や配線からなる回路パターンが形成されている。フォトレジストはウエハーにその回路を転写する工程で使用される。
詳しくはこちら
EUVとは?
EUVとは?
波長が極めて短い(13.5nm)、極端紫外線(extreme ultraviolet)。
デバイスの小型化・高容量化に伴って、半導体集積回路(LSI)にはさらなる高集積化が求められている。集積率を高めるためには、より細い配線を半導体内部に作る必要があり、露光光源であるレーザーの波長を短くしなければならない。そこで最先端のプロセスでは、EUVを露光光源とすることで半導体回路を微細化し、機器の高性能化・低消費電力化・低コスト化を図っている。一方で、EUVの実用化には課題も多い。
商品開発には、顧客や協業先とのコミュニケーションが不可欠
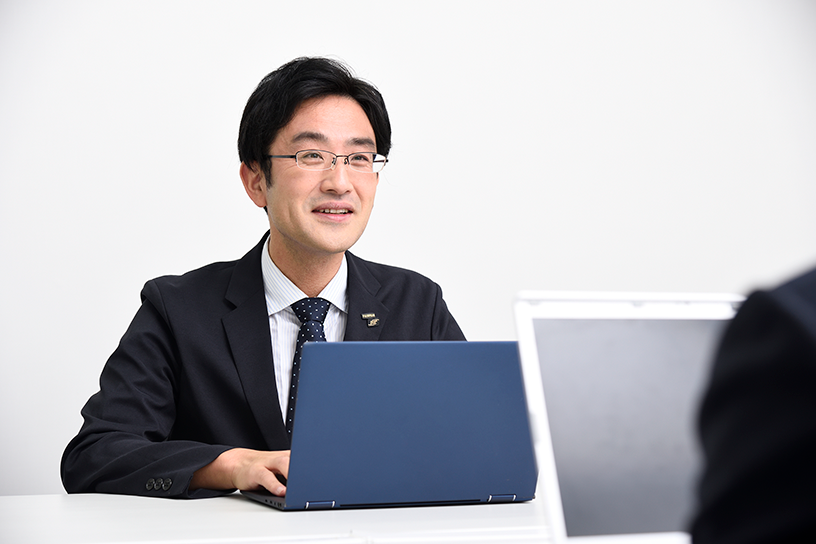
半導体の高性能化*には微細な加工が不可欠で、波長の短いレーザーが露光光源として利用されています。感光材料であるフォトレジストは、光源の種類によっていくつかに分類され、私は現在、ArF(フッ化アルゴン)エキシマレーザーとEUVレーザーの2種類に対応した商品を開発しています。波長が短いほど微細な回路パターンを描くことができ、最先端のEUVでは15nm以下の線幅が可能で、フォトレジストにもそれに対応した高いレベルの性能が求められています。
所属するEM研の、業務は基礎研究や、新しい商品を作るために原料の組み合わせや作り方を考えるだけにとどまらず、実に多岐にわたっています。特にフォトレジストは、顧客である半導体メーカー向けに一つひとつカスタマイズして開発していますので、顧客ごとに要求される性能や重視すべき性能が違います。そのため、営業と一緒に顧客へのヒアリングを重ねることや、客先のさまざまな部門とのすり合わせが重要になります。
しかも、採用されるためにはレジストだけではなく、レジストを使う基板、現像のユニット、レジストに現像液をかける装置のメーカーなど、複数の協業先とベストな組み合わせを作って提案することが多く、顧客との直接交渉はもちろん、協力会社との連携など、各方面とのコミュニケーションが欠かせません。
半導体の高性能化とは?
半導体の高性能化とは?
