Fujifilm Inkjet Innovation is Based on Core Technology with Great Magnitude, Creating New Values for the Future
Inkjet is moving into mainstream industrial and package printing and the combined resources of the Fujifilm inkjet technology group are focused on addressing the specific challenges that these new markets pose.
To understand these challenges and the methodology that Fujifilm is employing to address them, it is useful to consider the particular needs of the industrial and package printing businesses. The range of materials being printed is vast and the range of applications is diverse, but many of the requirements are common. Viewing distances are typically short and quality expectation is high, so spatial resolution of print must also be very high. Inks must have a defined functionality such as adhesion and resistance properties in order to provide the end use properties that are demanded by the application. These are frequently tied to rigid specifications. Finally, production volumes are typically large, requiring high speed printing. It is this combination of print resolution, ink functionality and print speed that define the task for Fujifilm's inkjet technology group.
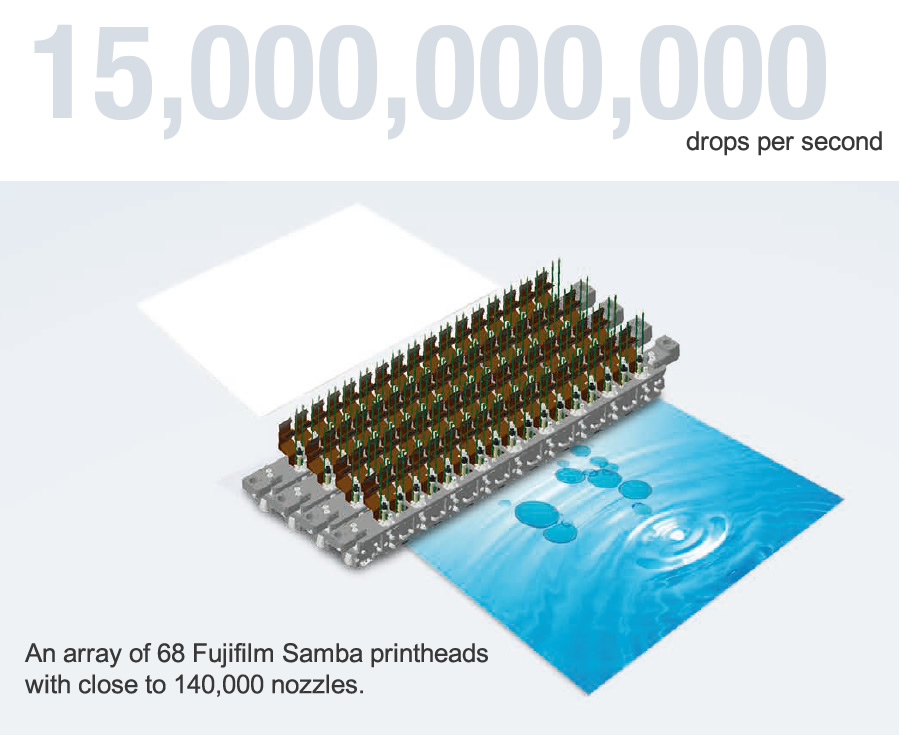
Billions of drops per second
A high speed digital printer may have to place up to 15 billion droplets of ink accurately, every second in order to form a high resolution image at production speed. Achieving this and doing so with a specially designed ink that has all of the required end use properties is a significant challenge, requiring a combination of advanced technologies in order to provide a final solution.
100 microseconds in the life of an inkjet droplet
It takes around 100 microseconds for a typical inkjet droplet to be formed, travel to the substrate, land on the surface and start forming the image.
In this time, an Olympic sprinter will run 1mm, and a Formula 1 race car will travel less than 1cm.
In the inkjet printer itself, an individual nozzle may fire up to a further 10 droplets of ink while the first droplet is still in flight. To understand the technologies needed to make this happen and how these technologies work together, it is useful to consider what is actually going on while an inkjet droplet makes its journey from nozzle plate to substrate, and to review the technology that makes all of this possible.
