What is a filtration membrane?
This page offers basic information on filtration membrane, explaining its characteristics.
About filtration membrane
Filtration involves separation of liquid or gas, in which the feed stream is divided into permeate and retentate when processed through a certain medium. There are different types of filtration, filtration medium being one of the classifications, such as membrane filtration.
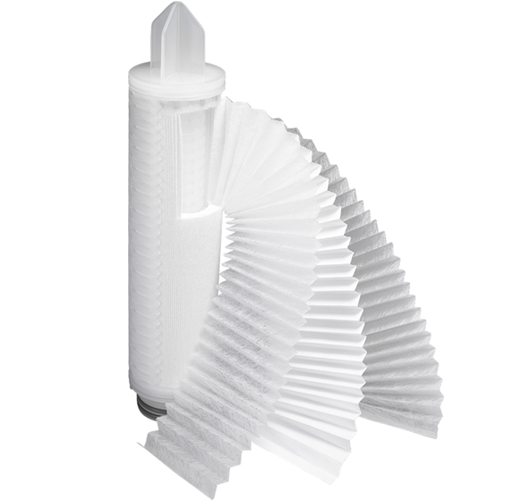
Method of membrane filtration and its function
What is a membrane? Membrane acts as a barrier that allows the separation. Although the appearance may look like a sheet of paper, membrane filters are made up of numerous micro-sized pores, which particles larger than a defined rating are retained when a liquid or gas is passed through.
Membrane filter principle and its construction
Membrane filters come in different sizes and shapes, from cartridges, capsules, disks, etc. Fujifilm offers broad lineup of pleated membrane cartridges and capsules.
Types of filtration (Absolute type vs Nominal type)
Filters can be classified into different categories, such as “absolute” type and “nominal” type depending on their filtration method and their structure. The nominal type filters are well known as depth filters, in which microfibers are randomly tangled. When the liquid is filtered through the medium, particles are retained through adhesion on fiber. On the other hand, absolute type typically has numerous micro-sized pores inside a synthetic resin film or membrane, which enables particles larger than a defined size to be trapped. In case of depth filters, process conditions such as operating pressure or concentration of contaminant have a significant effect on the retention of the filter. Therefore, depth filters are mainly used as pre filtration, whereas membrane filters are used as absolute filtration, where particles larger than the defined rating have to be retained. There are cases where multiple filtration steps are installed, for example in the case of mineral water. Absolute type filters are used right before the packaging to ensure its safety, making sure that harmful organisms or any contaminants are removed from the bottled water. However, nominal filters are usually placed beforehand to remove bigger particles first and reduce the blockage of final filters.It is recommended to use the appropriate filter which follows the type of filtration required in the process.
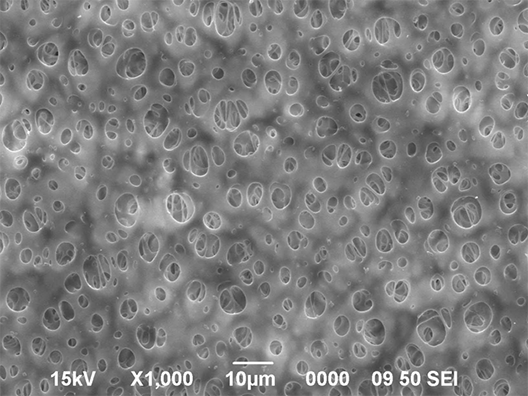
Electron microscope image of absolute type membrane
(Polysulfone material)
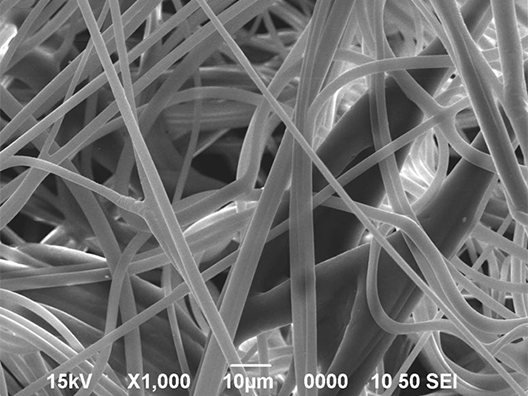
Electron microscope image of nominal type membrane
(Polyproplyene material)
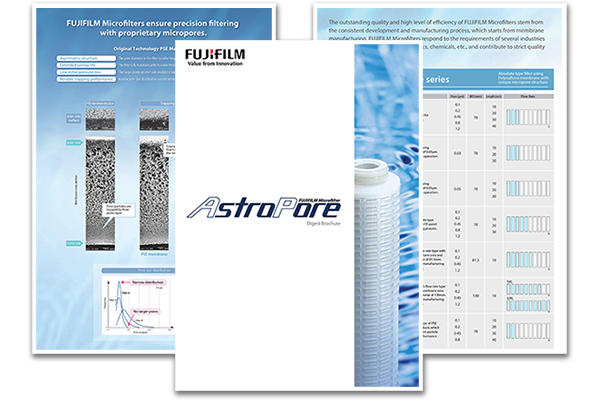
Downloads
Comprehensive brochure includes…
- Characteristics of Fujifilm membrane filter
- Lineup of Fujifilm cartridge series
- Suitable applications for each series
Advantages of membrane filtration
Membrane filtration is installed for many purposes, such as cost down on operational costs or improvement on product quality. Membrane filtration systems are often very simple, making it less expensive compared to other alternative systems. Not only during the installation, membrane filters do not leave residue such as filter cake, reducing disposal cost. In addition, installment of high quality filtration system leads to improvement on product quality, allowing safe and stable product to be distributed to customers.