半導体の性能の高さは集積率の高さと言える。集積率が高いほど処理スピードが速く、小型化が可能。小型化によって、機器の低消費電力化・低コスト化にもつながる。
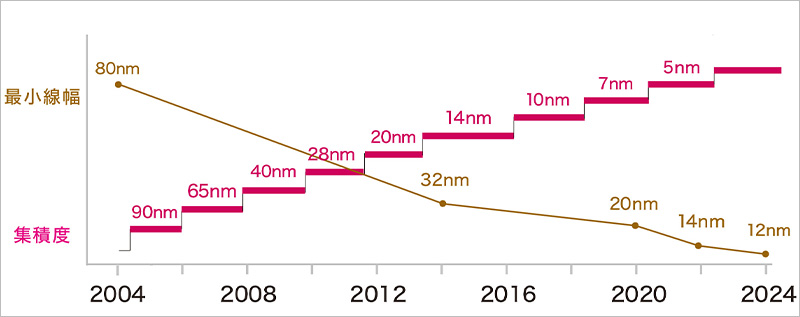
研究所にとどまらない“動ける研究者”であれ
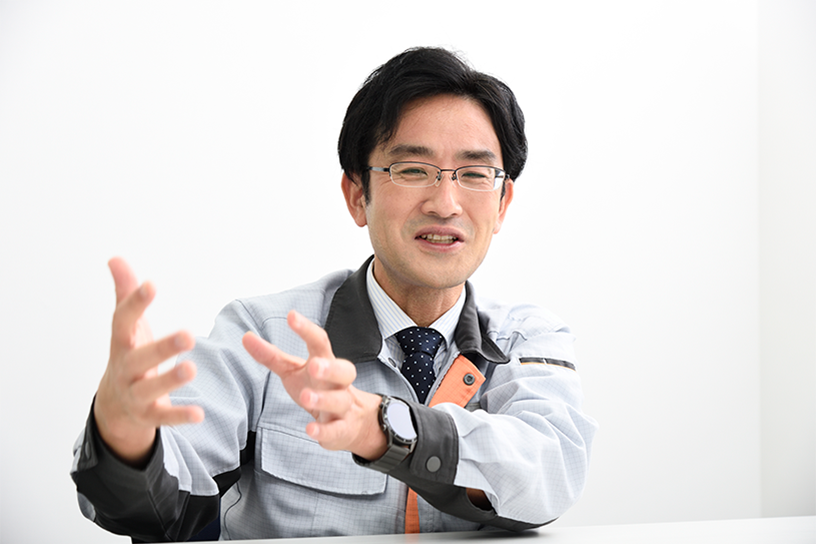
コミュニケーションは、フォトレジストの開発において非常に重要です。例えば私の仕事は、顧客のもとに伺って「どんな性能の材料を必要としているか」を確認するところから始まります。その後、ポリマーなどの化学物質の合成部門などとも協力して化学構造から設計し、試行錯誤しながらサンプルを作ります。そのサンプルを顧客にプレゼンテーションし、試用してもらってフィードバックを受け、また新たなサンプルを作る。顧客と対話を重ねてこのサイクルを何度も繰り返します。顧客に満足してもらえる性能が出たら、商品化を担う関連事業会社や工場などと協力して量産にまでこぎつけます。サンプル採用から商品化にいたるまで、1年から2年くらいかかることも当たり前です。
また、変化の激しい業界ですので、顧客の要求性能が当初の予定から変更されることも少なくありません。積極的に情報を収集して、その可能性を推測したり先読みしたりしながら、開発に落とし込むといった動きも必要になります。ある意味、“情報戦”ですね。だからこそ、開発品が採用され、商品化にまでこぎつけるためには、研究所にこもっているのではなく、積極的に“動ける研究者”でなければならないと考えています。
最近は、半導体製造を世界的に牽引している東アジアの顧客と仕事をすることが多くなっていますが、彼らからは過去の実績や失敗よりも、今と未来の可能性を重視する前向きな志向を感じています。「昔のことはいい。それより、今はほかにどんな提案ができるんだ」といった姿勢ですね。私たちも、できるだけ多くのサンプルを提案したり、新しいものを提案したり、以前と比べて意識はずいぶん変わりました。
