Our analysis technology consists of three technical field.
- “Analytical Chemistry” to clarify composition (elemental and chemical structures), distribution, and morphology with high sensitivity and precision
- “Physical Chemistry” to visualize functional sites and detect higher-order structures in materials, medicines, and devices
- Prediction of functions of materials/medicine/devices and design capability based on “theoretical calculation” technology
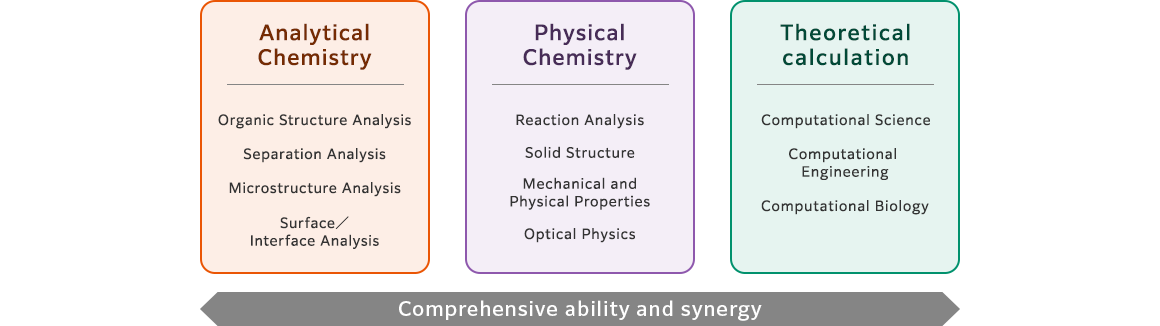
By combining the analysis, nano-dispersion, and precision coating technologies cultivated in photographic research with the high-purity polymer synthesis technology of FUJIFILM Wako Pure Chemicals, a Group company, we have developed new reference materials optimal for the innovative elemental analysis technology “fs-LA-ICP-MS method” developed recently, and improved the accuracy of quantification. (Developed jointly with Professor Takeshi Hirata of the University of Tokyo)
The thickness of the coated film of high-functional material products developed by our precision coating technology ranges from several tens of nanometers to several micrometers, so even the smallest foreign particles of 10 micrometers or less can affect the performance if mixed in. For this reason, we have established technologies to sample and analyze very small areas and to analyze products in their original form. We make full use of various techniques, and the figure below is an example.
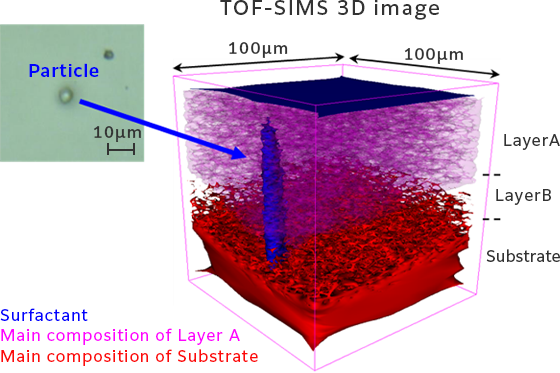
Can be analyzed by LC, GC, MALDI-MS, IR, etc. after sampling
In inkjet printing, it is important to control the size of ink droplets (dots) ejected onto paper. We have developed an on-site visualization technology using a combination of a high-speed camera, zoom lens, and illumination to capture the instantaneous phenomenon of dot formation. The information and findings obtained are being used to improve the image quality of inkjet printing.

The surface properties of the liquid-based materials, such as inks, continuously change as they dry. We have developed a novel technique to detect the mechanical properties of the liquid surface. By measuring the profile of the liquid top face at which a pointy needle comes into contact, the elastic modulus and viscosity in the vicinity of the air/liquid interface are obtained. Our method also enables to capture the dynamic change of surface properties during the drying process, which can be used to improve the image quality of printed materials and the performance of electronic and optical materials.
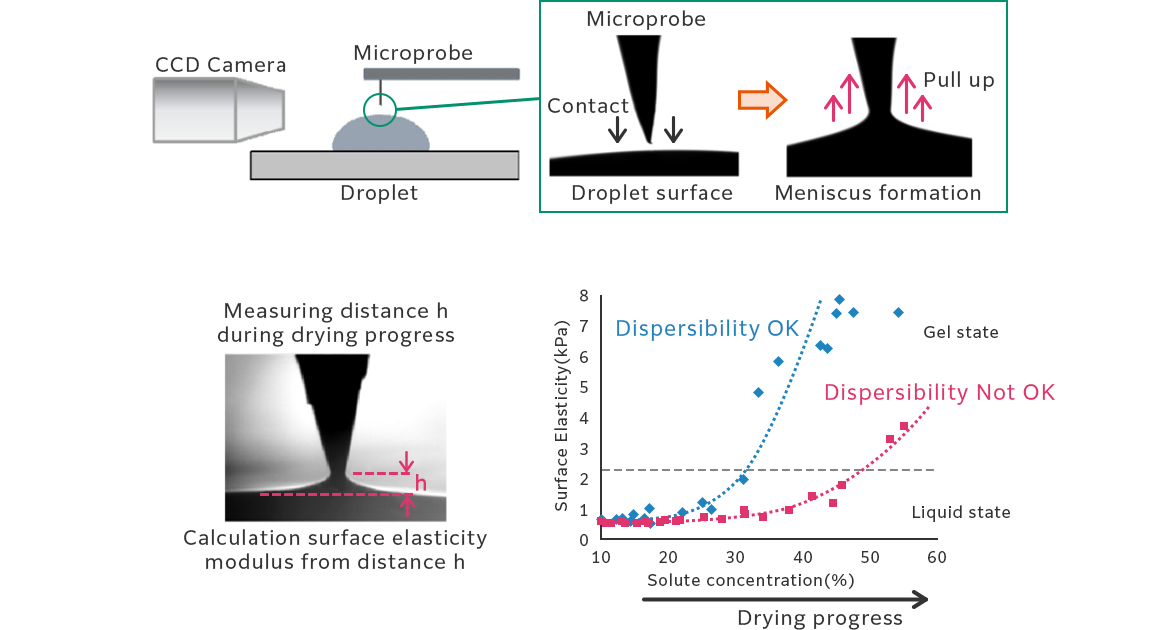
We perform large-scale calculations using not only our in-house cluster calculators but also external resources such as Fugaku (peta-scale supercomputer in Riken). In the example below, we used Fugaku to perform first-principles calculations on the Li conduction that occurs at the interface between the electrode active material and the solid electrolyte in an all-solid-state battery, and clarified the cause of the high resistance when the electrolyte is a sulfide. High-precision simulations are useful for such phenomena that are difficult to measure.
Calculated interface structure between electrode (LiCoO2) and electrolyte (Li3PS4)
We have developed “AI-AAM,” a technology for drug candidate compound search and design. “AI-AAM” is a simulation technology that calculate the binding energy between a known drug candidate compound with potential medicinal effects and a target protein based on the analysis of the interaction with amino acids, the building blocks of proteins, and automatically searches for another compound with the same binding energy and different structure as this compound by utilizing AI technology. It is also possible to design unknown compounds that could not be conceived of before.