Are membrane filters only used for filtration of water? What are its uses?
Membrane filters in the form of pleated cartridges are used at filtration processes for food and beverage (such as beer, wine, bottled water and dairy products), pure water or chemical solutions used in manufacturing of electronics devices and semiconductors, process water/industrial water used in pharmaceutical and other various industrial sites.

Examples of applications:
- Food and beverage (beer, wine, bottled water, dairy produtcs, etc)
- Biotechnology (amino acids, enzymes, etc)
- Pharmaceutical (process water, pure water)
- Electronics, semiconductor (industrial water, pure water)
Types of membrane filtration method and its purification classifications
Membrane filters for microfiltration (MF)
Microfiltration (MF) is defined as a process of membrane separation which removes particles with sizes varying from 0.01 to 10μm. Micro filter is another term used to describe the filters used for microfiltration.
Other membrane filter method
Other than microfiltration, there are different types of membrane filters used in separation processes. They are classified depending on its capability of filtering target. Ultrafiltration (UF) has the pore size of 0.01μm, targeted to remove viruses along with microorganisms. Nanofiltration (NF) removes not only the viruses but also divalent ions, with membrane pore size of 0.001μm. Reverse Osmosis filters (RO) is mainly used as desalination and purification of water with its pore size range up to 0.0001μm,with water being the only material that can pass through the membrane.
Membrane filter material
Membrane filtration is one of the methods of sterilization when heat sterilization cannot be performed. As sizes of bacteria ranges from 0.3μm to 0.5μm, pore size of a sterile membrane filter is generally 0.2μm, as it is suitable for removing contaminating microorganisms. Membrane materials such as Polysulfone (PS/PSF), Polyethersulfone (PES), Polyvinylidene fluoride (PVDF), Polytetrafluoroethylene (PTFE) and Nylon are commonly used. Membrane properties vary depending on its material features along with its pore distribution. Therefore, it is important to select the type the membrane that is suitable for its usage conditions.
Polysulfone (PSF) and Polyethersulfone (PES) membranes share similar features, where they have resistance to acidic and alkaline solutions with low extractables. They are also known to have thermal stability and low protein binding. They are commonly used in various industrial fields from F&B, semiconductors to pharmaceutical.
Polytetrafluoroethylene (PTFE) membranes have compatibility to a broad range of chemicals with high thermal resistance. With its resistance to chemical solutions, hydrophilic PTFE membranes are applied to filter fluids such as organic solvents and aggressive solvents, whereas hydrophobic PTFE membranes are mainly used for filtering gases.
Nylon membranes have resistance to broad range of organic solvents along with its hydrophilicity, flexibility and low elution rate characteristics.
Polyvinylidene fluoride (PVDF) membranes offer durability and resistance in broad chemical solutions with low extractables. With its low protein binding feature and hydrophilic features, PVDF filters are commonly used as final filters for bioburden reduction in pharmaceutical applications.
Polypropylene (PP) membranes are known for its compatibility with alkaline solutions and its thermal resistance. PP filters are commonly used for general clarification or prefiltration, in order to capture particles to reduce the burden of final filtration that follows.
Fujifilm has a long experience in the manufacturing of Polysulfone membranes, offering broad lineup of cartridge filters suitable for each application.
Fujifilm membrane filter size, spec and other features
Fujifilm filters come in various sizes and different end caps that fit with the corresponding housing. Fujifilm has its own end cap code, explained in the chart below.
Fujifilm end cap codes | |||||
---|---|---|---|---|---|
G Type | P Type | M Type | MP Type | PM Type | |
O ring size*1 | ― | 226 | 222 | 222 | 226 |
Shape | DOE*2 | SOE*3 | SOE*3 | SOE*3 | SOE*3 |
Spear / Fin | ― | 〇 | ― | 〇 | ― |
Twist lock | ― | 〇 | ― | ― | ― |
- *1 O ring size:SAE AS568(US standard)
- *2 DOE:Double Open End ・・・Filter with flat gasket seals on both open ends.
- *3 SOE:Single Open End
For more information on its feature and its specifications, refer to the product catalog.
Membrane filter price
Please send a request through the contact form for quotations.