諦めずに努力しつづけることで、チャンスを生かし逆転勝利
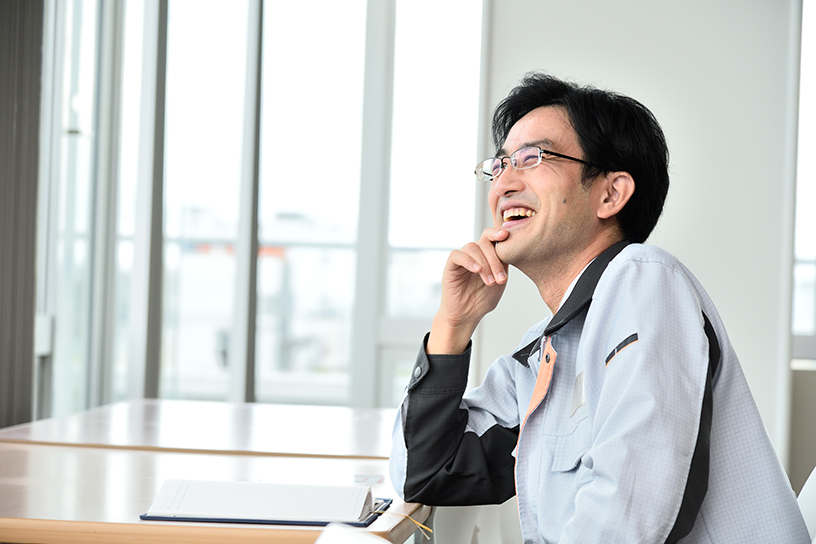
半導体業界特有の状況の流動性と私たちの粘り強さが、コンペ(受注競争)で逆転勝利を呼び込んだことがあります。そのコンペで私たちは2番手でした。普通は1番手が採用されます。しかし、私は、まだチャンスがあるのではないかと諦めませんでした。
諦めなかった最大の理由は、提案した商品に大きな自信を持っていたからです。フォトレジストは顧客の求める性能に合わせてカスタマイズする商品です。私たちはあらゆる手段で情報を集め、実際にフォトレジストが塗布される下地まで入手して品質を調整するなど、顧客の厳しい要求にこたえた最適なものを作り上げ、提案したという自信がありました。逆に1番手が提案したのは、広く使用実績のある既存材料そのものと推察されました。
また、半導体業界は流動的ですので、ちょっと先に何があるかわからないという可能性もあり、とにかく開発は継続しようと考えました。これは長年の経験から来る半ば感覚的な判断だったのかもしれません。
そこで、富士フイルムの現地法人の営業担当者などを説得して巻き込み、「どの性能が足りないのか」「レジストを塗布する条件は何か」といった情報収集を顧客に対して行い、私も仕事の合間を縫ってそれに対応できるよう品質を調整し、継続的に顧客のいろいろな部署にアピールする活動を続けました。
最終的には、顧客が当社品を追加評価してくれることとなり、顧客と一緒に条件調整した後、私たちの提案が採用となりました。諦めずに開発と提案をし続けていたからこそです。目算という意味では確たるものはなく、周囲に諦めムードが漂う中で開発を続けるのは精神的につらい部分もありましたが、基本的な顧客対応を地道に行い、結果として極めて大きな売上となる仕事につながったのは、満足のいく成果だと感じています。
