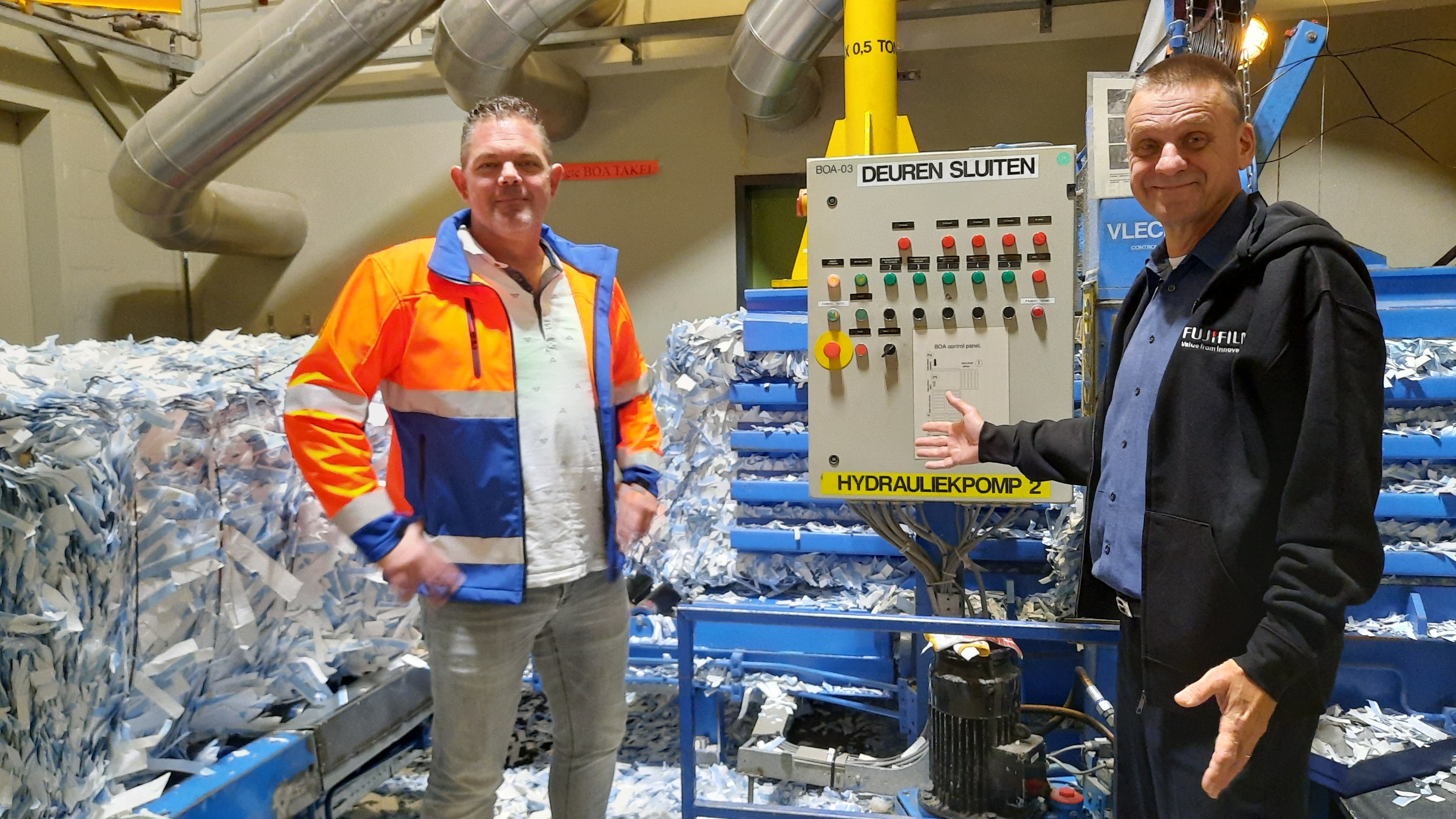
Jos van Dommelen, head of facility services Fujifilm and Daan de Wijs, in-house waste coordinator PreZero at the paper bale press.
