The market for antibody drugs is expected to grow significantly because of their low side effects and high efficacy. Antibody drugs are obtained by culturing cells genetically modified to produce antibodies in a culture medium that provides nutrients for the cells and extracting (purifying) only the useful antibody drugs from the resulting culture medium.
In the past, the batch production method, in which multiple purification processes are performed sequentially after a certain period of culture in a bioreactor, has been the mainstream, but in recent years, continuous production methods, in which culture and purification are operated in parallel and antibodies are collected continuously, have attracted attention (Fig. 1).
The continuous production system is characterized by its ability to continuously expel cell wastes that accumulate in the bioreactor, thereby improving the cell culture environment and producing high-quality antibody drugs while culturing cells at higher densities and for longer periods of time. Furthermore, the continuous production of both culture and purification improves productivity and is highly effective in reducing costs. Continuous production is a new production system that combines high productivity, quality, and low cost.
- High productivity based on culturing with high density for long period
- High-quality antibodies can be obtained.
- Continuous culture and purification improves productivity, resulting in lower costs.
Figure 1, Comparison of batch and continuous production of antibody drugs
We have the continuous production MaruXTM process, which is based on five technologies: (1) ApolloXTM , our proprietary cell line with high productivity, (2) high-performance continuous culture medium (manufactured by FUJIFILM Irvine Scientific, a group company engaged in the culture medium business), (3) a culture process that supplies oxygen to high-density cells at high efficiency, (4) a membrane separation process that stably separates cells and antibodies over a long period of time, and (5) SymphonX , an automated continuous purification system developed by our company (Fig. 2). In addition to the development of scale-up technology for mass production, FUJIFILM Diosynth Biotechnologies, a group company engaged in bio-CDMO business, is introducing cGMP production equipment.
Figure 2, Our continuous production process and proprietary technologies
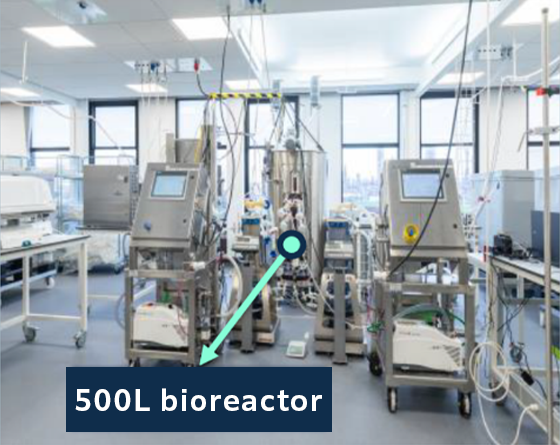
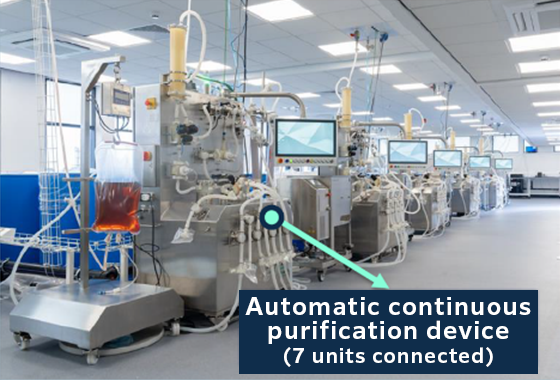
Figure 3, 500L demonstration plant