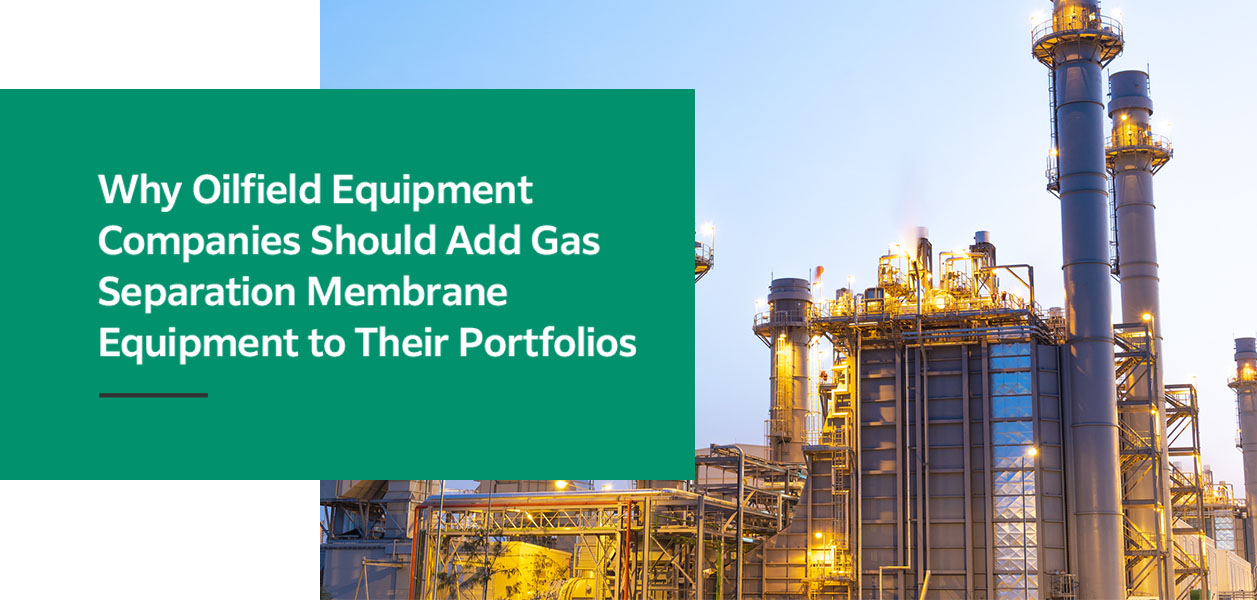
Gas separation is a necessary part of many oil and gas processes. When natural gas is first collected, it's considered "sour" because it contains carbon dioxide (CO2) and hydrogen sulfide (H2S). This sour gas can corrode pipelines and equipment, affect equipment functionality and prevent the gas from meeting regulations and standards. To remove such sour compounds, oil and gas companies "sweeten" the gas with various processes, including putting it through gas separation membranes, which make use of a thin selective polymeric layer to remove the CO2 and H2S, along with H2O.
These membranes are powerful solutions that are only becoming more popular as oil and gas companies see the benefits. Adding them to your oilfield equipment portfolio opens you up to the latest innovations in the industry, allowing your clients to reduce costs, labor demands, environmental challenges and other downsides of traditional sweetening methods. Gas separation membranes can help position you as a modern partner with solutions to target the unique demands of oil and gas companies.
Growth of the Gas Separation Membrane Market
Although there are other methods of sweetening gas, separation membranes hold particular promise. They greatly simplify the process of sweetening gas, resolving some of the most pressing issues in the industry. Some of the factors impacting the gas separation membrane industry's forecast include:
- Supply chain and labor interruptions: Other methods of gas sweetening can be resource-intensive, with the need to replenish materials, maintain complicated parts and keep the system running without power. Gas separation membranes are much simpler to install and manage. They can improve resiliency to supply chain and labor challenges.
- Increased demand: Since gas separation membranes have applications in gas sweetening, biogas purification and enhanced oil recovery, the demand for them is sizeable and growing.
- The need for improved performance: Gas separation membrane technology offers several key advantages over other methods like amine sweetening. It provides reliability, durability, safe operation, design flexibility and economic benefits, among others. Membranes offer durable materials with high permeability and selectivity while reducing costs, making them an excellent choice.
- Ecological requirements: Alternatives to gas separation membranes often use chemical methods to remove unwanted materials. Since membranes forgo these chemicals, they can limit environmental concerns, like handling and disposing of hazardous materials and managing carbon capture capabilities.
These are some of the needs that gas separation membranes meet exceptionally well. They're helping to fuel the growth of this innovative technology, which has made great strides in commercialization to meet business demands.