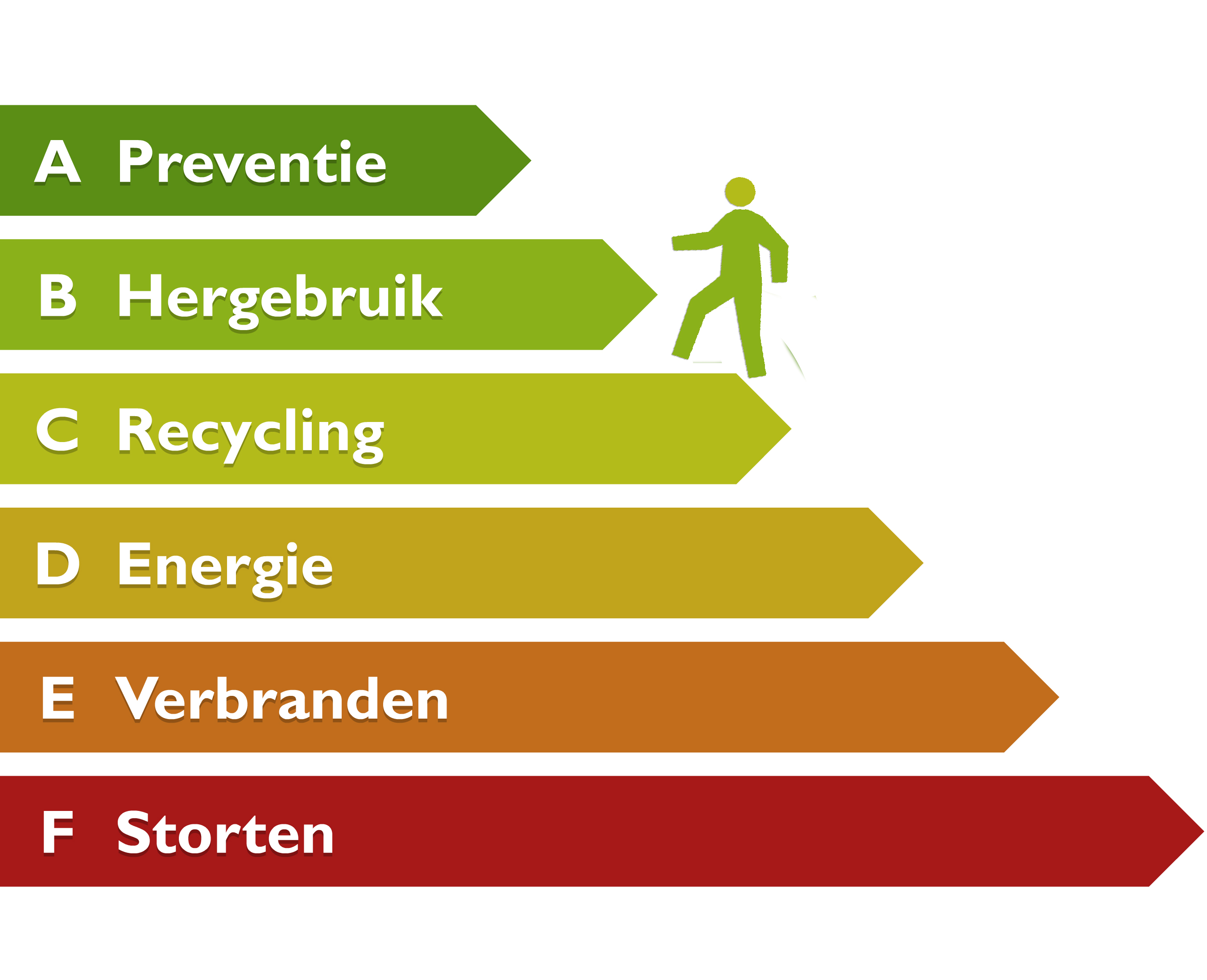
The many waste streams have always been a point of attention at Fujifilm; sustainability and sustainable entrepreneurship are high on our agenda. Fujifilm's 60-acre production site in Tilburg has many different production processes, each with their own waste streams, 95% of which falls under chemicals. Jos van Dommelen, head of facilities services explains: "We aim to process all waste streams as well as possible and go for "Zero landfill". For this we use the Ladder of Lansink, the standard in the field of waste management. We aim for non-use of the lowest step (landfill) and continuously strive for more sustainable processing of our waste and thus a higher position on the ladder. We are proud to say that our way of processing waste puts us on average between the second and third rung of the ladder. There will always be waste streams but we keep improving to stay at least on this position."
Total Waste Management
Starting in 2009, all waste streams have been assigned to one party. We have placed our Total Waste Program with PreZero. What does this mean in practice? Jos: "PreZero is our advisor, service provider and partner in the disposal and coordination of all waste and raw materials. That's a lot for our large production site, we're talking about over 560 different furnished waste streams."
In this partnership, we work together on issues in our waste policy and the best suited solution for each situation. Then it's about the biggest waste streams from the production process: aluminum and silver-containing paper but also about waste separation in the factories and offices. How can we improve our waste processes and make them more efficient? Daan de Wijs, in-house waste coordinator at PreZero explains, "For processing full containers of waste, we have developed a QR code scan. Transports are automatically reported via the QR code and therefore quickly processed in our system, which brings a lot of efficiency to the process for both parties."