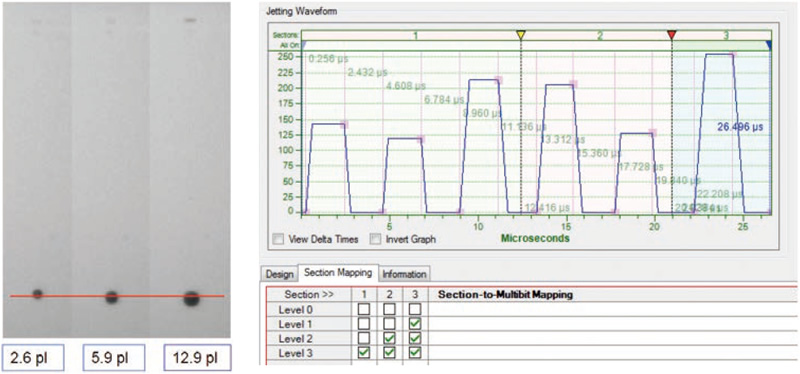
Speed of 3 different drop sizes can be tailored to land at same place on substrate.
The diagram below shows inkjet droplets in flight and details some of the characteristics of the various components that must all be tuned in order for the overall operation to be optimized. There are a great many of these properties that have to work together in order to obtain the best overall performance so it is useful to split these into three groups:
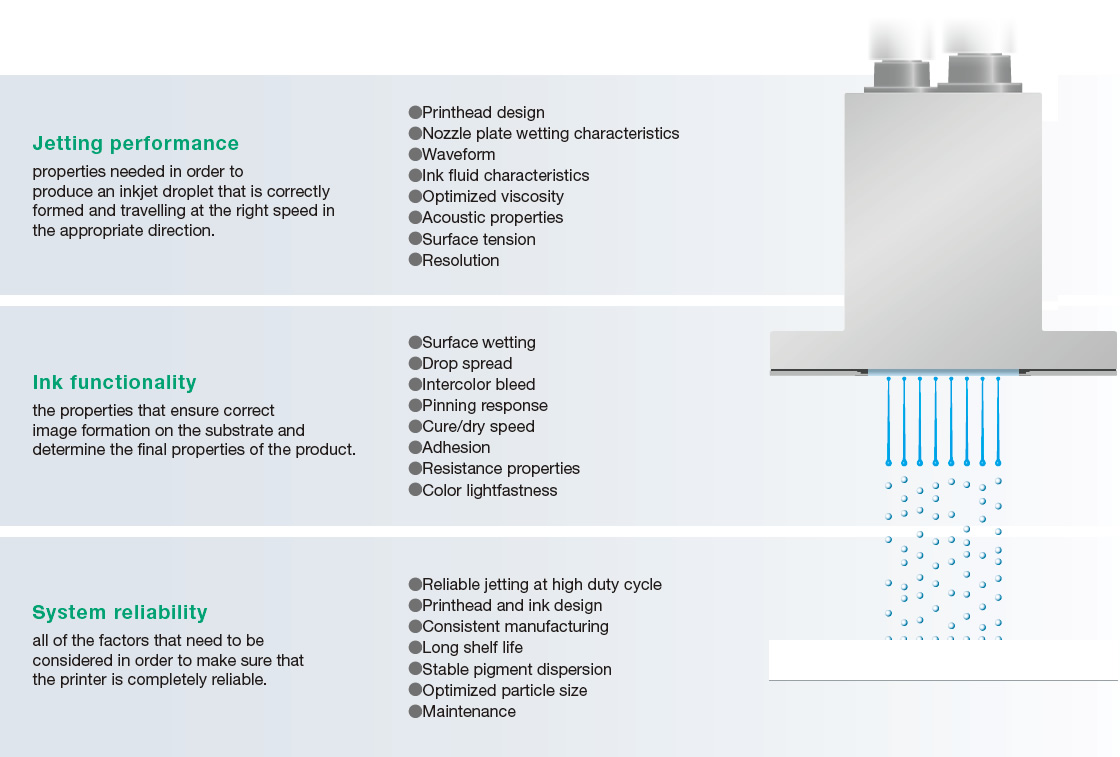