Company C manufactures various containers and wished to enhance the accuracy of their inspection system to be doubly sure about their product quality. On the other hand, they had a problem in that inspections were taking too long because they manufacturer many different kinds of containers in very large quantities. It was an urgent task for them to establish a system that enables more accurate and efficient inspections.
Issues
- Variations in detection accuracy occur when inspecting more than a single piece at a time.
- A tremendous number of man-hours is needed for the selection, evaluation and adjustment of the equipment when introducing a vision system.
After the introduction of "4D High Resolution" lenses
- Consistent resolution performance is realized at the center and edges of the image, which reduces recognition errors for individual pieces.
- High resolution is maintained in various shooting conditions, resulting in shorter selection, installation and adjustment times for the vision system.
Issue 1: To obtain a uniform image within the image frame
Problem 1: The edges of the image are out of focus.
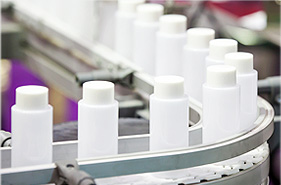
Company C initially thought that inspections could be performed efficiently by shooting many containers at once. So, they put as many products as possible within the area captured by the camera. However, the products at the edges of the image were out of focus, which prevented accurate inspection. They tried many times by adjusting the positions of the camera and light, but they could not achieve satisfactory results.
Issue 2: To enhance selection efficiency
Problem 2: The optimum lens had to be selected for each inspection item and shooting condition, which prevented them from concentrating on their core business.
Company C manufactures many kinds of containers with different sizes and designs. Therefore, the shooting conditions such as distance and aperture vary depending on the container. The shooting conditions had to be reviewed each time the container capacity is changed or a new product is introduced, which occurs frequently. But variation in the inspection results occurred every time the shooting distance or aperture was changed, which made the personnel in charge of the system extremely busy trying to identify the cause.
The keys to solving these issues were...
consistent resolution within the image frame and the best performance exercised under any conditions.
Solution: They changed to lenses that deliver consistent resolution within the image frame
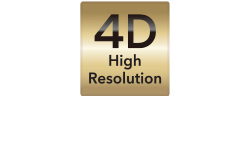
The issues Company C had to solve were inspecting many containers at once and reducing the labor required to select lenses in order to realize more accurate and efficient quality inspections. So, they consulted their system integrator, who recommended Fujifilm "4D High Resolution" lenses as the optimum lens in consideration of the many pieces to be inspected and the wide variety of shapes unique to a container manufacturer.
Solution to Issue 1: Adoption of lenses that deliver consistent resolution within the image frame
The worker at Company C was troubled because no matter what they did they could not successfully inspect as many products at once as they needed to. This problem can be solved with lenses capable of consistent resolution from the center all the way to the edges of the image frame. Generally, lenses are designed to have the best resolution at a predetermined standard shooting distance (design distance). Therefore, the edges of the image may become blurry when the distance is changed, which prevents inspection of the products at the edges. Fujifilm "4D High Resolution" lenses for machine vision cameras adopt the floating design. The lens elements are configured into front and rear groups, and only the lens elements behind the iris move to focus. This restrains the drop in resolution caused by changing shooting distances. In addition, alignment of the entire lens constructions with micrometer-level adjustments during assembly almost completely eliminates one-sided blur caused by misalignment of the lenses. The containers placed at the edges are not out of focus when as many of them are put in the shooting area as possible. As a result, Company C is now able to conduct efficient inspections.
Solution to Issue 2: Adoption of versatile lenses that deliver the best performance irrespective of shooting conditions
In inspections using a vision system, the resolution performance may be degraded when the shooting conditions such as the distance from the product and aperture are changed. This is because the optimum shooting conditions for the best performance of the lens are predetermined. For companies that manufacturer many products with a large variety of sizes and designs like Company C, it was very difficult to figure out what lens would be the most suitable for what containers. Fujifilm developed "4D High Resolution" lenses that deliver consistent resolution from the center to the edges of the image even when the shooting conditions are changed, which is a testament to Fujifilm's abundant design and manufacturing know-how as a comprehensive lens manufacturer. This has successfully eliminated the bothersome task of lens selection. As one lens is capable of inspecting a wide variety of containers, Company C has been freed from the problem of lens selection. In addition, the camera can be installed anywhere, at the top, bottom, left, right or diagonally to the product, which results in shorter system installation and adjustment times.
Machine vision camera lenses that solved the issue
"4D High Resolution" lenses
HF-XA-5M series
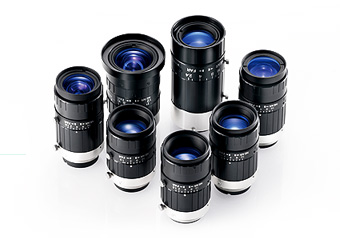
"4D High Resolution" lenses that demonstrate high resolution performance from the center to the edges are ideal for Company C, which wanted lenses that deliver consistently sharp images across the entire image frame. Shooting under any shooting conditions can be done with just one lens. Such ease of use is also what this manufacturer of a wide variety of containers wanted. The worker in charge at Company C was pleased, saying "The time required for inspection has been shortened by as much as 20%. We are now able to use that time to install new equipment and improve existing equipment." Currently, Company C uses "4D High Resolution" lenses of all focal lengths.
- * This story was arranged based on actual facts.