Minimale waste with the 5S system
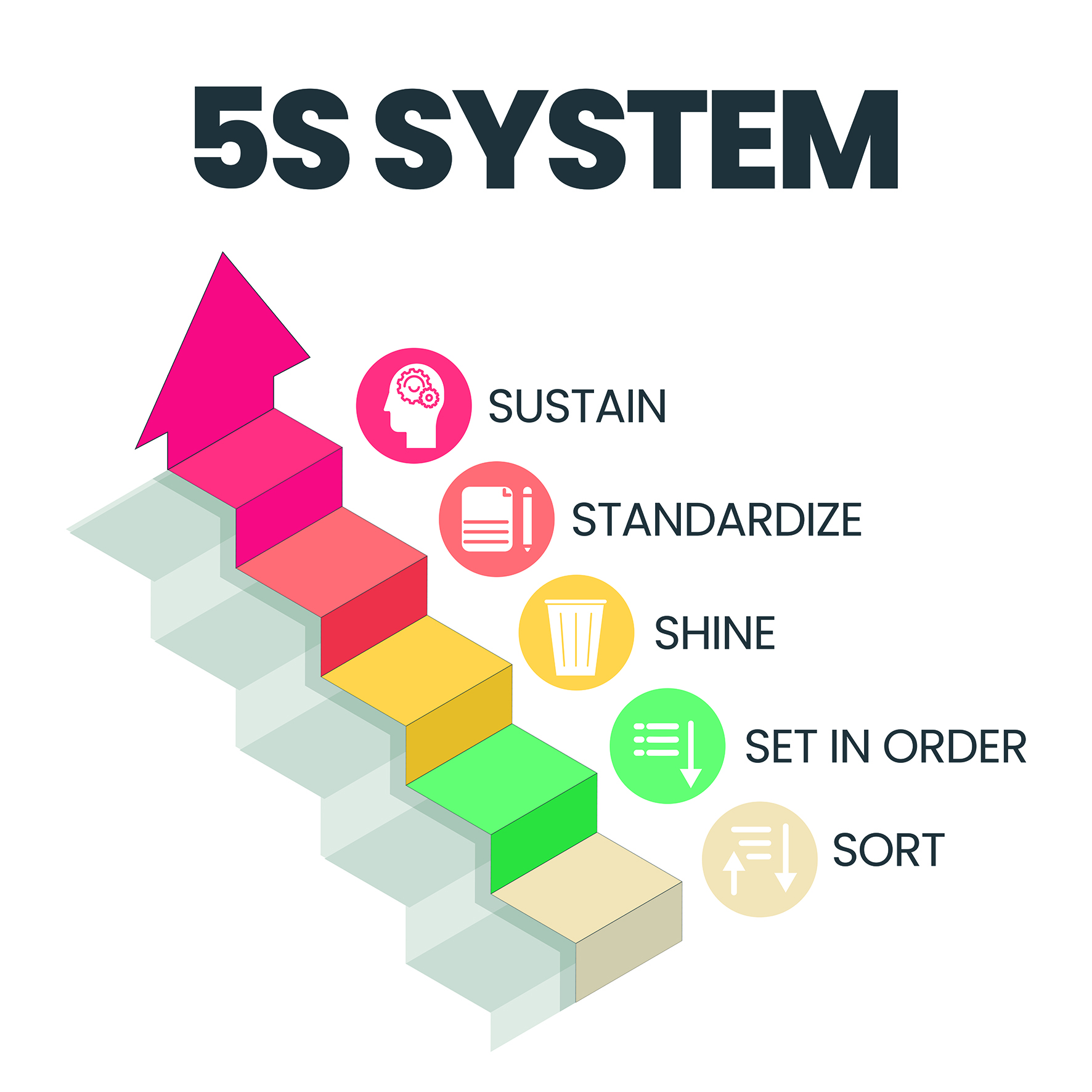
Jos: "As a Japanese company, we often work according to the 5S system at Fujifilm. 5S is a term from the Japanese management philosophy 'Lean Manufacturing', and refers to five Japanese words that describe 'cleaning' or 'tidying up'.
Seiri | Separate |
Seiton | Arrange |
Seiso | Cleaning |
Seiketsu | Standardize |
Shitsuke | Maintain or systematize |
When you work according to the 5S system, one of your goals is to eliminate waste. This way of working, as part of Lean Manufacturing, also helps reduce our waste streams. What this means in broad terms for our waste streams: separate at source, handle separately and keep the environment and materials clean.