日々変化する半導体業界において、チャンスをつかむためには、今回のように2番手だからといってすぐに諦めるのではなく、情報収集を継続していつでも声をかけてもらえるような状況を維持しておく戦略もあるのではないかと思いました。
富士フイルムの一員として社会課題の解決に貢献する
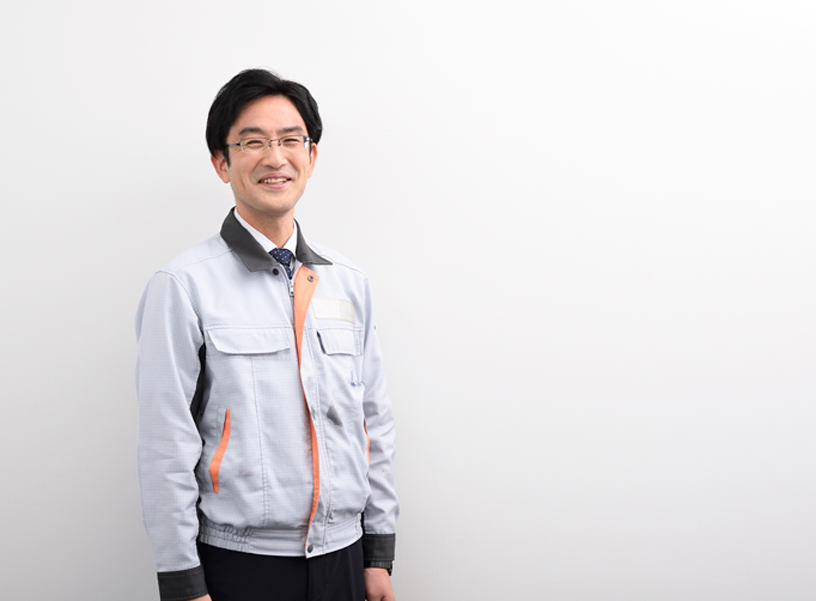
半導体材料に求められるレベルはどんどん上がり、スピード感とクオリティーが同時に必要とされています。こうした中、富士フイルムの強みは、合成や解析技術など幅広い分野の専門家がいることです。多様で豊富な知識・知見などを有効活用していくことで顧客満足度をさらに高めるとともに、デジタル機器やインフラに欠かせない半導体の高性能化を支えることで、より安全で誰もが暮らしやすい社会の実現など、社会課題の解決を目指していきたいと思っています。
EUVレジストの開発はチームで行うため、組織作りや運営にも生かせるかもしれないと考え、1年ほど前に、企業の成長戦略策定を行う国家資格である中小企業診断士の試験を受け合格しました。結果として、リーダーとしての組織のまとめ方が、感覚ではなく理論的にわかるようになり、物事のとらえ方がとても多面的になったと感じています。やればやっただけの達成感が得られるので勉強自体は苦にならないタイプですし、これからも興味のある勉強を続けていきたいと考えています。
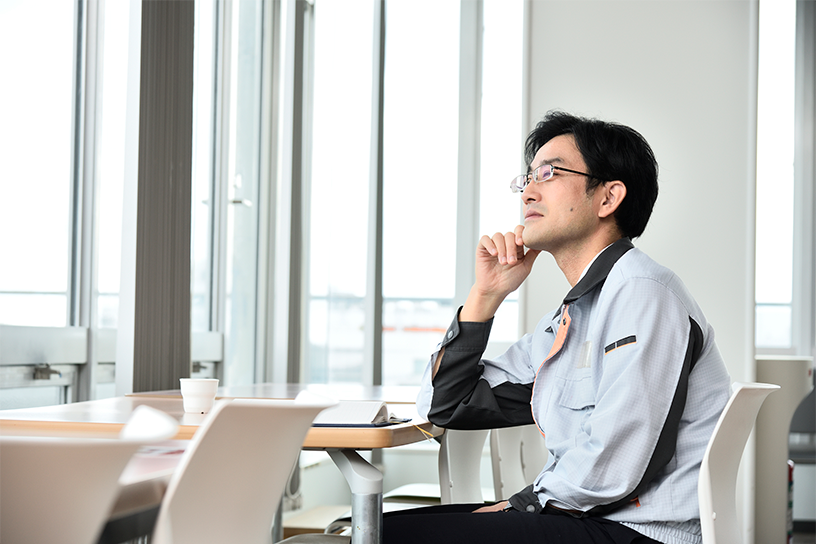
研究所は自然豊かな場所にある。食堂で窓外を眺めながらアイデアを練ることも。
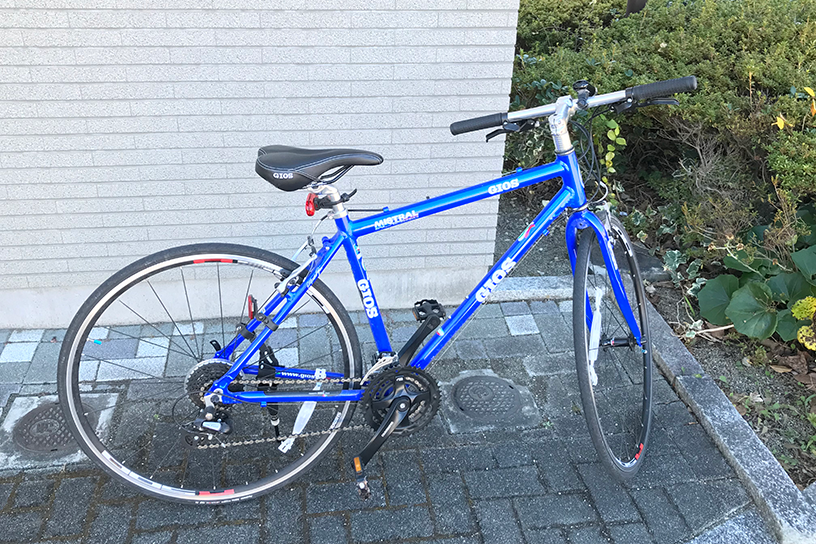
現在の事業所に配属になってから、通勤は自転車。毎日往復20kmを走るので体力がついた。“動ける研究者”にとっては体力も重要な資本。