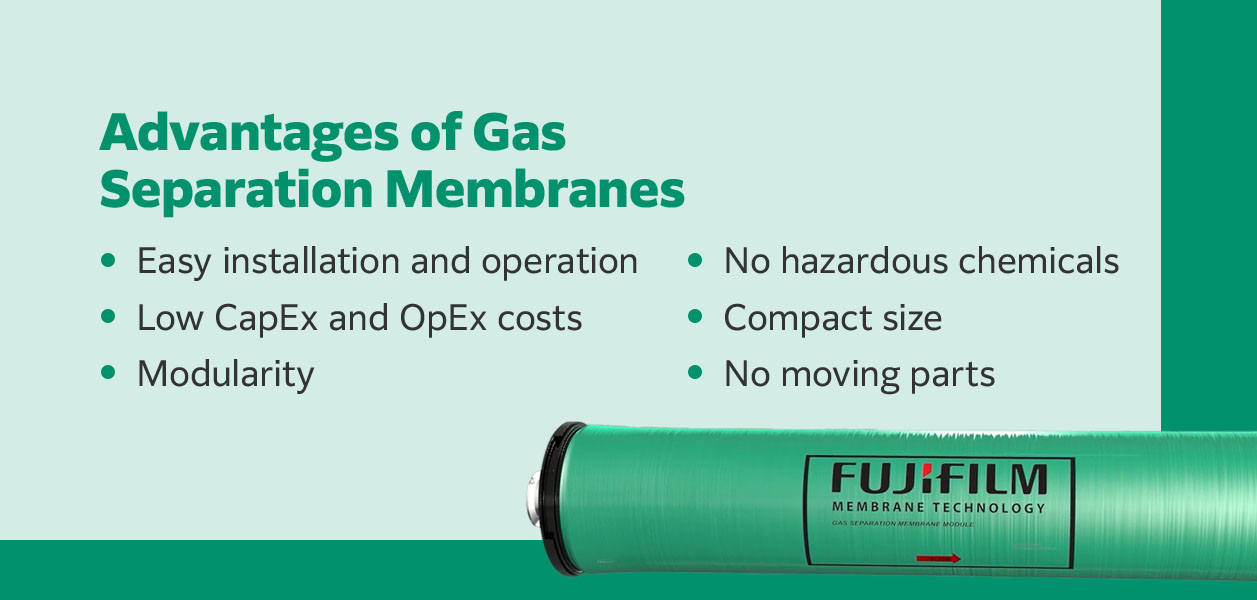
Advantages of Gas Separation Membranes
Oil and gas companies can reap many benefits from gas separation membrane technology, most of which come from its simplicity. Some reasons to sell gas separation membranes include:
- Easy installation and operation: Gas separation membranes are skid-mounted and ready to operate. They involve a much simpler installation process, reducing cost and labor. Operation also isn't labor intensive, with one-button startup and shutdown.
- Low CapEx and OpEx costs: Capital expenditures (CapEx) and operating expenditures (OpEx) are both low with gas separation membranes. CapEx is generally about 30%-40% less than comparable amine or solvent systems. With minimal maintenance, materials and operational demands, OpEx stays low, too.
- Modularity: The modular design of gas separation membranes offers more flexibility and turndown when there are changes in process conditions, such as flow rate and CO2.
- No hazardous chemicals: Without any circulating liquids, a membrane system avoids the challenges and costs associated with hazardous chemicals that can be spilled and must be disposed of.
- Compact size: A gas separation membrane system is typically 40%-60% smaller and lighter than equivalent amine units. This small size and modularity offer even greater flexibility for space requirements like offshore installations.
- No moving parts: The membrane's single-stage system eliminates moving parts that would require more operator involvement and maintenance costs. This simplicity helps to reduce OpEx costs, including maintenance costs.
Fujifilm Support
As with any gas treatment solution, proper usage and quality products from a gas separation membrane supplier are essential. Here at Fujifilm, we bring our expertise to every purchase. We can help you choose and install a system that incorporates our high-performing Apura™ membrane modules in the ideal configuration for your client's operation. We offer comprehensive technical training and installation support to help you and your clients understand a gas separation membrane system inside and out for optimal operation.
Why Gas Separation Membranes Are a Superior Alternative to Amine Sweetening
Amine gas treatment has been used for years to sweeten gas, but the benefits of gas separation typically outweigh those of amine systems. Here are some of the reasons that gas separation membranes have emerged as a strong amine alternative:
- Ease of use: Amine treatment systems are usually complex, with many moving parts and ongoing maintenance demands. They call for skilled operators and permanent placement. Since membranes are skid-mounted, they can be moved. They also have a small footprint and much simpler operation.
- Costs: As gas separation systems have become more popular and commercially available, they've become more affordable. Now, they typically have more affordable CapEx and OpEx, especially with a stable, long-lasting solution like Apura™.
- Hazardous chemicals: Amine systems rely on chemicals to sweeten the gas, contributing to risky and resource-intensive disposal and handling requirements. The membrane system operates independently on these chemicals.
- Dehydration units: The gas separation membrane dehydrates natural gas while removing CO2 and H2S, meaning there's no need for a separate dehydration unit. These units can increase cost, complexity and energy requirements, so removing them offers a much more efficient system.
- Emissions: Similarly, amine systems often come with higher emissions since they rely on processes like heaters, burners and pumps. These components can create byproducts like methane, CO2 or volatile organic compounds and release them into the environment. Without these byproducts, the membrane system can greatly reduce emissions.
- Modularity: If a client needs to make changes to an amine sweetening system, the process is usually costly and time-consuming. Because gas separation membranes have a compact size and skid-mounted design, clients can quickly and affordably modify their processes, such as increasing or decreasing flow rate, pressure, and concentration.
The outlook for gas separation membranes is particularly strong. They provide extensive flexibility and performance improvements over amine systems, making them an ideal approach for many oil and gas organizations.
Learn More About Fujifilm Gas Separation Membranes
Fujifilm is an industry leader in gas separation membranes, and we proudly offer our innovative Apura™ solution and expert support services. Apura™ stands out with resistance to contaminants like aromatics and water and offers effective gas separation with semi-permeable polymeric membranes. They deliver high permeation rates and high selectivity, with stability and durability built in.
Apura™ gas separation membranes are an excellent addition to any oilfield product portfolio, increasing the strength of your service and helping clients reap the benefits of more capable equipment. To see how Fujifilm can improve your catalog of oilfield equipment, reach out to an experienced representative today.