Plans for the future
Jos explains: "Every year we look at our current and new waste streams. What processes can we improve and what opportunities do we see to stay high on that ladder?" These are a few examples from the list of topics scheduled to be explored and developed:
- Recycling Fujifilm (disposable) clothing into new products
- Reusing wooden pallets more efficiently
- Disposing of aluminum sulfate through our own water treatment plant to save transportation costs
- Recycling glass-reinforced, polyester cores
We always keep the Fujifilm slogan "Never Stop innovating for a healthier world" in mind. We will never stop striving for more sustainable processing of our waste streams.
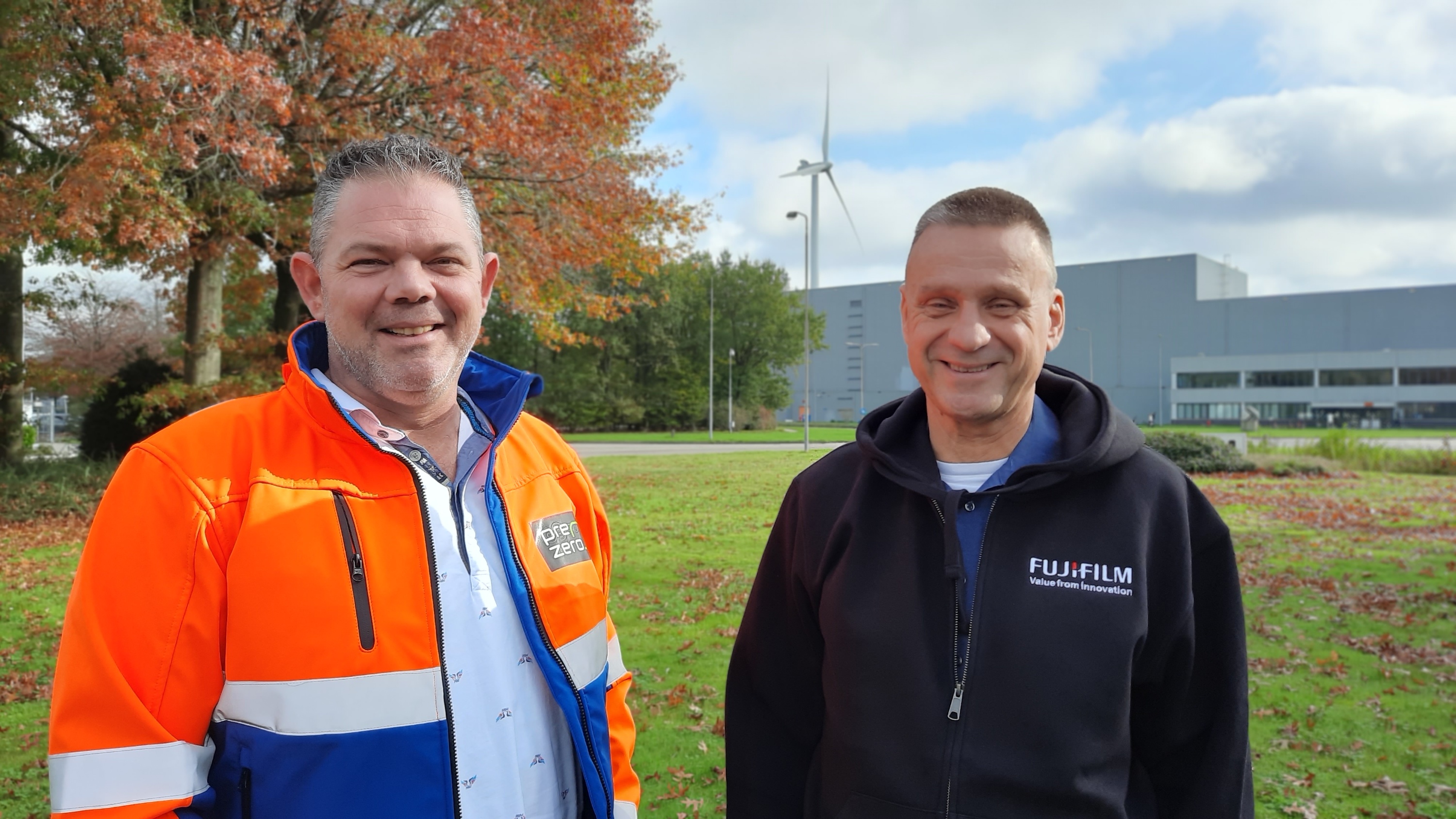