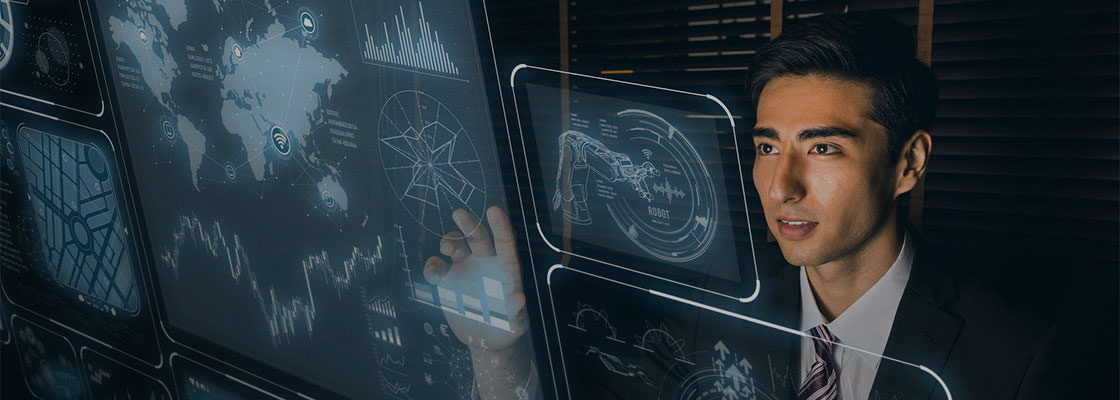
Examples of work styles established through DX
We have introduced advanced digital technologies in settings to improve business process efficiency and to share expertise. We have in doing so established diverse systems enabling our employees engaged in a broad range of jobs to collaborate with each other, demonstrating their high-level expertise.
The following example work style reforms were implemented through DX.
The work styles of salespeople and system engineers to efficiently use daily work time
Our sales-related departments have accumulated wisdom and experience through work style reforms, which they have been implementing over many years. This wisdom and experience has led to the establishment of IT and a mobile environment, which enables people to work smoothly anytime, anywhere, and with anyone, as well as systems and rules that encourage employees to work from home and go to customers' sites directly from home and return home directly. Systems for efficient and effective work have been applied not only internally but also to cross-organizational processes. They are evolving into systems that support customers' work style reforms, including the introduction of electronic contracts.
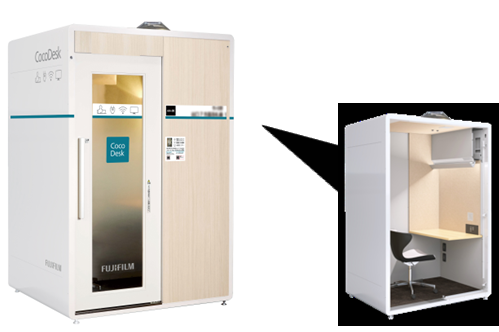
Examples of the exterior and interior of CocoDesk
Employees who contact customers, including salespeople from FUJIFILM Business Innovation Japan, our Group company, use satellite offices set up all over Japan and the CocoDesk* personal workspaces provided in stations and other places to reduce unnecessary travel. Customers are able to observe the flexible work styles of salespeople and engineers in places including the company's Toyosu Center Office in Tokyo, which is virtually connected to its bases across Japan.
- *CocoDesk: personal workspaces we provide in stations and towns in Japan.
Style of maintenance services that has evolved using ICT
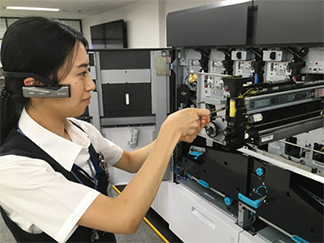
A CE performing maintenance work while receiving remote support from an engineering specialist via a wearable device
Customer engineers (CEs), who maintain multifunction devices and printers have changed their work styles using big data collected through remote services. Specifically, we have introduced the automatic remote diagnosis of the operational status of customers' equipment, which is conducted every day. We have thus replaced the previous style of maintenance services, which featured CEs' regular visits to customers to inspect equipment, with a style in which they visit customers only when a visit is deemed necessary as a result of a diagnosis. This permits CEs to understand the detailed condition of equipment and identify necessary work and parts in advance. As a result, the accuracy and efficiency of their maintenance work has improved significantly.
In the domain of commercial production printers, where a high level of skills and knowledge are necessary for maintenance, we use wearable devices all over Japan as a system for immediately sharing the expertise of engineering specialists. When highly difficult work is performed at a customer's site, the CE visiting the site shares video and audio information about the equipment with an engineering specialist in the back office. This permits the engineering specialist to provide remote support as if they were on site. This has resulted in a 30% reduction in time spent on highly difficult maintenance work, which is highly acclaimed by customers.
Contact centers, where the departure from analog channels is in progress
At our contact centers, we accept requests for maintenance, respond to inquiries about operations, accept requests regarding the delivery of consumables, provide a range of machine maintenance services and perform other tasks. At these facilities, we are introducing new digital channels that use AI, in an attempt to solve problems in traditional analog operations which had been done mainly by using telephones.
Taking advantage of the technological progress in recent years, we have enhanced the lineup of digital channels to cater to diverse customer needs. For example, we use an online FAQ and chatbot* to respond to customers who want to solve problems on their own. Another example is an AI operator which responds to customers who want to request the repair of malfunctioning equipment in the middle of the night or on a holiday. Through these channels, we provide highly convenient customer support and have made great achievements in improving the rate of support provided in response to inquiries received via digital channels and the percentage of customers able to find solutions to their problems on their own.
- *Chatbot: A program which enables a computer using an AI to communicate with humans via text or audio
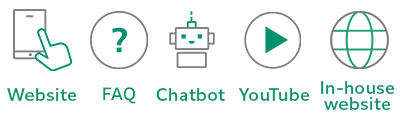
Our lineup of digital channels
Reform of the development and production processes through the full utilization of 3D data
Manufacturing sites, where the on-site confirmation of actual goods has been a basic practice, are also included in the targets of our work style reforms.
To prevent delays in schedules and process rework, which tend to cause cost increases, we worked on front-loading* mass production design, with which quality is developed in the early phases of design. Our design department and production department cooperate by sharing design data, which has resulted in the significant reduction of the frequency of internal rework and the number of returns from suppliers. We have also established a system, in which cost is estimated automatically with a high precision in an early phase using 3D data. This has significantly reduced the number of cases where a product is redesigned to achieve the cost target.
- *Front-loading: Proceeding with tasks, which were done in later processes, at an earlier stage by investing resources in the initial process of product development
Digitalization of contracting process with electronic signatures
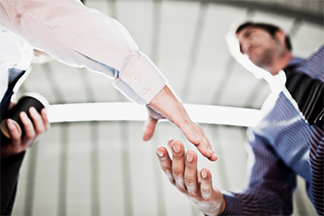
In response to the growing need for digitizing contract preparation and management tasks for faster contract processing, we provide an electronic signature solution helping customers with their business process transformation.
We have also introduced this solution ourselves and it is being expanded to the entire Fujifilm Group. This has enabled efficiency improvement and a significant reduction in the amount of time spent on operations related to the conclusion of contracts. It has also resulted in the reduction of transportation costs and the cost of stamps, as well as enhanced compliance including the reduction of the risk of losing a contract. This solution also permits the affixation of seals at home, saving people the trouble of having to go to the office just to affix a seal. Thus, it enables people to work anywhere.